Table of Contents
KanBo – The Pharma-Focused Work Coordination Maestro
Experience ultimate task alignment, communication and collaboration
Trusted globally, KanBo, bridges the gap between management and engineering in complex pharmaceutical organizations. Seamless coordination, advanced project planning, and outstanding leadership are made possible through our versatile software. Stride toward your mission-critical goals with superior collaboration and communication.
KanBo Quality Assurance Inspector - Pharmaceutical Industry and Collaboration Challenges
What do readers need to know about this challenge?
In the pharmaceutical industry, maintaining consistent quality assurance standards is imperative for both product integrity and regulatory compliance. A challenge that Quality Assurance Inspectors frequently encounter is the complex task of effectively coordinating investigations into abnormal events, deviations, and trends. This requires meticulous root cause analysis and implementation of corrective and preventive actions across various teams, often dispersed across different geographic locations.
What reader can do with KanBo to solve this challenge?
- Space: Create organized spaces for each quality assurance project, ensuring a single point of truth for all activities and documentation involved in investigations.

- Card activity stream: Utilize the card activity stream to maintain a clear and updated log of every action taken during an investigation, enhancing accountability.
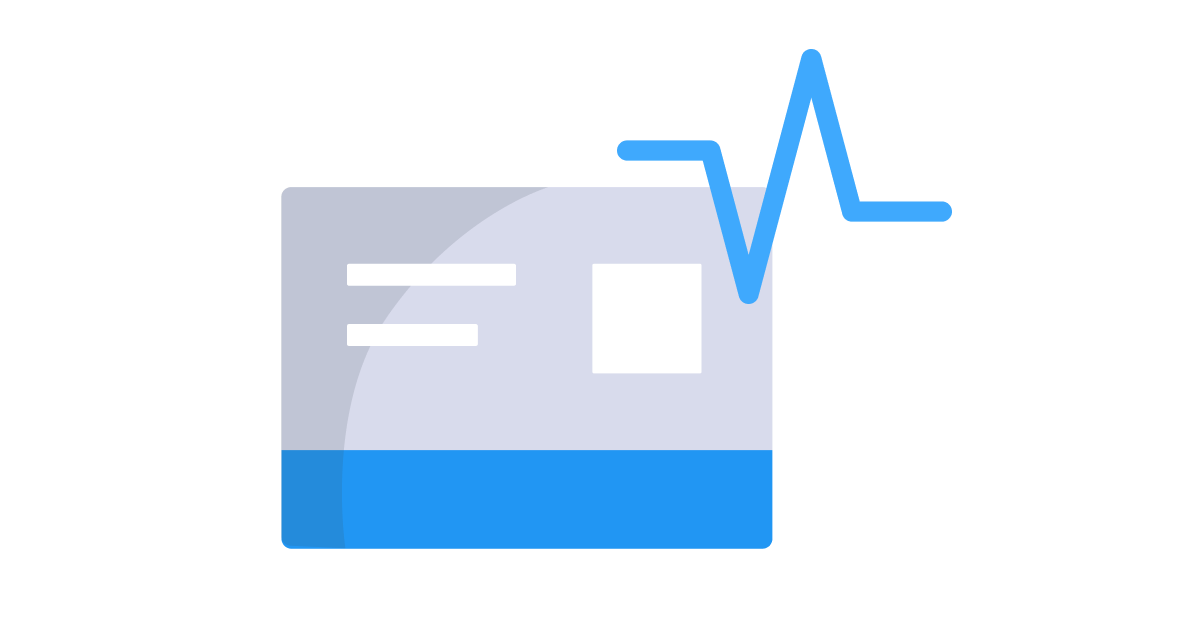
- Calendar view: Manage and oversee critical timelines for investigations and related quality improvement measures through the Calendar view.
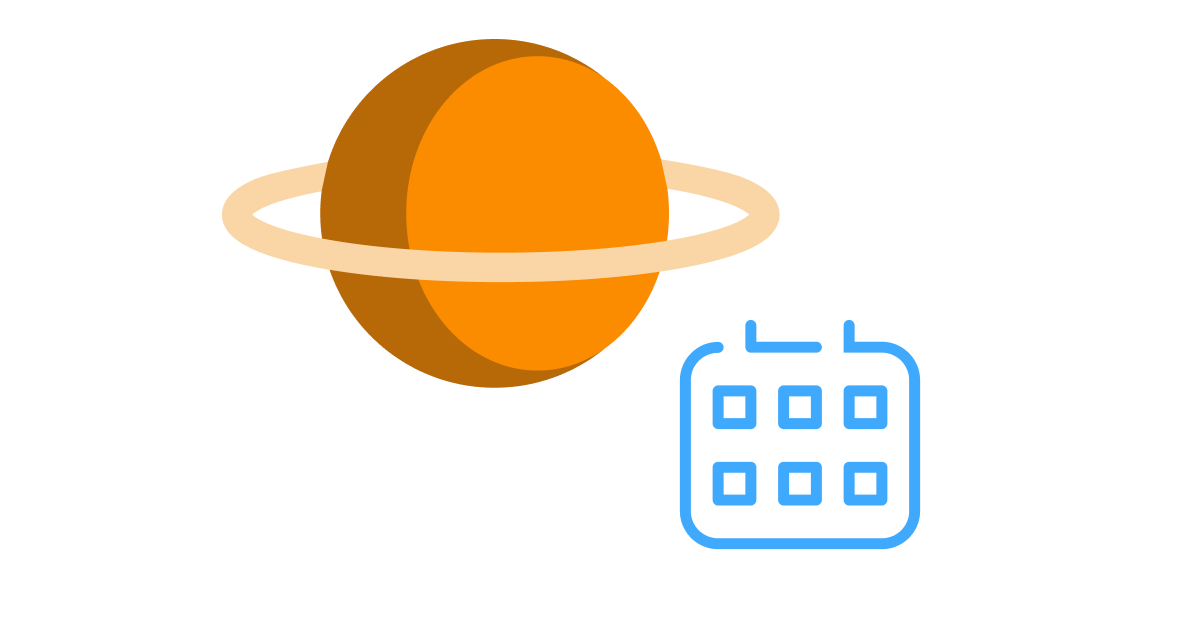
- Card relation: Build clear dependencies between investigation tasks to establish order and flow of the quality assurance process.

- Filtering cards: Swiftly find and address specific events or deviations by using filtering options to zero in on pertinent cards within a space.
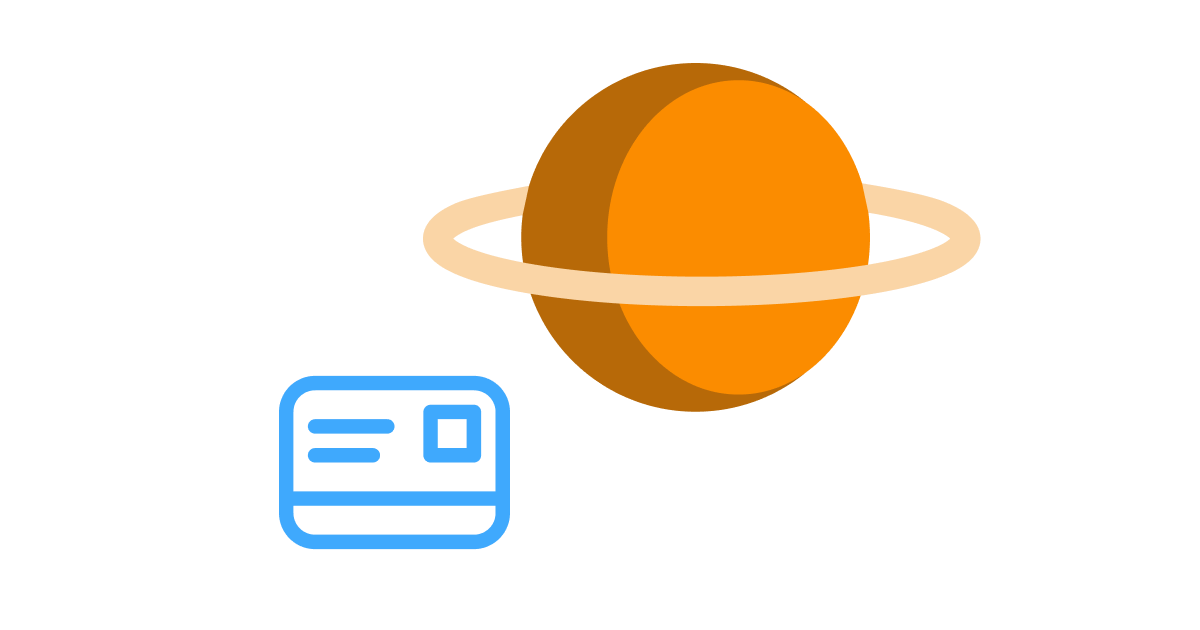
- Timeline view: Arrange and visualize the chronological sequence of quality assurance tasks for easier management and scheduling using the Timeline view.
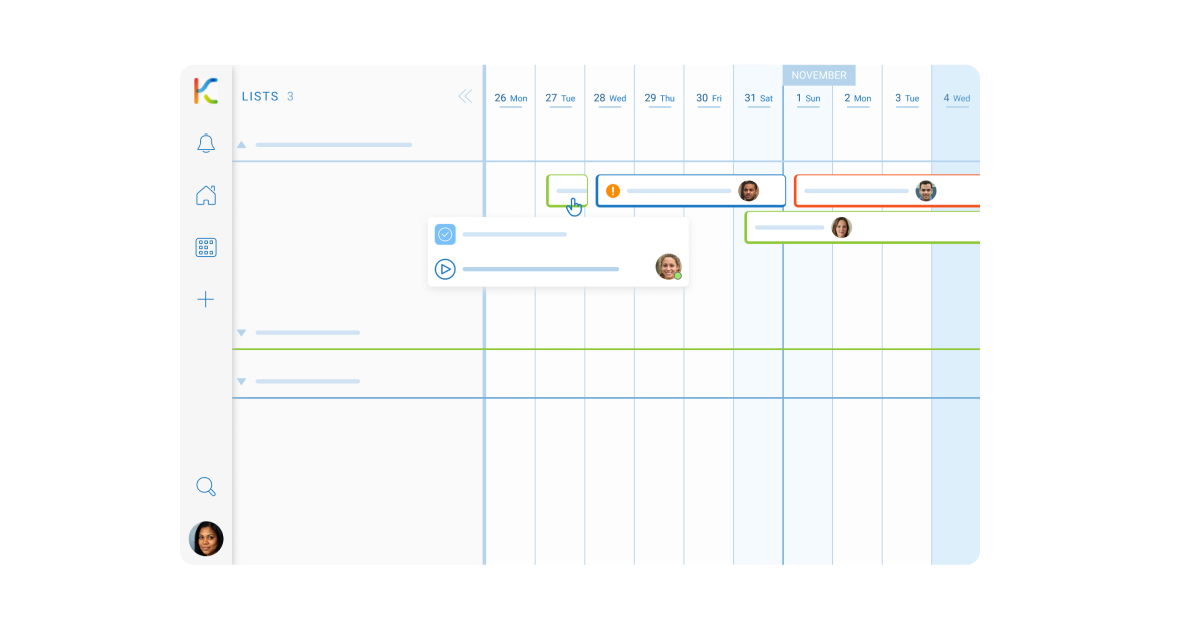
- KanBo Search: Quickly locate critical information within your KanBo spaces, saving time and improving the efficiency of the investigation process.
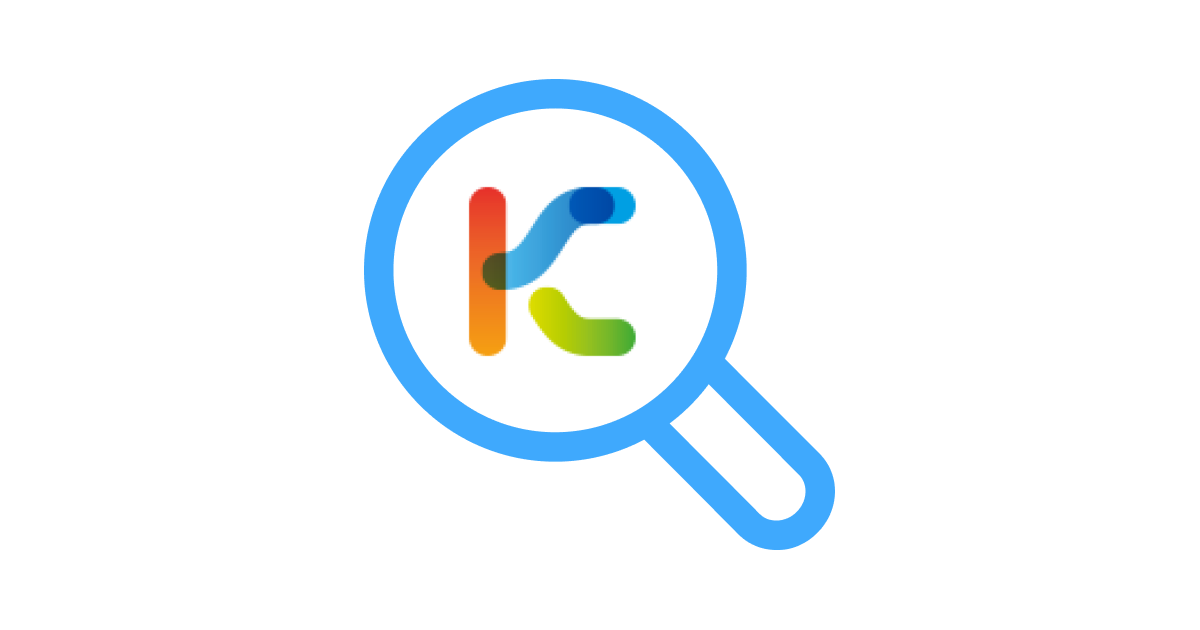
- Gantt Chart view: Plan out long-term corrective and preventive actions with the Gantt Chart view, which provides a comprehensive perspective on deadlines and progress.
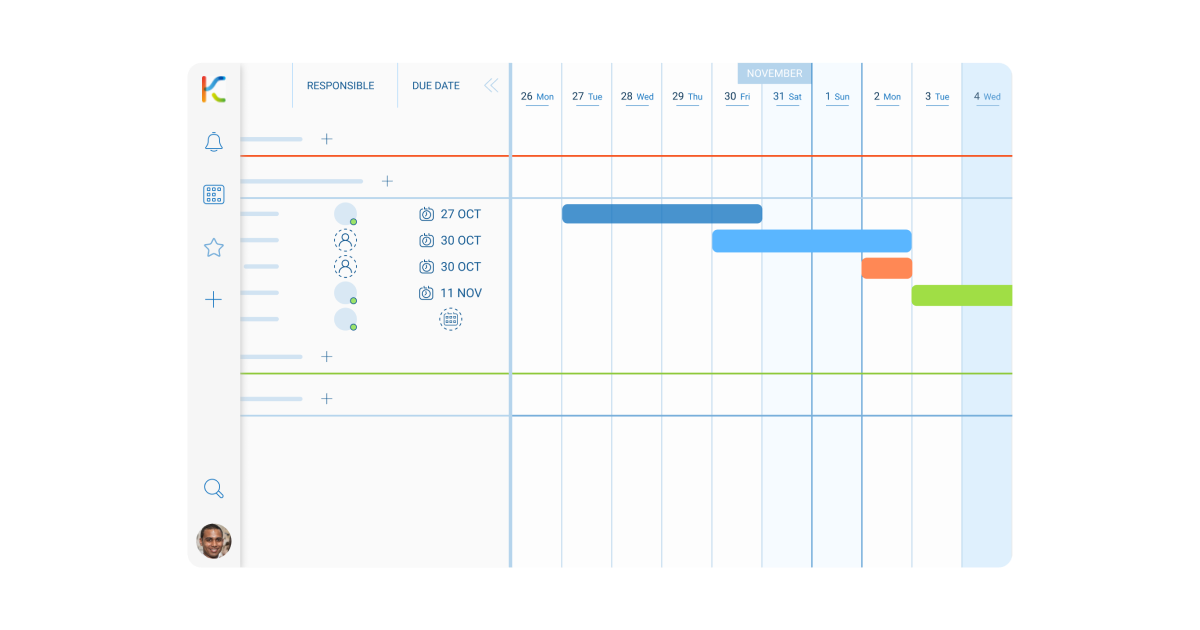
What reader can expect after solving this challenge?
After effectively applying KanBo's features to address the collaboration challenges in quality assurance, organizations can anticipate a robust set of long-term benefits. Improved investigation coordination across teams will enable rapid identification and resolution of quality issues. Transparent and real-time tracking of corrective actions will bolster regulatory compliance and product quality. Centralized documentation management will reduce errors and prevent information silos, resulting in a more streamlined quality assurance process.
Future improvements could include further customization of workflow tracking for quality improvement measures, integration of predictive quality trend analytics, and a more seamless collaboration experience that adapts to the evolving landscape of quality assurance in the pharmaceutical industry. With KanBo, companies can look forward to not only solving current challenges but also enhancing their quality management systems for the future.
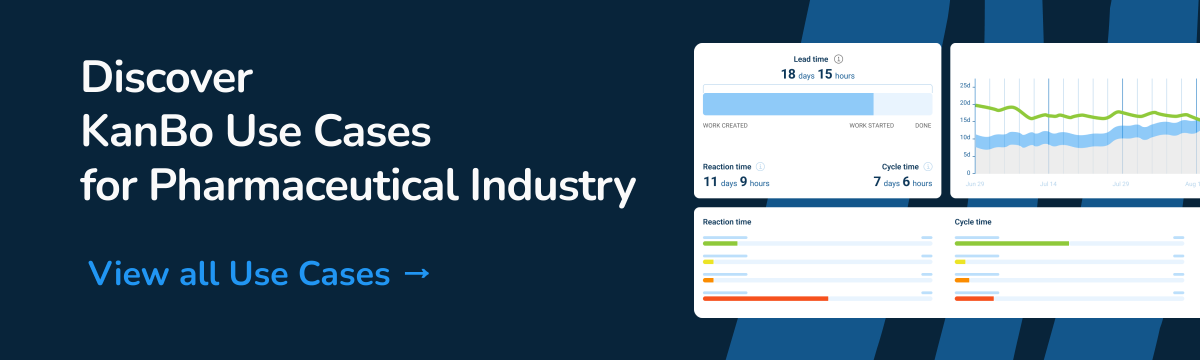
Table of Contents
KanBo – The Pharma-Focused Work Coordination Maestro
Experience ultimate task alignment, communication and collaboration
Trusted globally, KanBo, bridges the gap between management and engineering in complex pharmaceutical organizations. Seamless coordination, advanced project planning, and outstanding leadership are made possible through our versatile software. Stride toward your mission-critical goals with superior collaboration and communication.
KanBo Quality Assurance Inspector - Pharmaceutical Industry and Collaboration Challenges
What do readers need to know about this challenge?
In the pharmaceutical industry, maintaining consistent quality assurance standards is imperative for both product integrity and regulatory compliance. A challenge that Quality Assurance Inspectors frequently encounter is the complex task of effectively coordinating investigations into abnormal events, deviations, and trends. This requires meticulous root cause analysis and implementation of corrective and preventive actions across various teams, often dispersed across different geographic locations.
What reader can do with KanBo to solve this challenge?
- Space: Create organized spaces for each quality assurance project, ensuring a single point of truth for all activities and documentation involved in investigations.

- Card activity stream: Utilize the card activity stream to maintain a clear and updated log of every action taken during an investigation, enhancing accountability.
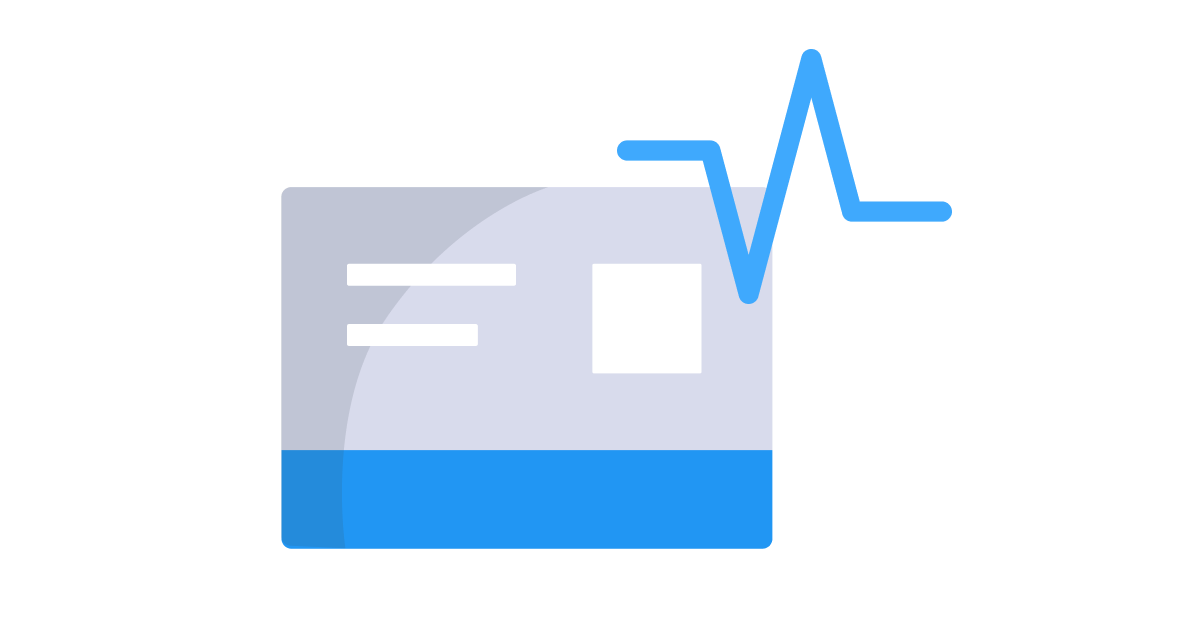
- Calendar view: Manage and oversee critical timelines for investigations and related quality improvement measures through the Calendar view.
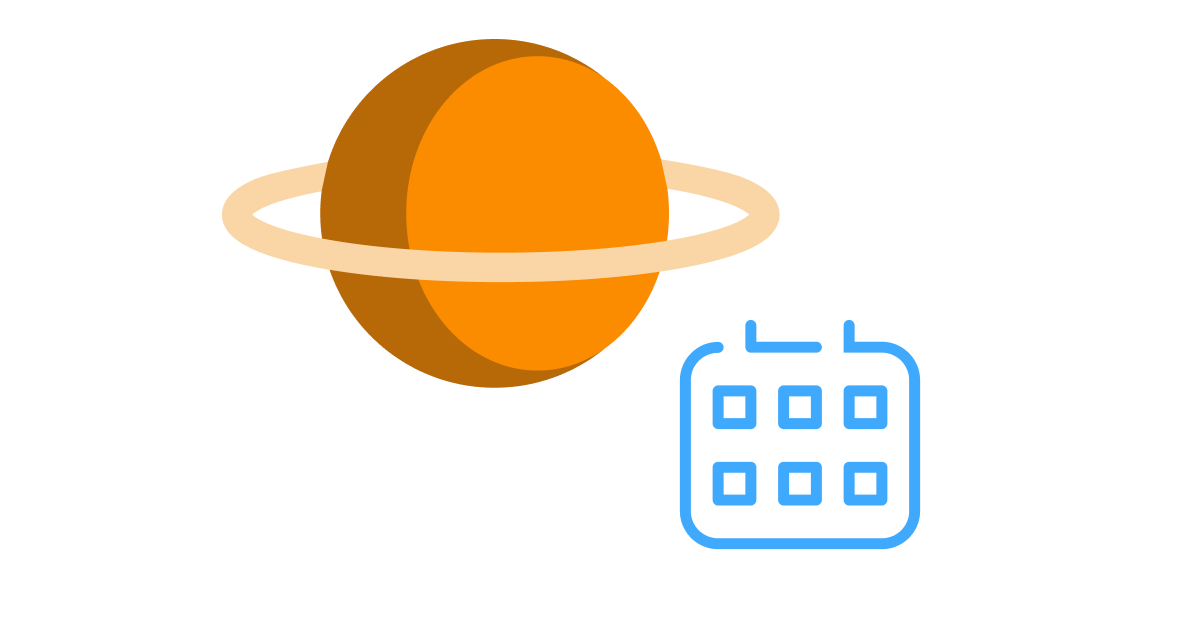
- Card relation: Build clear dependencies between investigation tasks to establish order and flow of the quality assurance process.

- Filtering cards: Swiftly find and address specific events or deviations by using filtering options to zero in on pertinent cards within a space.
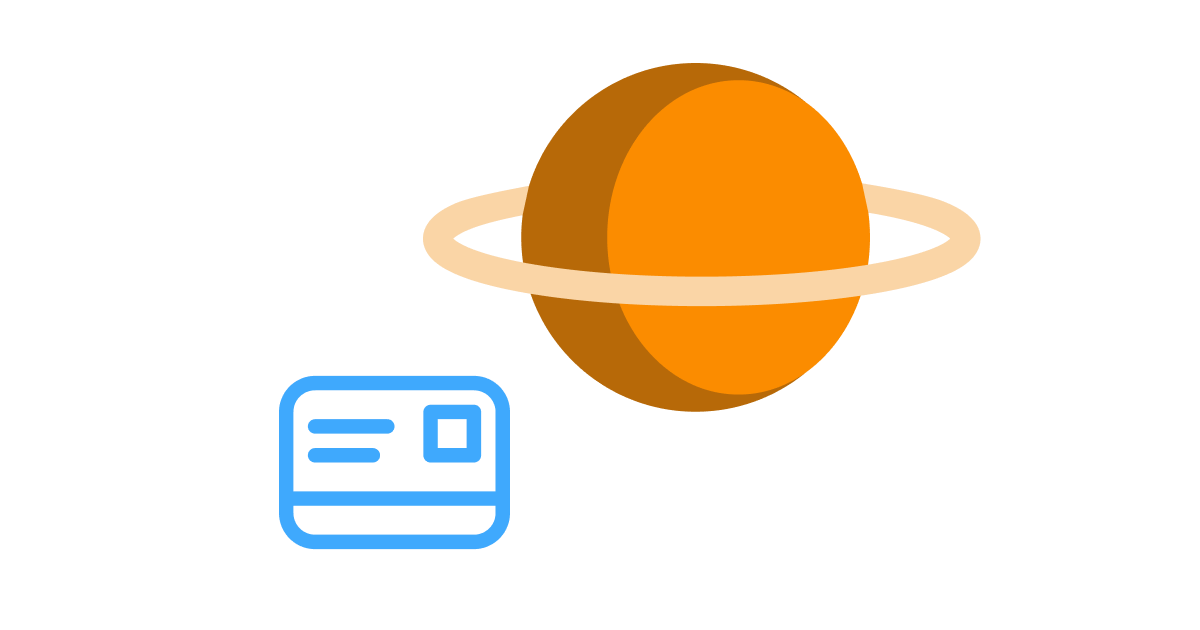
- Timeline view: Arrange and visualize the chronological sequence of quality assurance tasks for easier management and scheduling using the Timeline view.
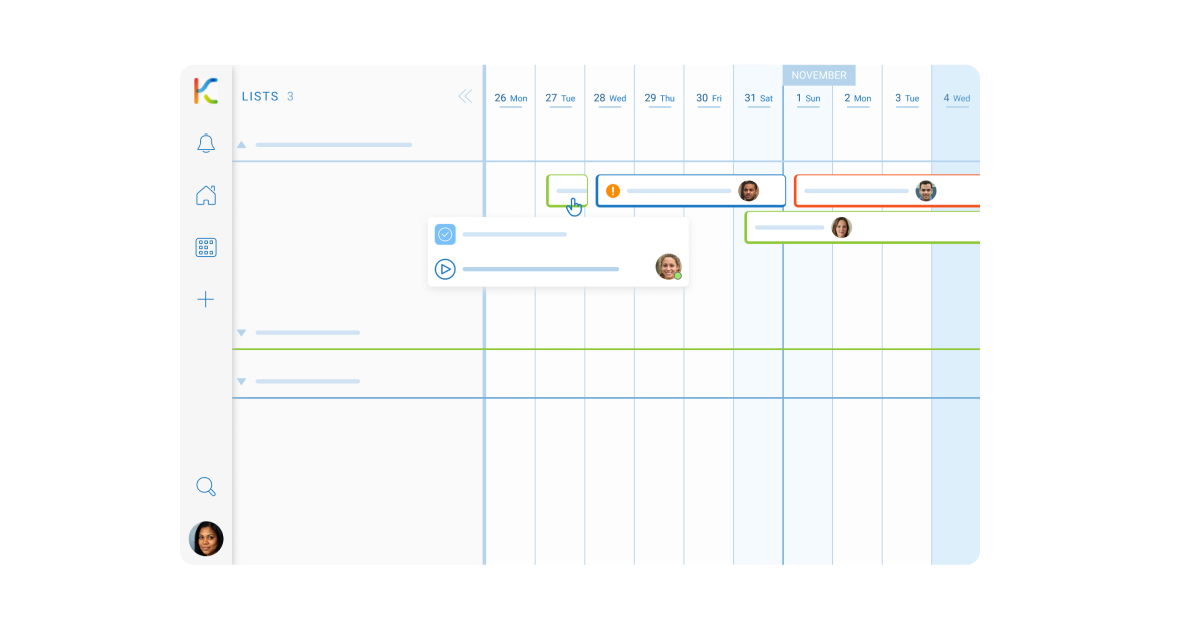
- KanBo Search: Quickly locate critical information within your KanBo spaces, saving time and improving the efficiency of the investigation process.
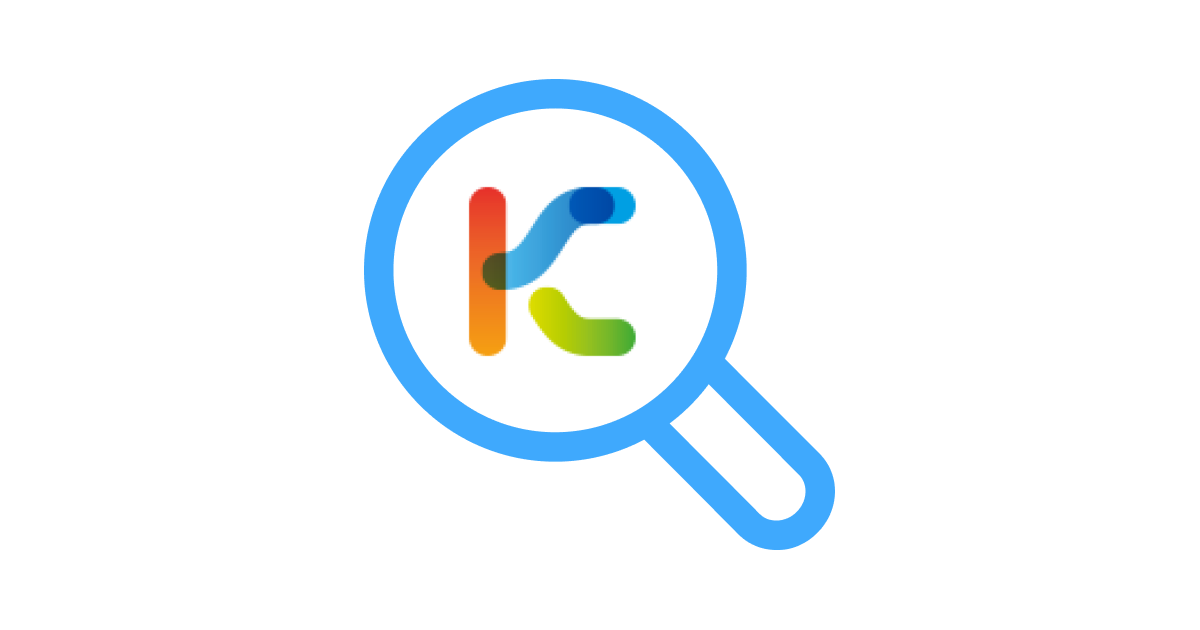
- Gantt Chart view: Plan out long-term corrective and preventive actions with the Gantt Chart view, which provides a comprehensive perspective on deadlines and progress.
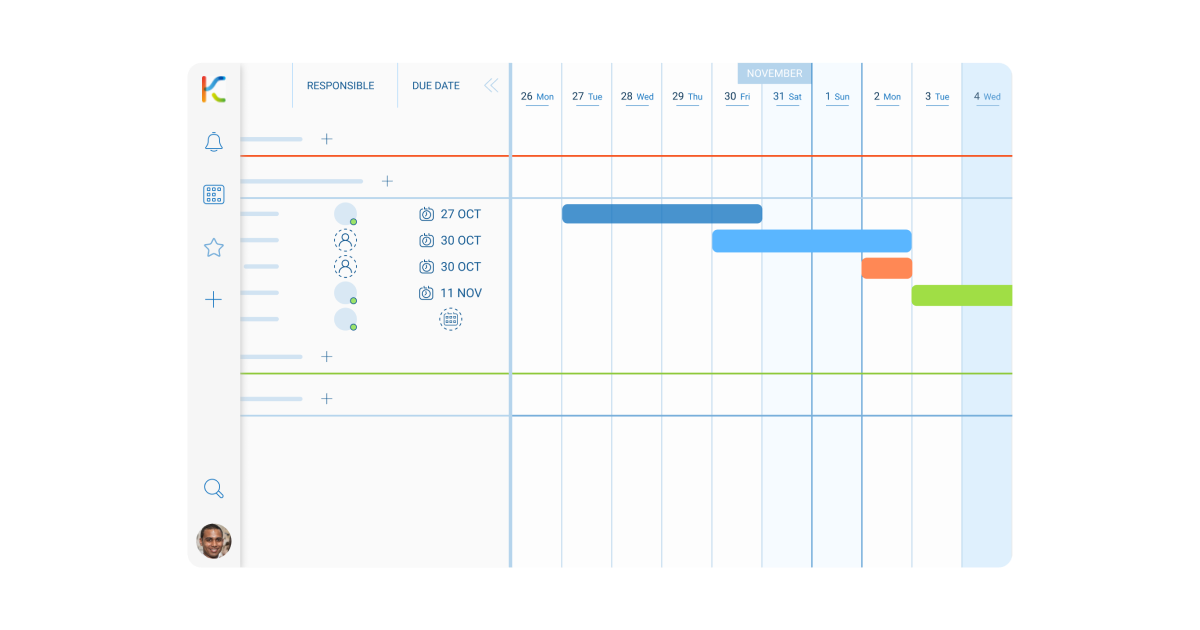
What reader can expect after solving this challenge?
After effectively applying KanBo's features to address the collaboration challenges in quality assurance, organizations can anticipate a robust set of long-term benefits. Improved investigation coordination across teams will enable rapid identification and resolution of quality issues. Transparent and real-time tracking of corrective actions will bolster regulatory compliance and product quality. Centralized documentation management will reduce errors and prevent information silos, resulting in a more streamlined quality assurance process.
Future improvements could include further customization of workflow tracking for quality improvement measures, integration of predictive quality trend analytics, and a more seamless collaboration experience that adapts to the evolving landscape of quality assurance in the pharmaceutical industry. With KanBo, companies can look forward to not only solving current challenges but also enhancing their quality management systems for the future.
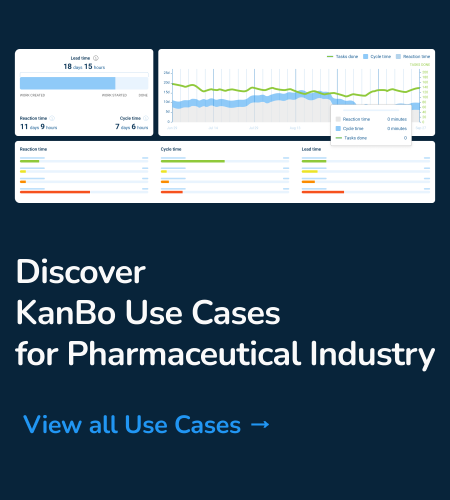