Table of Contents
KanBo – The Pharma-Focused Work Coordination Maestro
Experience ultimate task alignment, communication and collaboration
Trusted globally, KanBo, bridges the gap between management and engineering in complex pharmaceutical organizations. Seamless coordination, advanced project planning, and outstanding leadership are made possible through our versatile software. Stride toward your mission-critical goals with superior collaboration and communication.
KanBo Quality Specialist Operations in Pharmaceutical Industry: Navigating Collaboration Challenges
What do you need to know about this challenge?
In the pharmaceutical industry, collaboration challenges for a Quality Specialist Operations involve maintaining seamless coordination among different departments like manufacturing, Quality Control (QC), and support functions to ensure product quality and regulatory compliance. It's critical to track quality incidents, facilitate efficient root cause analysis, and ensure timely completion of corrective and preventive actions.
What can you do with KanBo to solve this challenge?
KanBo's features provide a powerful solution to the collaboration challenges faced by Quality Specialist Operations:
- Space: Create specific spaces for each department or quality project, allowing for segregated yet interconnected areas of focus.

- Cards: Represent each quality incident or action item as a card to monitor progress and accountability.

- Card activity stream: Keep a real-time record of all actions taken on a card, enhancing transparency and aiding in investigations.
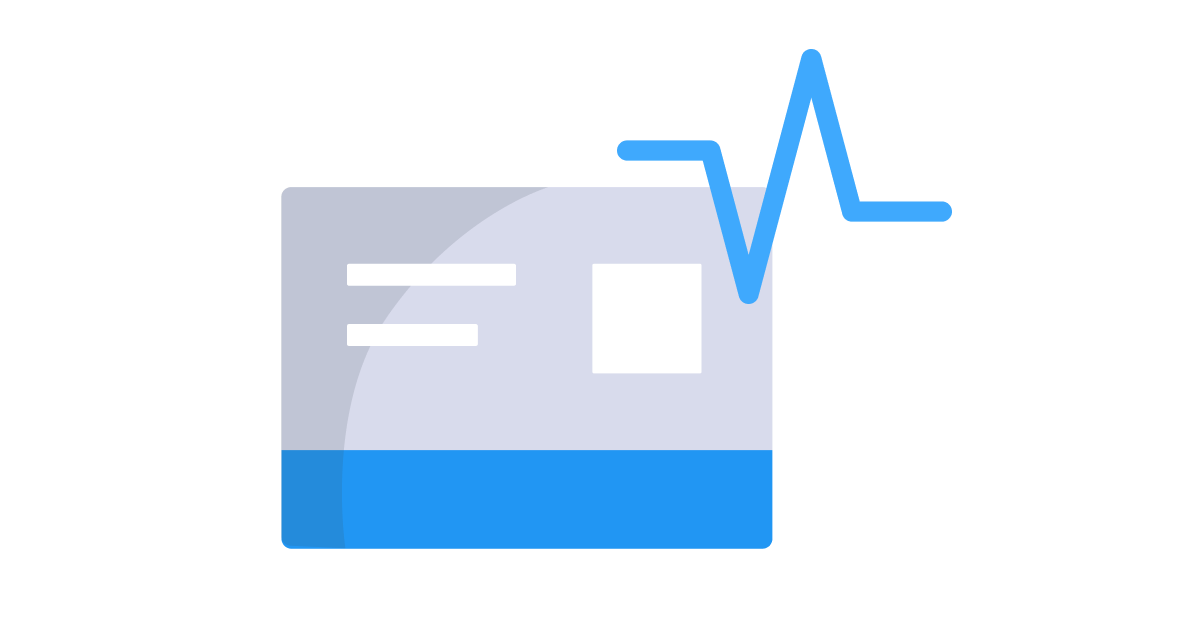
- Calendar view: Use this view to track and manage deadlines for quality checks, audits, and compliance-related activities.
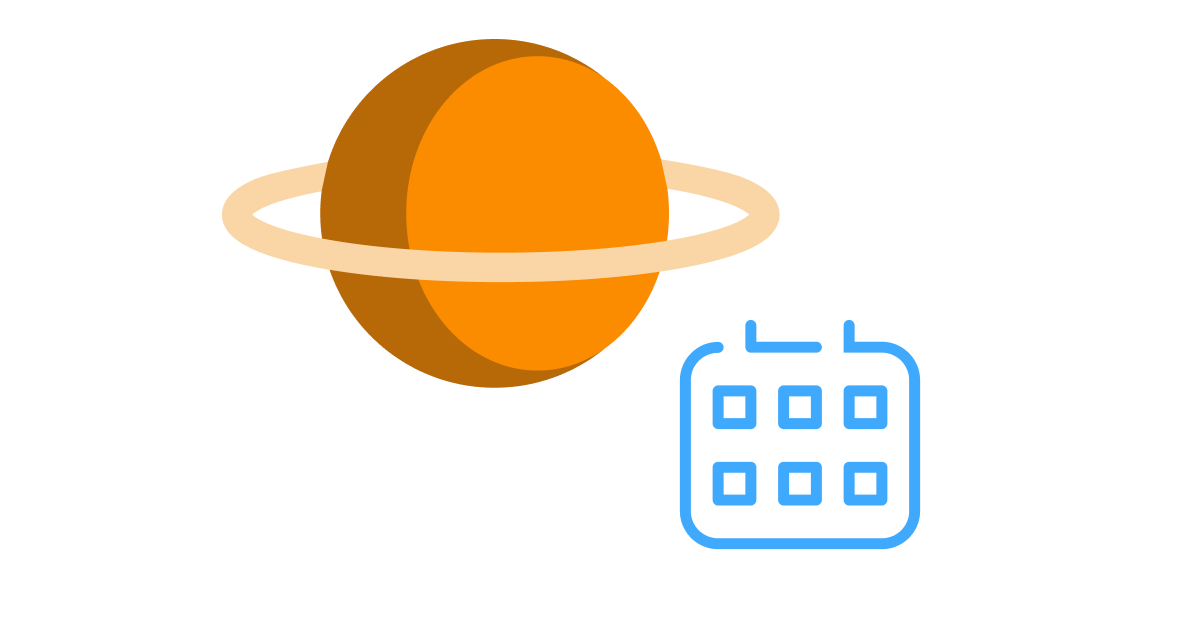
- Card relation: Connect related cards to clarify dependencies, especially between corrective actions and quality incidents.

- Grouping: Organize cards related to quality issues under groupings such as incident type, product line, or urgency.
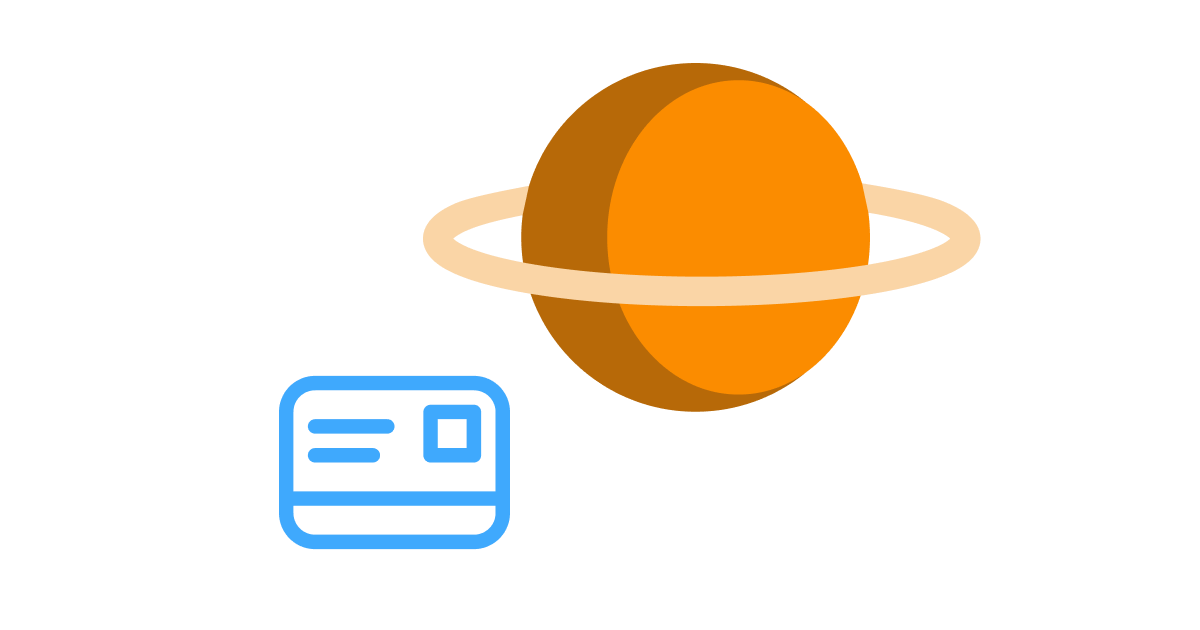
- Notification: Receive alerts on updates and changes to stay informed about the quality-related activities within your space.
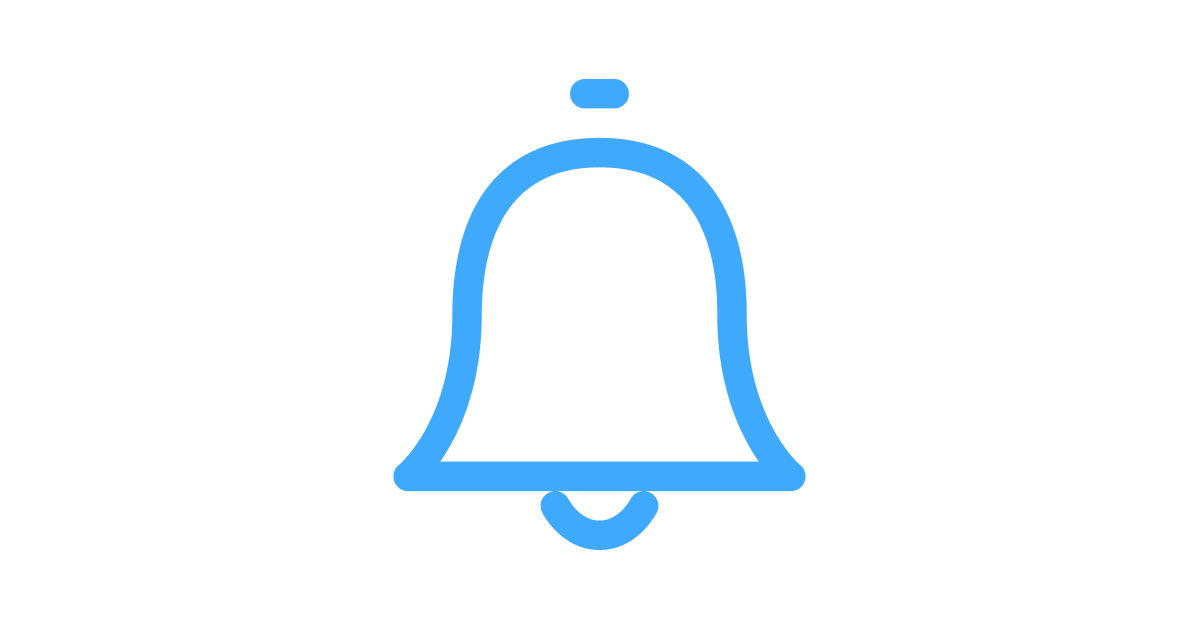
- KanBo Search: Find any critical quality document or discussion quickly with advanced search capabilities.
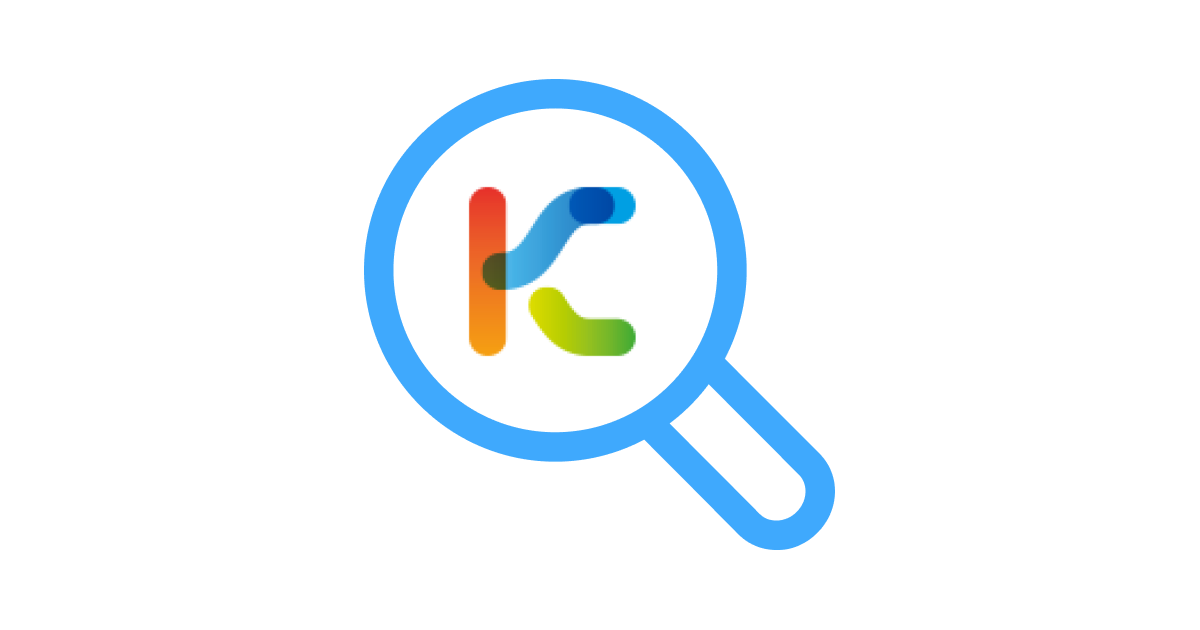
What can you expect after solving this challenge?
Implementing KanBo for collaboration challenges in pharmaceutical Quality Specialist Operations leads to long-term benefits, such as enhanced product quality, compliance with regulatory standards, and improved teamwork efficiency. By leveraging KanBo, operations can achieve streamlined communication, a centralized platform for all quality incidents, and proactive management of quality deviations. Future enhancements may include more advanced analytics for predicting quality trends, integration with additional quality management tools, and more sophisticated automation of quality processes. With KanBo, Quality Specialist Operations can not only resolve current collaboration challenges but also establish a more proactive and efficient quality management system for the future.
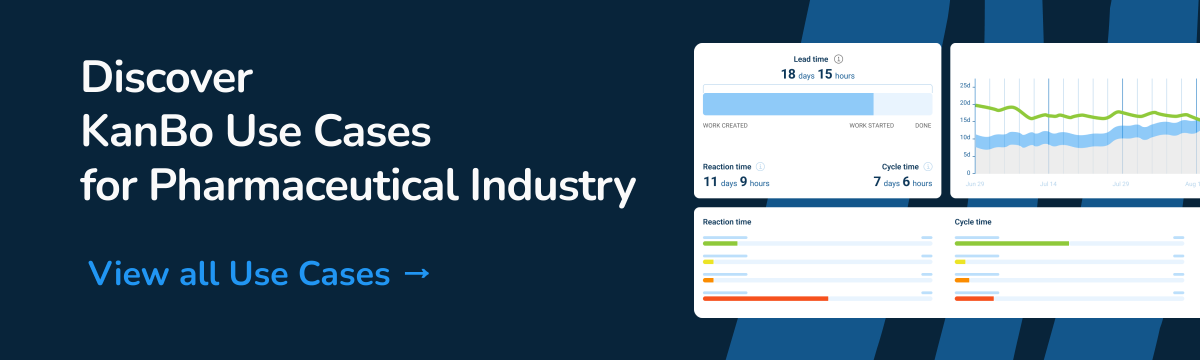
Table of Contents
KanBo – The Pharma-Focused Work Coordination Maestro
Experience ultimate task alignment, communication and collaboration
Trusted globally, KanBo, bridges the gap between management and engineering in complex pharmaceutical organizations. Seamless coordination, advanced project planning, and outstanding leadership are made possible through our versatile software. Stride toward your mission-critical goals with superior collaboration and communication.
KanBo Quality Specialist Operations in Pharmaceutical Industry: Navigating Collaboration Challenges
What do you need to know about this challenge?
In the pharmaceutical industry, collaboration challenges for a Quality Specialist Operations involve maintaining seamless coordination among different departments like manufacturing, Quality Control (QC), and support functions to ensure product quality and regulatory compliance. It's critical to track quality incidents, facilitate efficient root cause analysis, and ensure timely completion of corrective and preventive actions.
What can you do with KanBo to solve this challenge?
KanBo's features provide a powerful solution to the collaboration challenges faced by Quality Specialist Operations:
- Space: Create specific spaces for each department or quality project, allowing for segregated yet interconnected areas of focus.

- Cards: Represent each quality incident or action item as a card to monitor progress and accountability.

- Card activity stream: Keep a real-time record of all actions taken on a card, enhancing transparency and aiding in investigations.
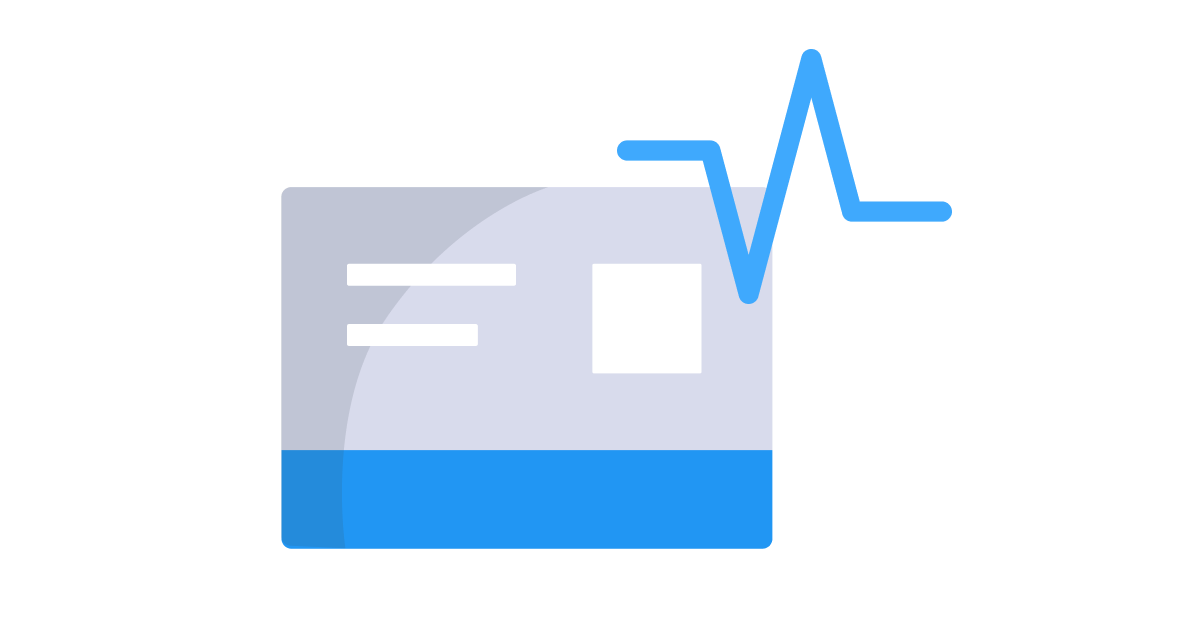
- Calendar view: Use this view to track and manage deadlines for quality checks, audits, and compliance-related activities.
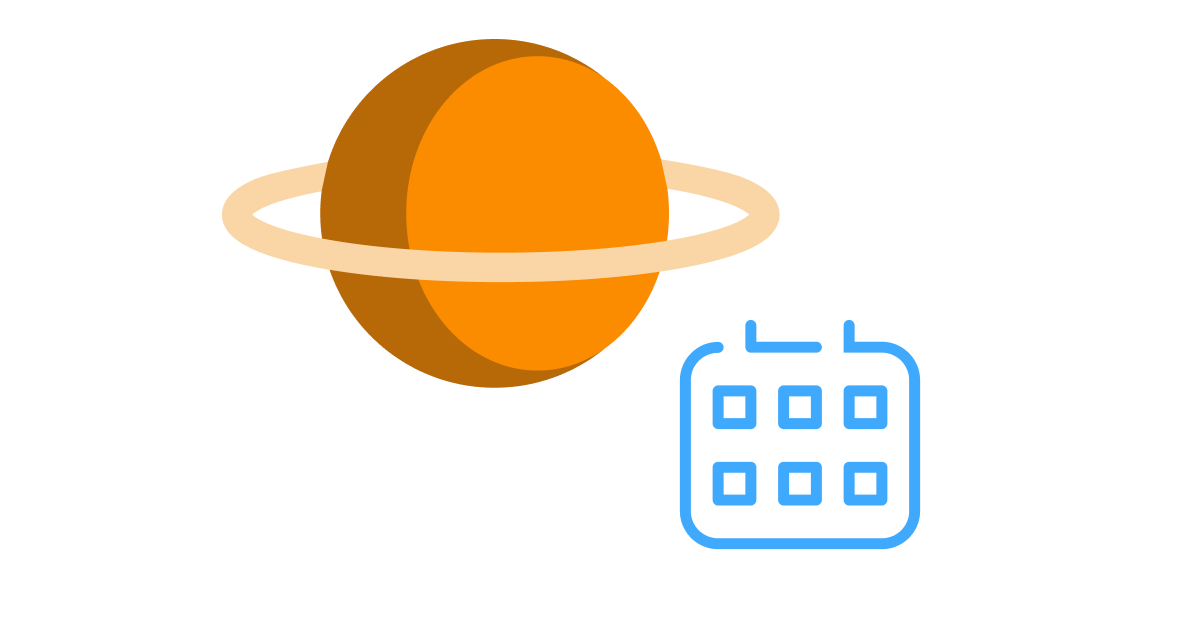
- Card relation: Connect related cards to clarify dependencies, especially between corrective actions and quality incidents.

- Grouping: Organize cards related to quality issues under groupings such as incident type, product line, or urgency.
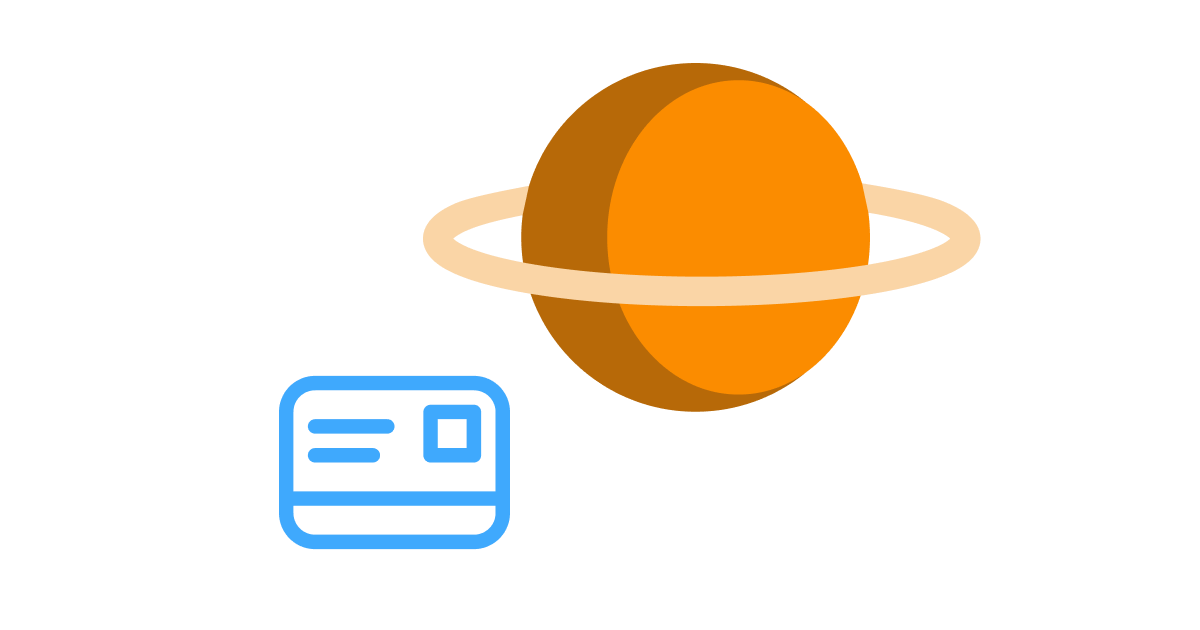
- Notification: Receive alerts on updates and changes to stay informed about the quality-related activities within your space.
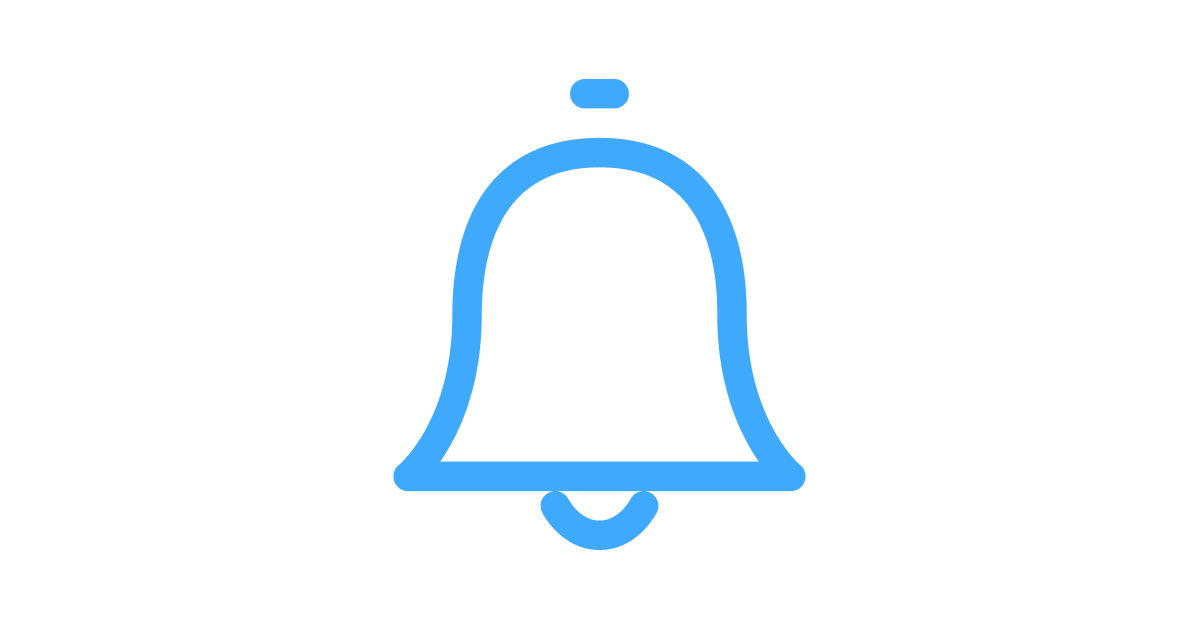
- KanBo Search: Find any critical quality document or discussion quickly with advanced search capabilities.
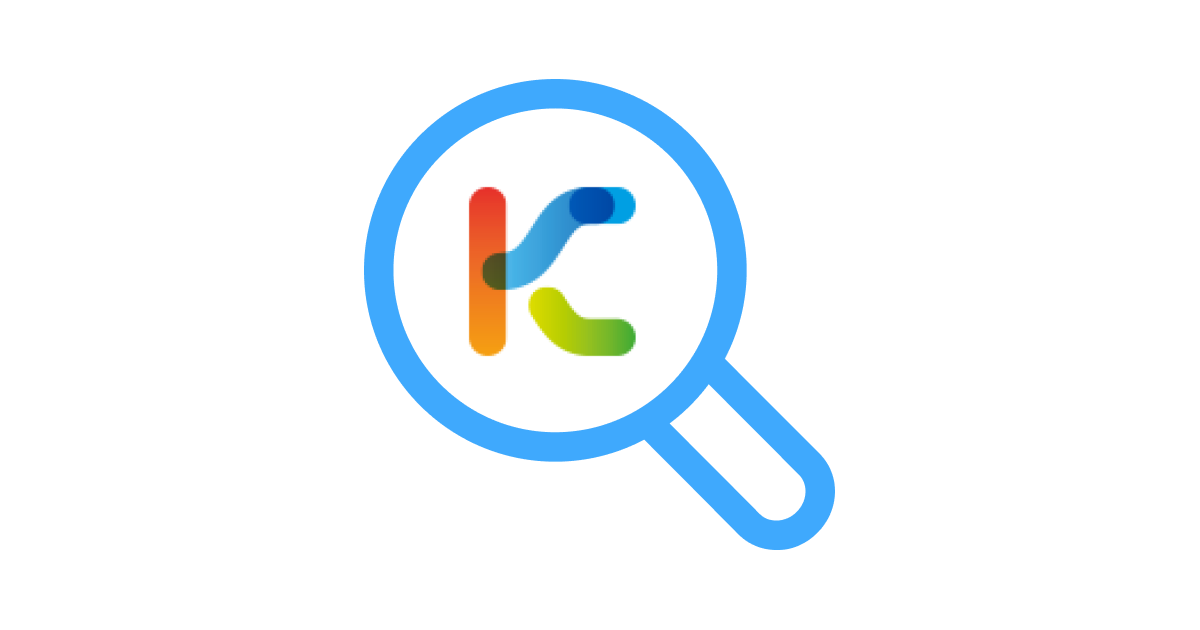
What can you expect after solving this challenge?
Implementing KanBo for collaboration challenges in pharmaceutical Quality Specialist Operations leads to long-term benefits, such as enhanced product quality, compliance with regulatory standards, and improved teamwork efficiency. By leveraging KanBo, operations can achieve streamlined communication, a centralized platform for all quality incidents, and proactive management of quality deviations. Future enhancements may include more advanced analytics for predicting quality trends, integration with additional quality management tools, and more sophisticated automation of quality processes. With KanBo, Quality Specialist Operations can not only resolve current collaboration challenges but also establish a more proactive and efficient quality management system for the future.
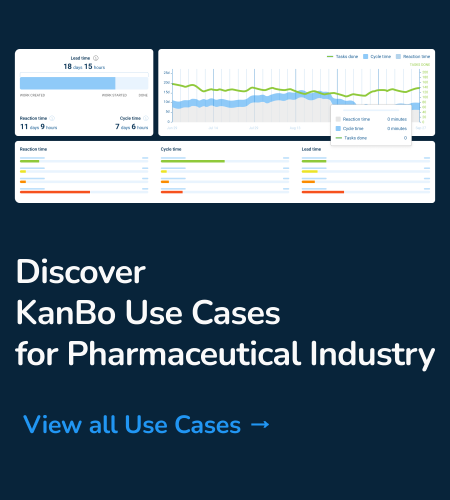