Table of Contents
KanBo – The Pharma-Focused Work Coordination Maestro
Experience ultimate task alignment, communication and collaboration
Trusted globally, KanBo, bridges the gap between management and engineering in complex pharmaceutical organizations. Seamless coordination, advanced project planning, and outstanding leadership are made possible through our versatile software. Stride toward your mission-critical goals with superior collaboration and communication.
KanBo Quality Engineer ECO Trending and Investigations: Navigating Collaboration in Pharmaceutical Quality Control
What do readers need to know about this challenge?
Within the pharmaceutical industry, maintaining environmental control (ECO) is critical for aseptic production. A significant challenge for Quality Engineers specializing in ECO Trending and Investigations is the need to perform exhaustive investigations of ECO deviations while collaborating with diverse departments. This task entails identifying root causes, assessing impacts, and ensuring effective corrective and preventive actions are taken.
What readers can do with KanBo to solve this challenge?
- Space: Create a central hub for all ECO-related activities, facilitating interdepartmental communication and documentation storage.

- Card: Represent each ECO deviation investigation as a card to manage and track progress efficiently.

- Card activity stream: Gain visibility into the real-time updates and actions taken on each investigation for complete transparency.
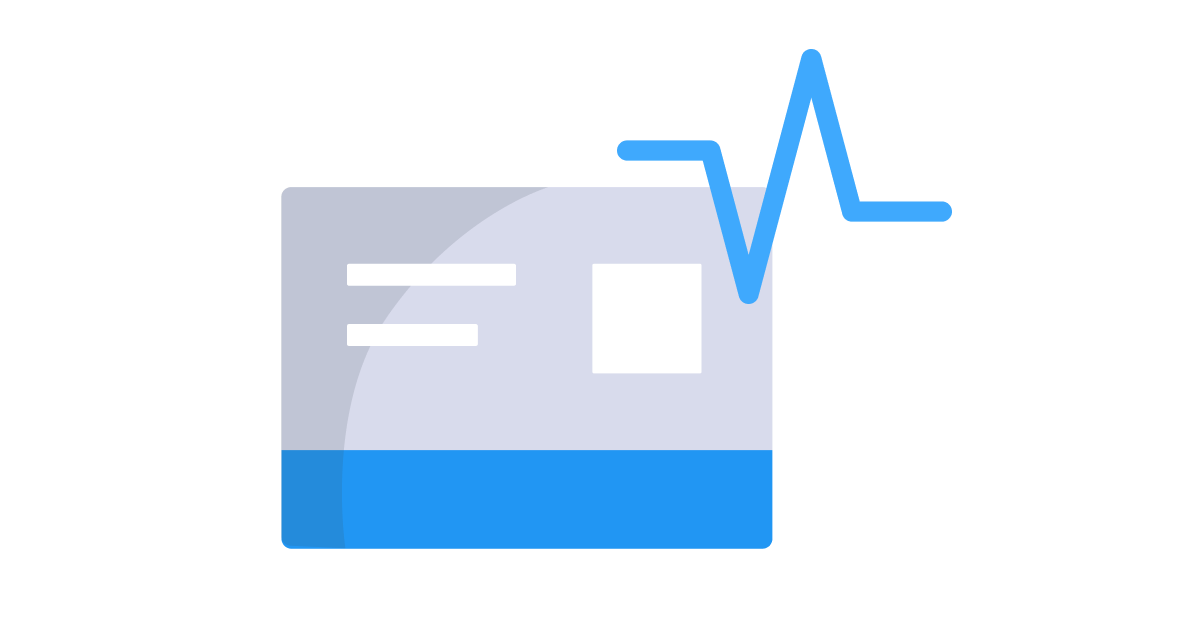
- Card status: Track the progress of each ECO investigation by categorizing cards based on their current status, enabling a structured follow-up process.
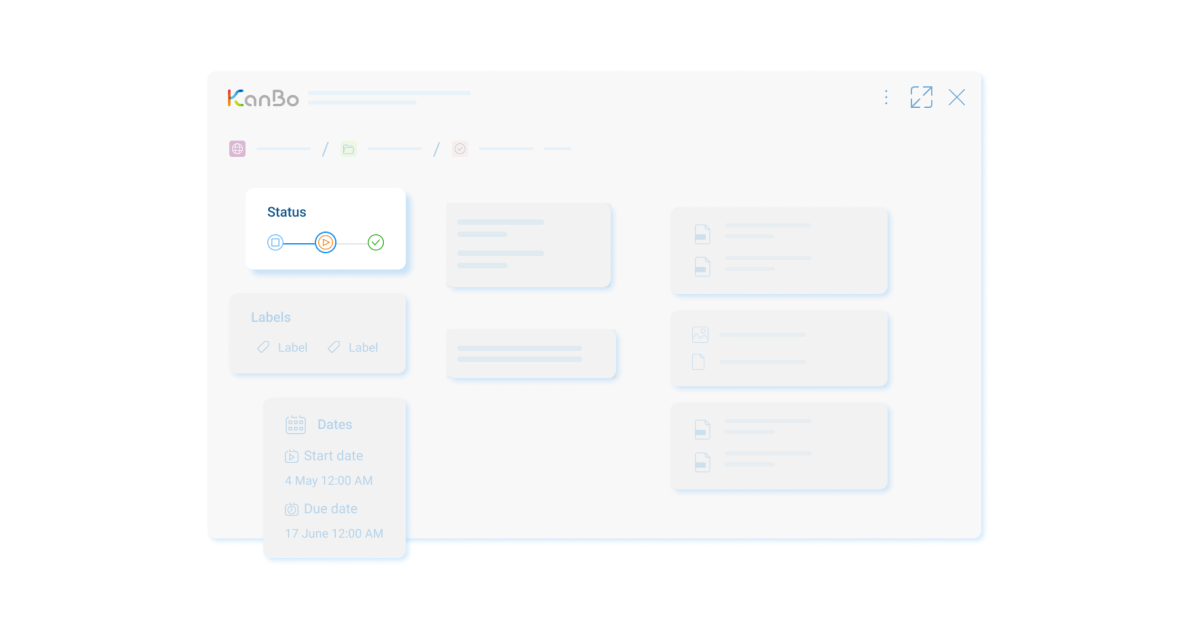
- Trending of ECO deviations: Use the Table view to categorize and analyze recurring ECO issues for pattern identification and long-term solutions.
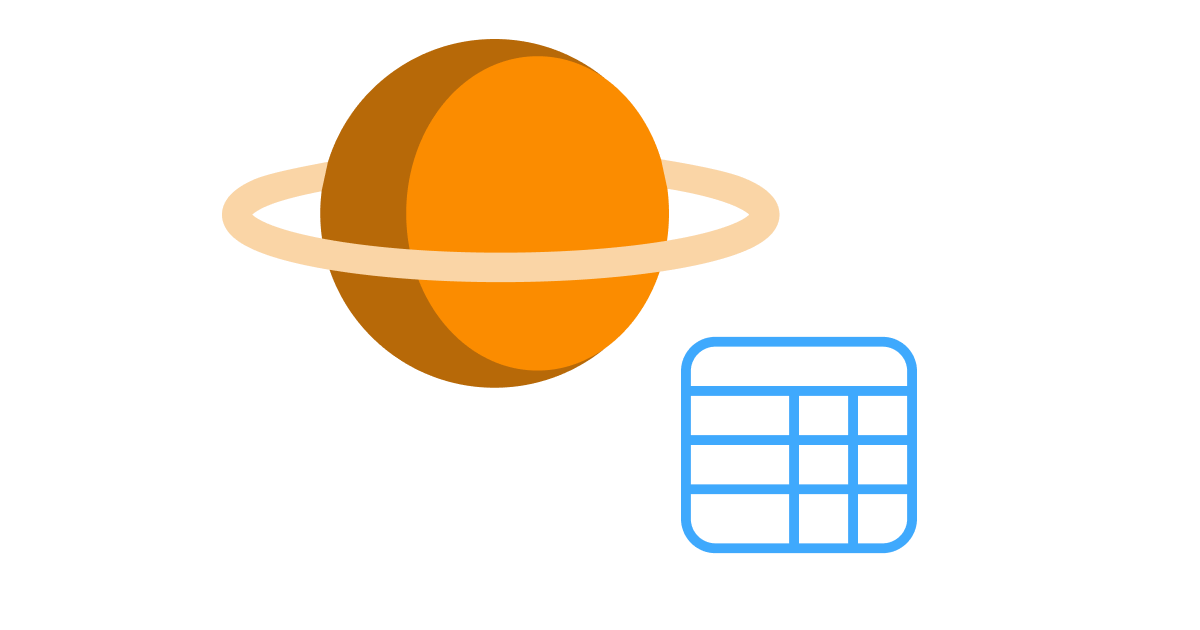
- Grouping: Group ECO deviations by type, department, or root cause for organized and effective monitoring.
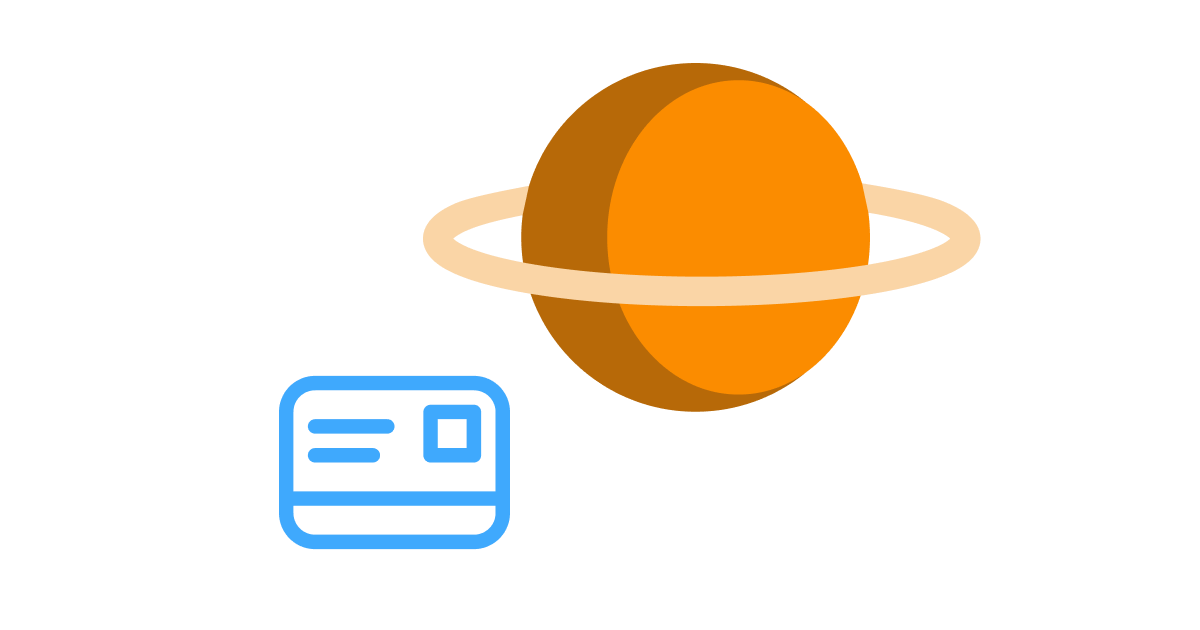
- Filtering cards: Filter cards by various criteria such as deadlines, involved teams, or deviation type to streamline investigations.
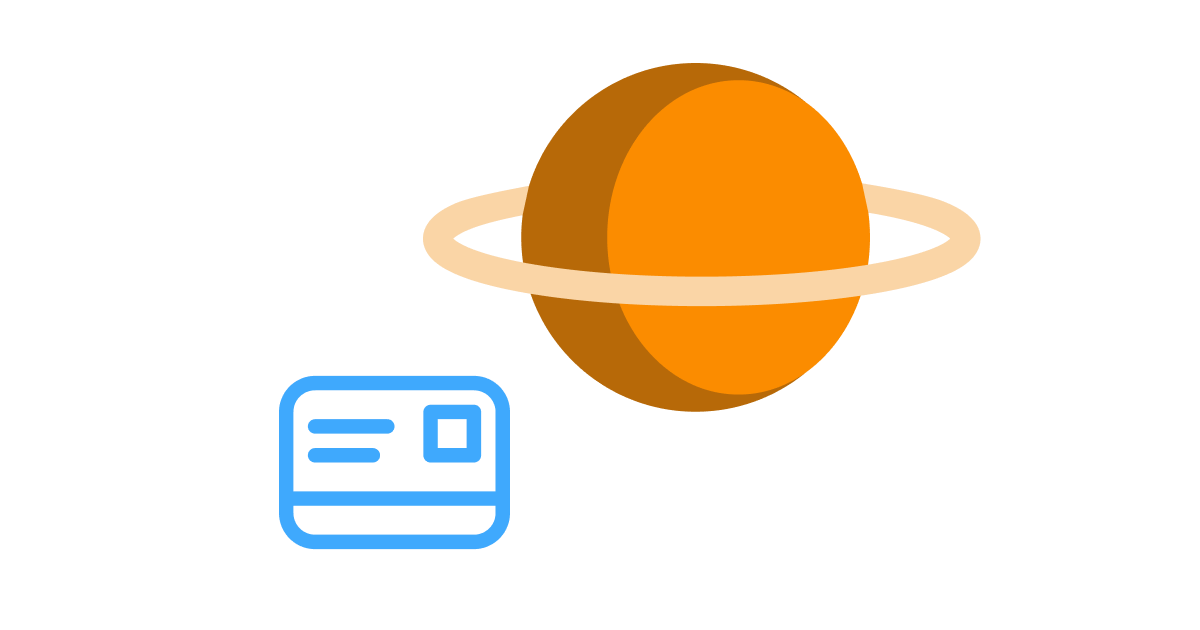
- Gantt Chart view: Visualize investigation timelines of ECO deviations and the implementation schedules for corrective/preventive actions.
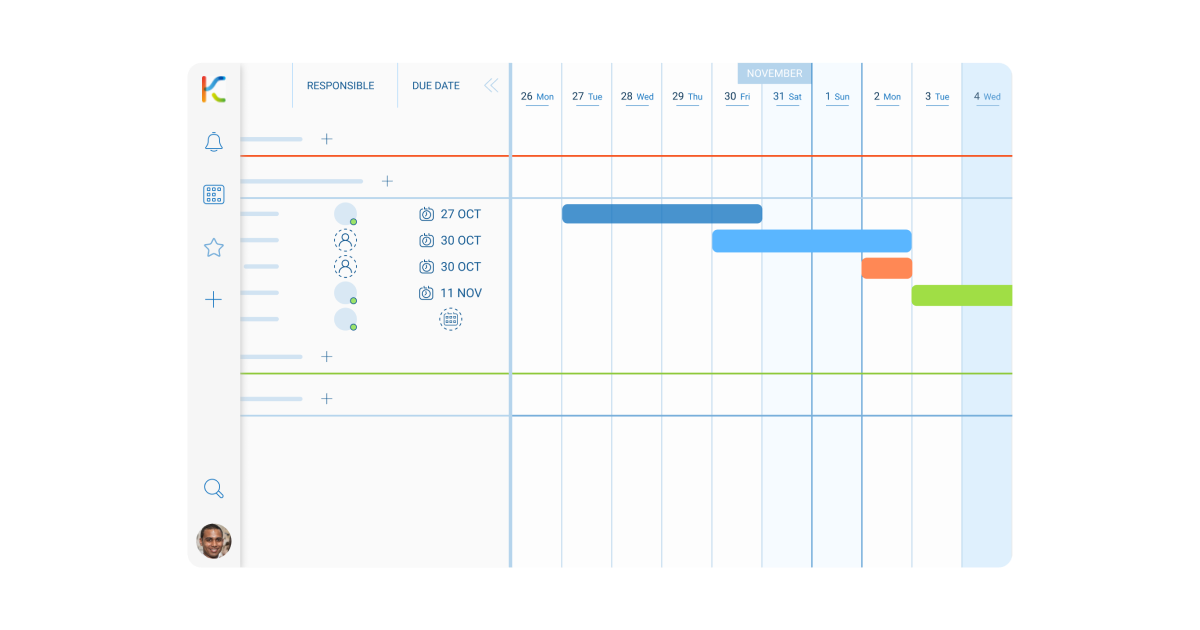
- Notification: Receive timely updates on critical changes or completion of investigation steps to keep all stakeholders informed.
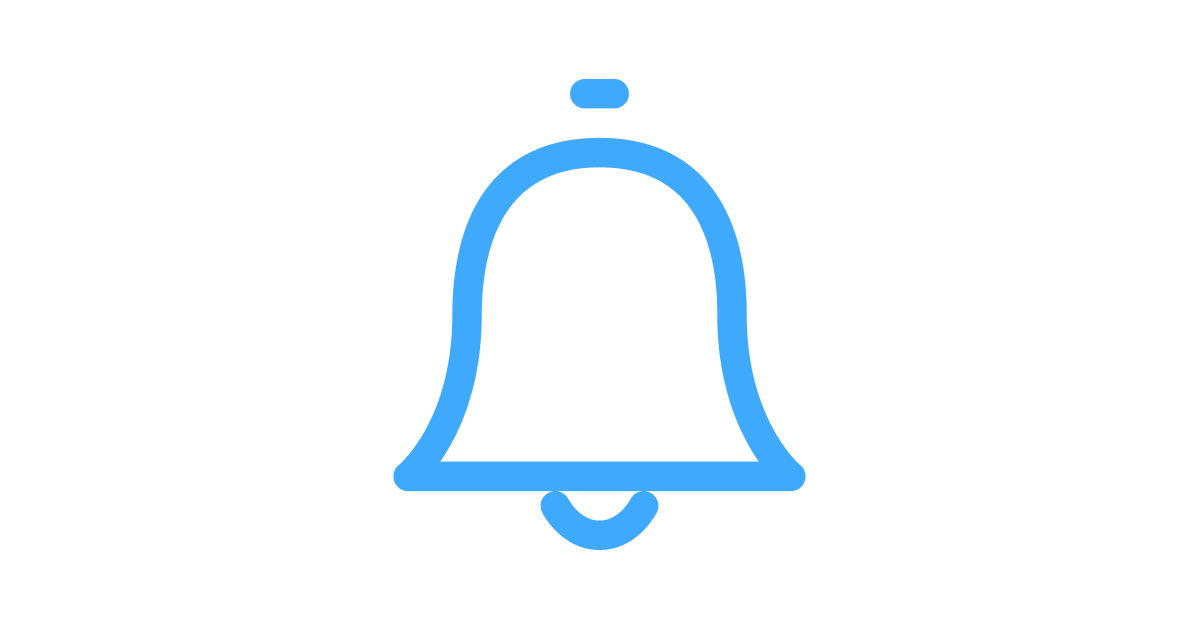
What readers can expect after solving this challenge?
By utilizing KanBo's suite of features for managing ECO Trending and Investigations, organizations can expect to achieve efficient and effective quality control collaboration. The clarity and insight offered by KanBo's organized structure help ensure that responses to ECO deviations are swift and comprehensive. In the long term, this organized approach can lead to a reduction in production halts due to environmental issues, enhance compliance with Good Manufacturing Practices (GMP), and establish a culture of continuous improvement and quality assurance. As the platform evolves, new features may be introduced that further streamline the collaboration process, including improved AI-driven analytics for root cause analysis and predictive trend assessments for proactive quality management.
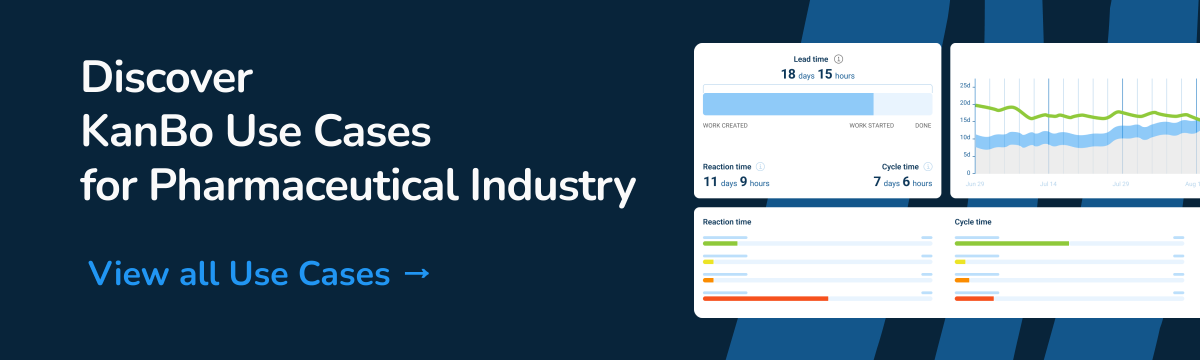
Table of Contents
KanBo – The Pharma-Focused Work Coordination Maestro
Experience ultimate task alignment, communication and collaboration
Trusted globally, KanBo, bridges the gap between management and engineering in complex pharmaceutical organizations. Seamless coordination, advanced project planning, and outstanding leadership are made possible through our versatile software. Stride toward your mission-critical goals with superior collaboration and communication.
KanBo Quality Engineer ECO Trending and Investigations: Navigating Collaboration in Pharmaceutical Quality Control
What do readers need to know about this challenge?
Within the pharmaceutical industry, maintaining environmental control (ECO) is critical for aseptic production. A significant challenge for Quality Engineers specializing in ECO Trending and Investigations is the need to perform exhaustive investigations of ECO deviations while collaborating with diverse departments. This task entails identifying root causes, assessing impacts, and ensuring effective corrective and preventive actions are taken.
What readers can do with KanBo to solve this challenge?
- Space: Create a central hub for all ECO-related activities, facilitating interdepartmental communication and documentation storage.

- Card: Represent each ECO deviation investigation as a card to manage and track progress efficiently.

- Card activity stream: Gain visibility into the real-time updates and actions taken on each investigation for complete transparency.
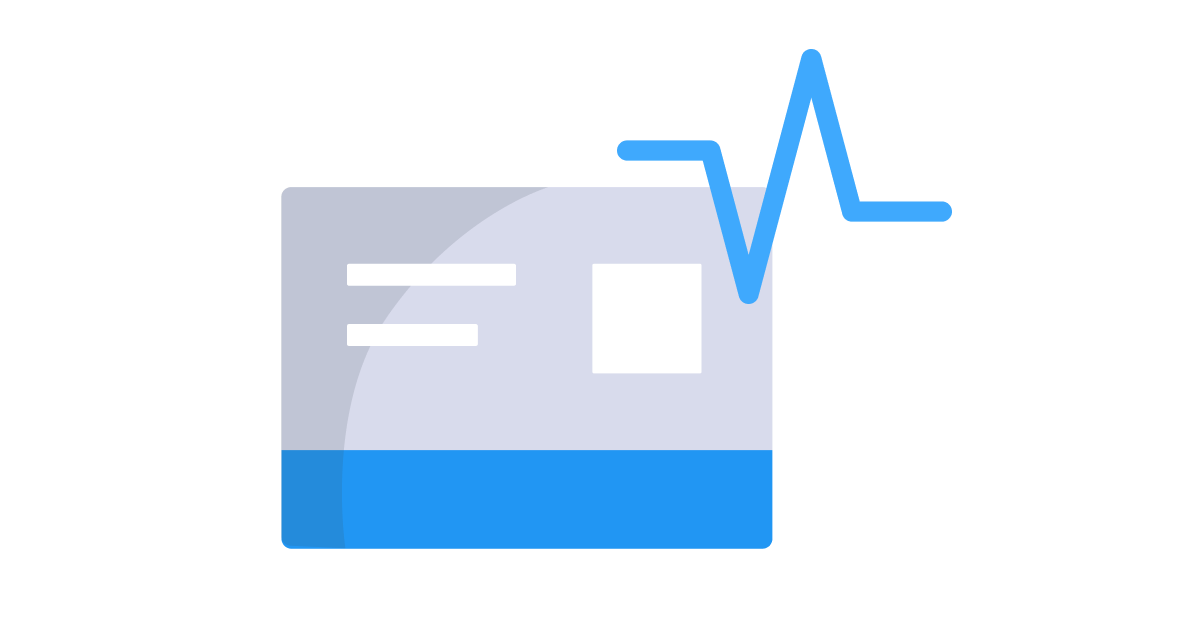
- Card status: Track the progress of each ECO investigation by categorizing cards based on their current status, enabling a structured follow-up process.
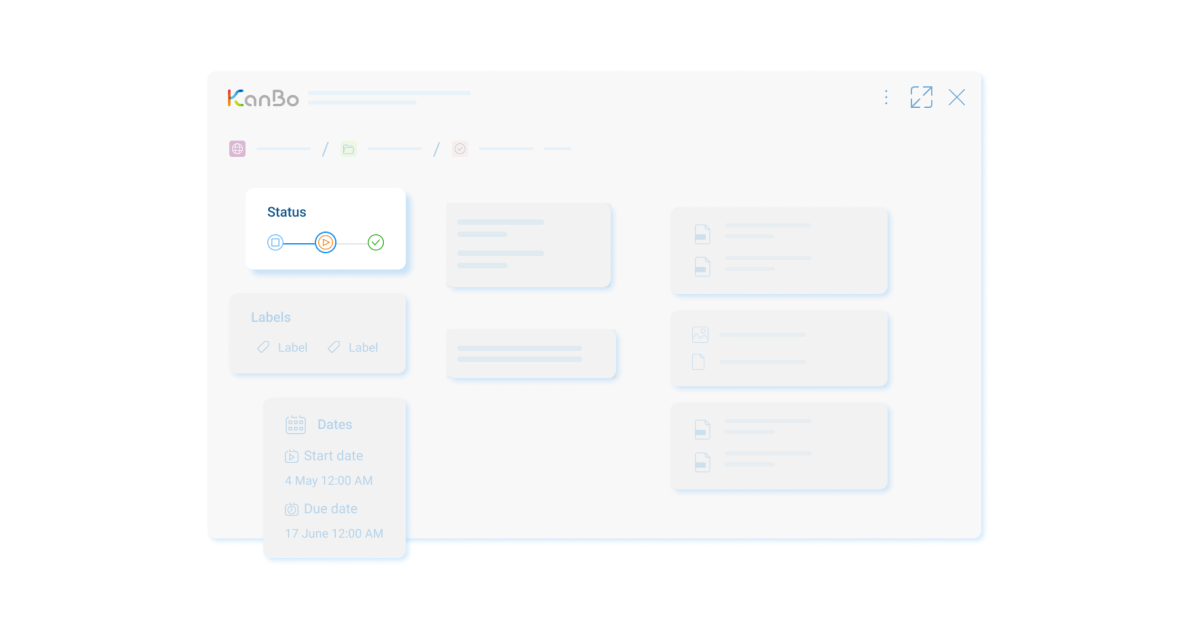
- Trending of ECO deviations: Use the Table view to categorize and analyze recurring ECO issues for pattern identification and long-term solutions.
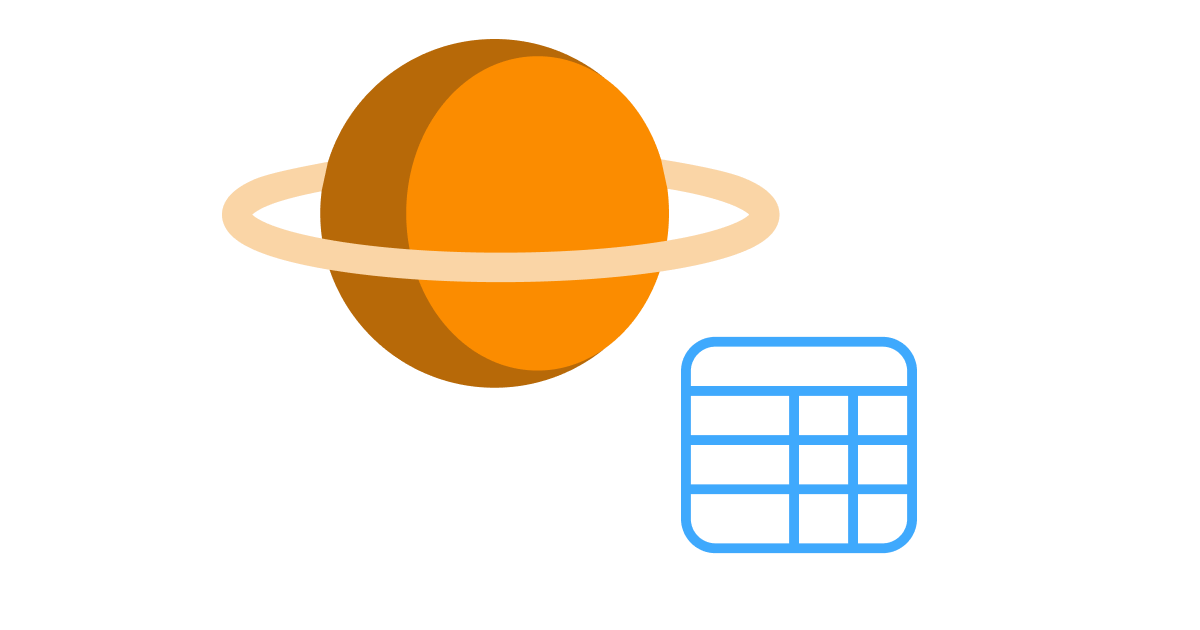
- Grouping: Group ECO deviations by type, department, or root cause for organized and effective monitoring.
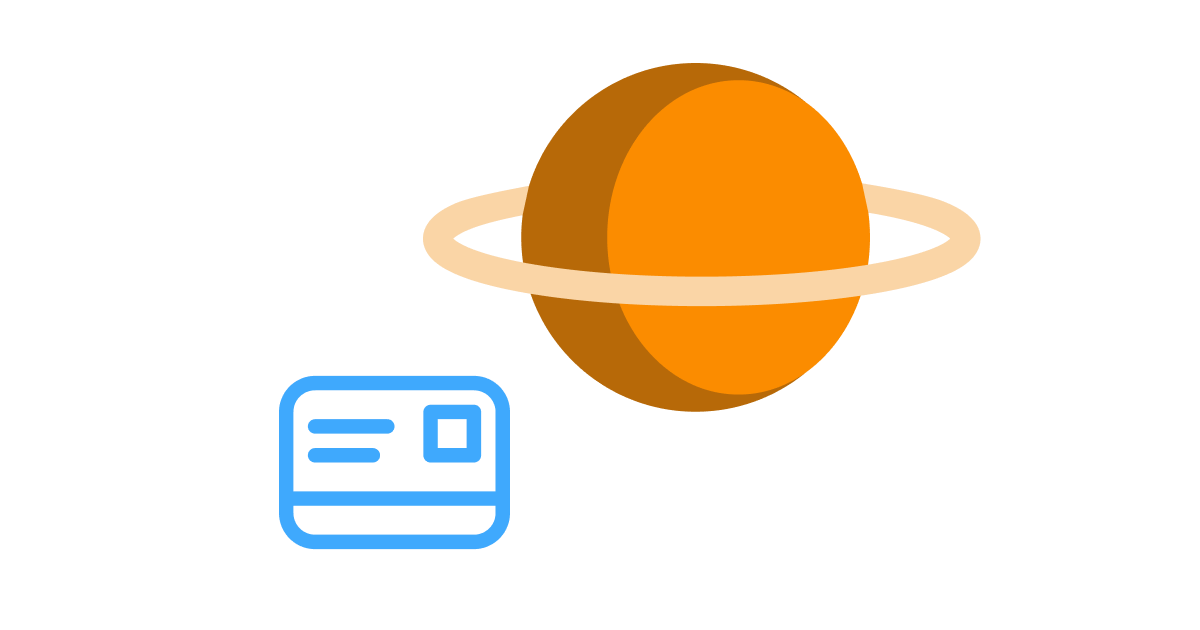
- Filtering cards: Filter cards by various criteria such as deadlines, involved teams, or deviation type to streamline investigations.
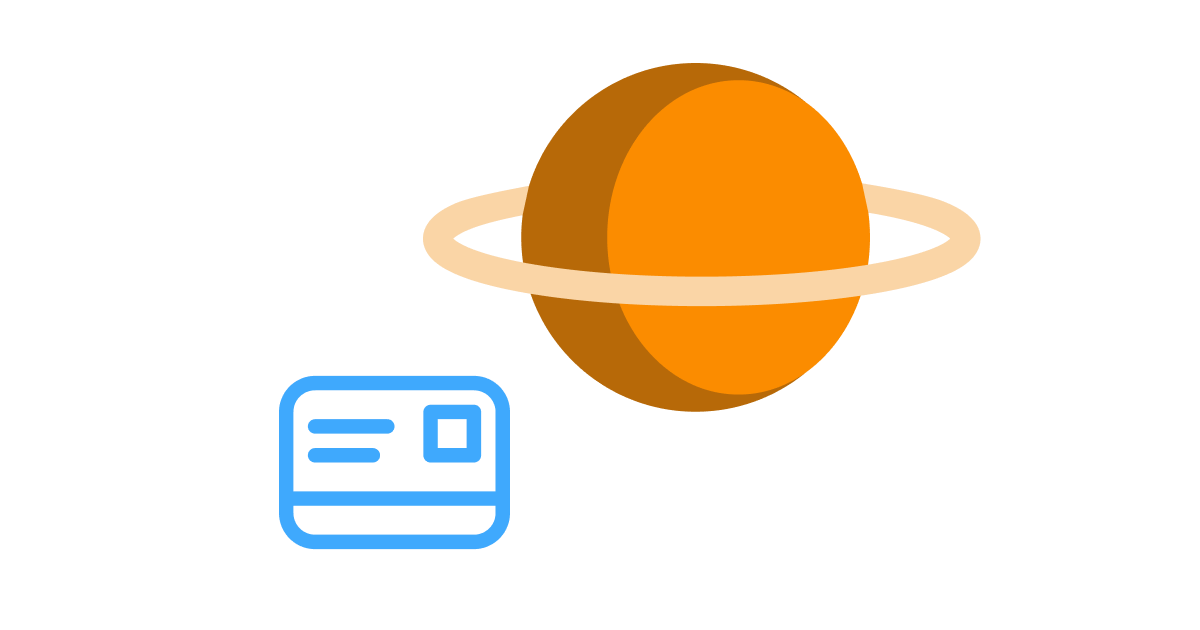
- Gantt Chart view: Visualize investigation timelines of ECO deviations and the implementation schedules for corrective/preventive actions.
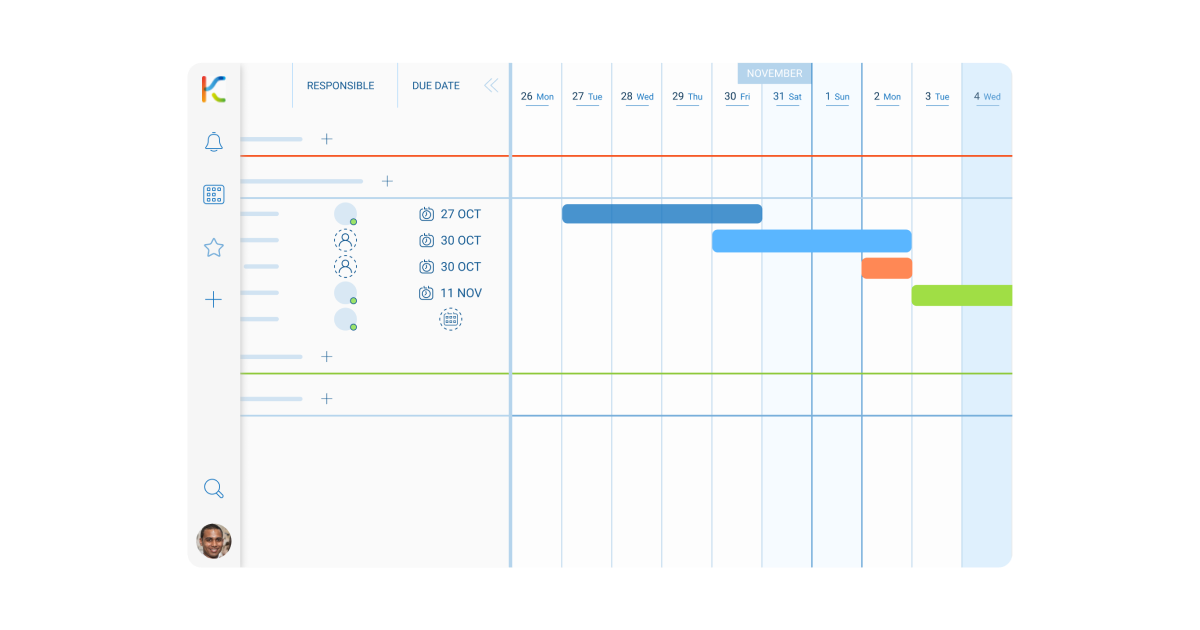
- Notification: Receive timely updates on critical changes or completion of investigation steps to keep all stakeholders informed.
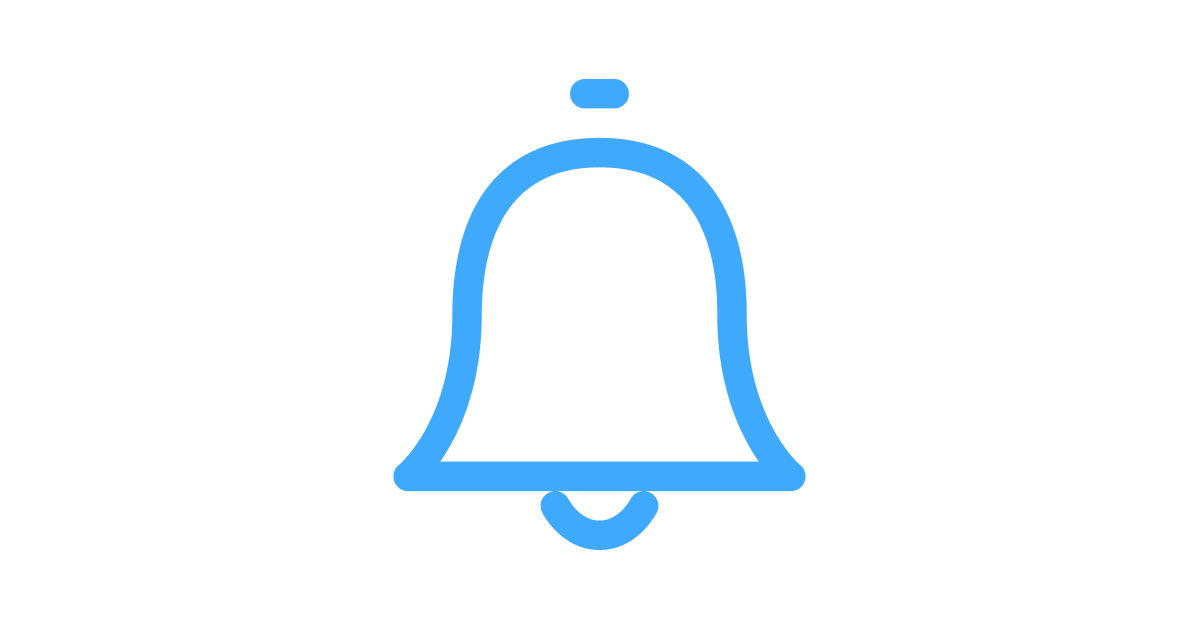
What readers can expect after solving this challenge?
By utilizing KanBo's suite of features for managing ECO Trending and Investigations, organizations can expect to achieve efficient and effective quality control collaboration. The clarity and insight offered by KanBo's organized structure help ensure that responses to ECO deviations are swift and comprehensive. In the long term, this organized approach can lead to a reduction in production halts due to environmental issues, enhance compliance with Good Manufacturing Practices (GMP), and establish a culture of continuous improvement and quality assurance. As the platform evolves, new features may be introduced that further streamline the collaboration process, including improved AI-driven analytics for root cause analysis and predictive trend assessments for proactive quality management.
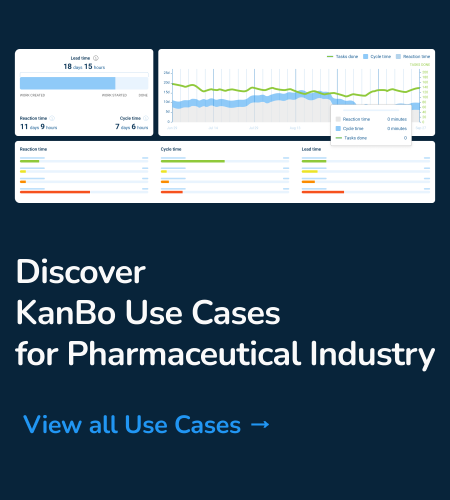