Table of Contents
KanBo – The Pharma-Focused Work Coordination Maestro
Experience ultimate task alignment, communication and collaboration
Trusted globally, KanBo, bridges the gap between management and engineering in complex pharmaceutical organizations. Seamless coordination, advanced project planning, and outstanding leadership are made possible through our versatile software. Stride toward your mission-critical goals with superior collaboration and communication.
KanBo Packaging Project Manager Pharmaceutical Inclusion and Collaboration Challenge
What do readers need to know about this challenge?
In the realm of pharmaceuticals, a Packaging Project Manager tackles the sensitive and crucial challenge of inclusivity. This involves integrating individuals with disabilities into the workforce, necessitating careful planning, coordination, and support to ensure that all team members can contribute effectively within the workplace.
What can readers do with KanBo to solve this challenge?
- Space Organization: Create a dedicated space in KanBo to centralize all tasks and activities related to the Packaging Inclusion project. Set up spaces that are accessible and designed with inclusivity in mind.

- Customized Workflow: Utilize the Kanban view to establish clear stages of the inclusion process for easy manageability and to provide visual indicators of progress.
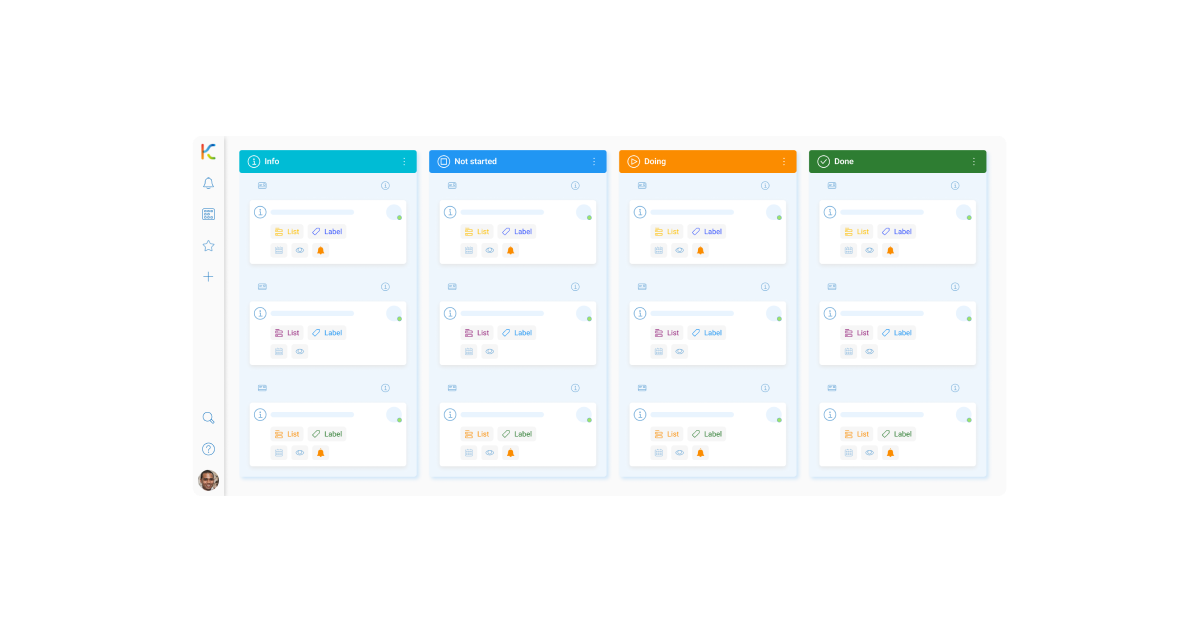
- Employee Onboarding: Use cards to represent each individual's onboarding process, with all necessary information, checklists, and timelines to ensure a smooth transition.

- Monitoring Progress: Implement Card statuses to reflect where each individual is in their onboarding journey, showcasing achievements and next steps.
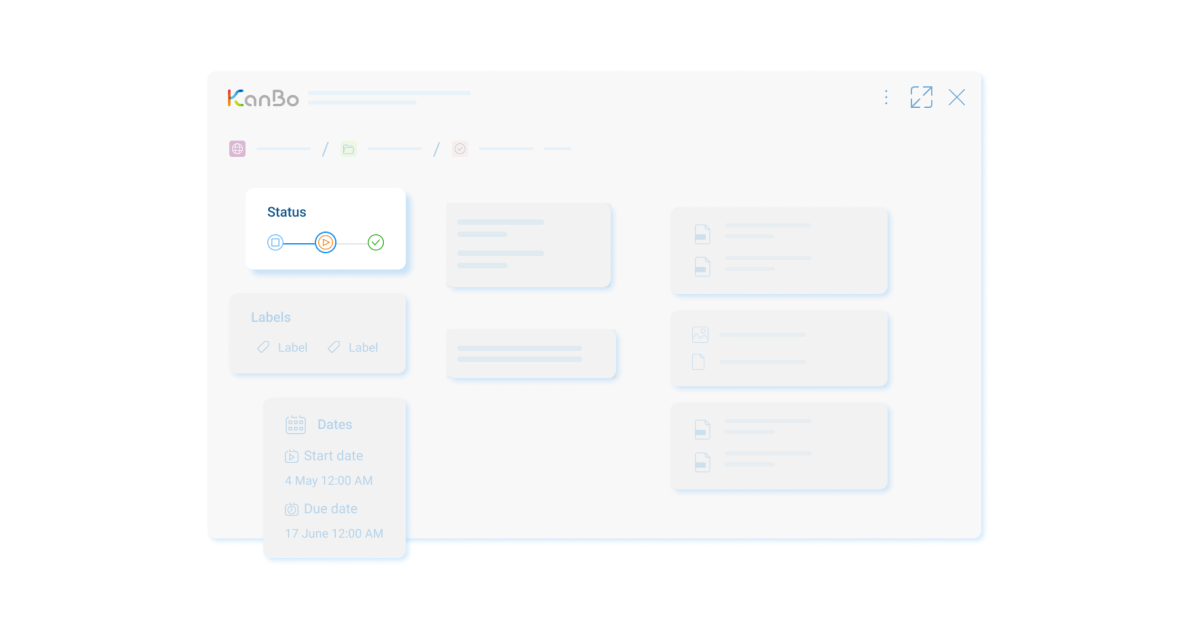
- Training and Support: Employ the Grouping feature to organize training sessions, workshops, and support groups to enhance collaboration and team cohesion.
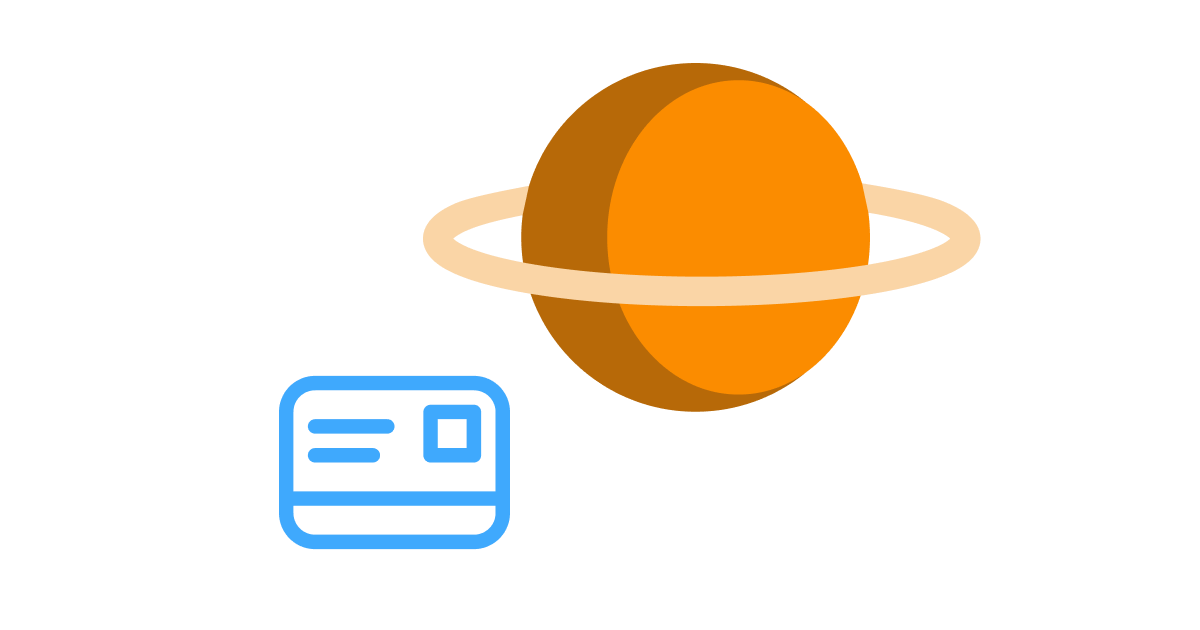
- Accessibility: Use Document sources to provide easy access to all necessary documents and training materials that support the inclusion of people with disabilities.

- Real-Time Collaboration: Leverage the User activity stream to monitor individual engagement and contributions, promoting a culture of visibility and proactive support.
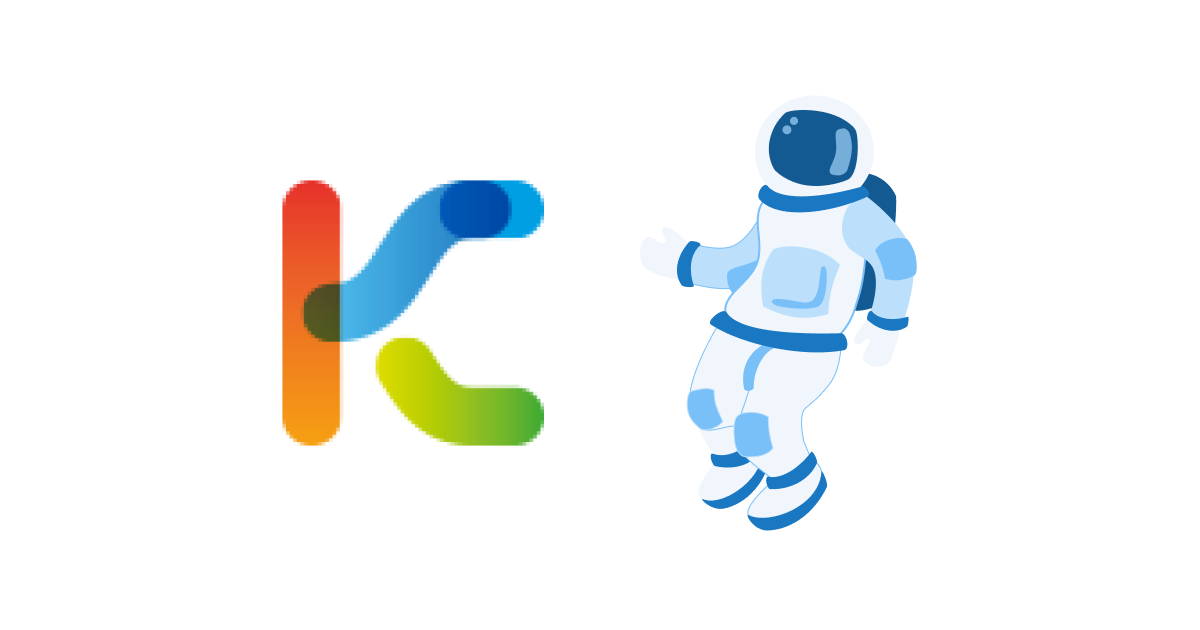
- Personalized Follow-Ups: Set Reminders for check-ins with new team members, ensuring they have the support they need and feel included in the team dynamic.
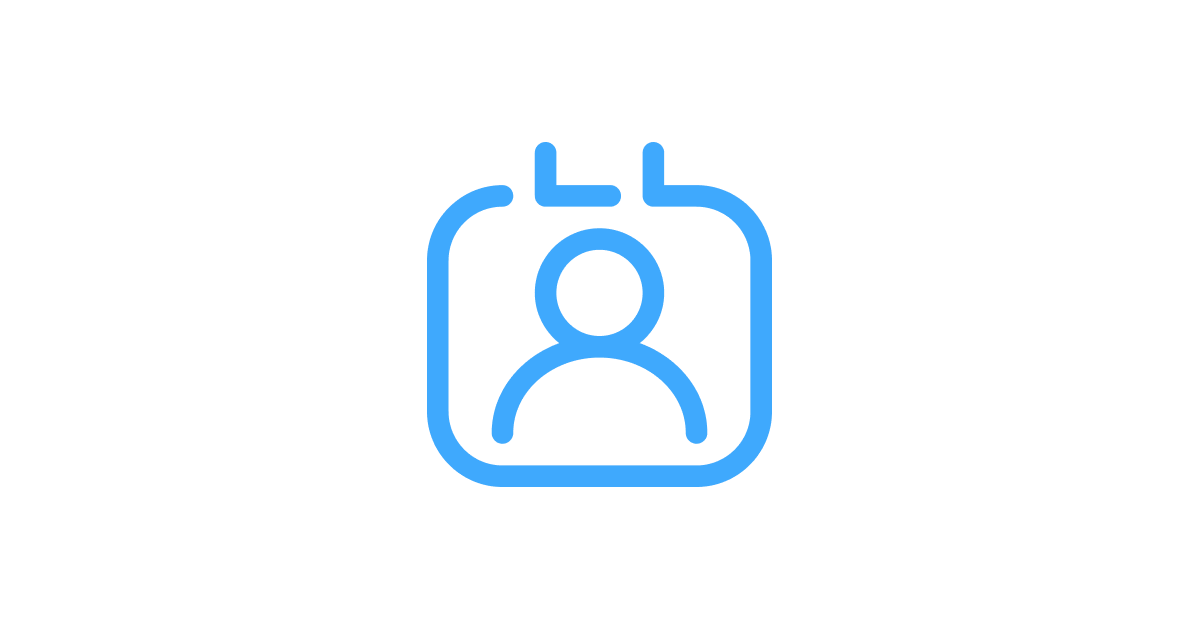
What can readers expect after solving this challenge?
After implementing KanBo to facilitate the inclusion of individuals with disabilities into the pharmaceutical packaging team, readers can expect to see a more cohesive, collaborative, and diverse work environment. Long-term benefits include higher productivity due to the efficient organization of work and the empowerment of employees through tailored support and resources. Additionally, ongoing enhancements in KanBo's interface and functionalities will support future inclusion initiatives, promoting continuous improvement and scalability for projects. Utilizing KanBo will establish a solid foundation for not just managing but excelling at inclusive operations.
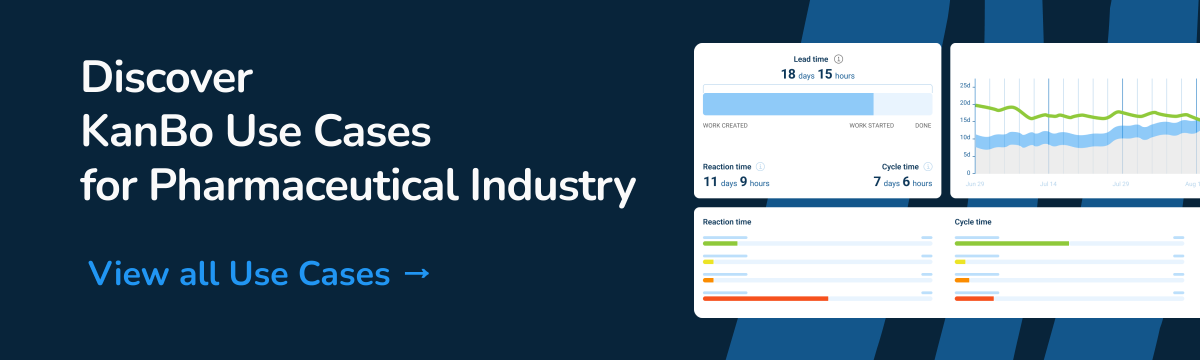
Table of Contents
KanBo – The Pharma-Focused Work Coordination Maestro
Experience ultimate task alignment, communication and collaboration
Trusted globally, KanBo, bridges the gap between management and engineering in complex pharmaceutical organizations. Seamless coordination, advanced project planning, and outstanding leadership are made possible through our versatile software. Stride toward your mission-critical goals with superior collaboration and communication.
KanBo Packaging Project Manager Pharmaceutical Inclusion and Collaboration Challenge
What do readers need to know about this challenge?
In the realm of pharmaceuticals, a Packaging Project Manager tackles the sensitive and crucial challenge of inclusivity. This involves integrating individuals with disabilities into the workforce, necessitating careful planning, coordination, and support to ensure that all team members can contribute effectively within the workplace.
What can readers do with KanBo to solve this challenge?
- Space Organization: Create a dedicated space in KanBo to centralize all tasks and activities related to the Packaging Inclusion project. Set up spaces that are accessible and designed with inclusivity in mind.

- Customized Workflow: Utilize the Kanban view to establish clear stages of the inclusion process for easy manageability and to provide visual indicators of progress.
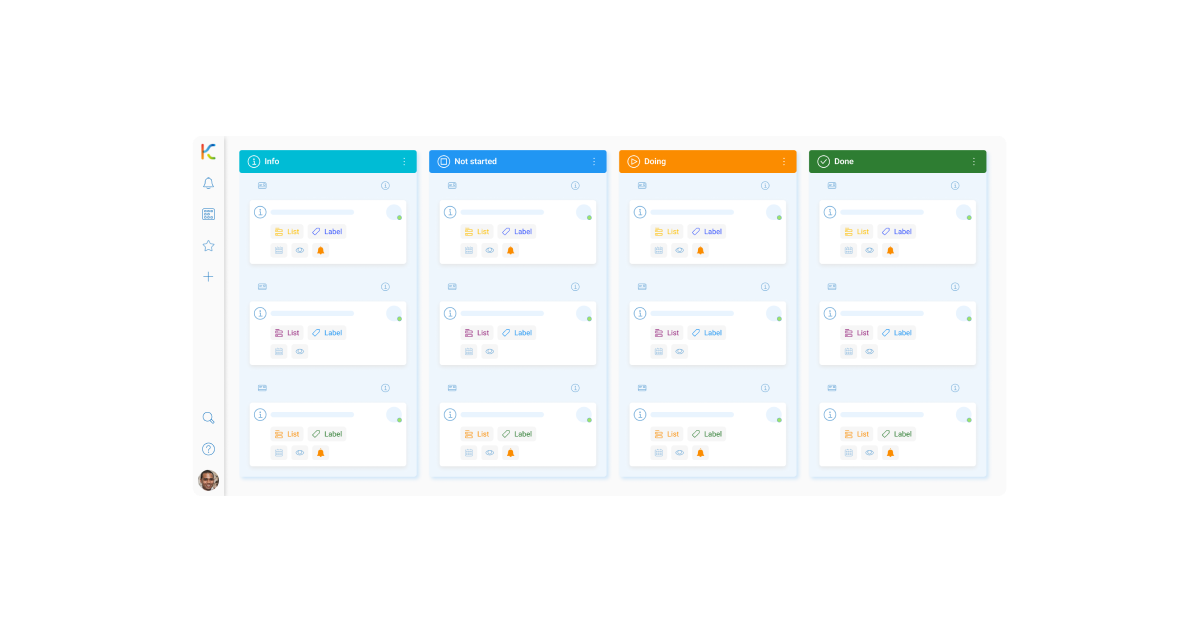
- Employee Onboarding: Use cards to represent each individual's onboarding process, with all necessary information, checklists, and timelines to ensure a smooth transition.

- Monitoring Progress: Implement Card statuses to reflect where each individual is in their onboarding journey, showcasing achievements and next steps.
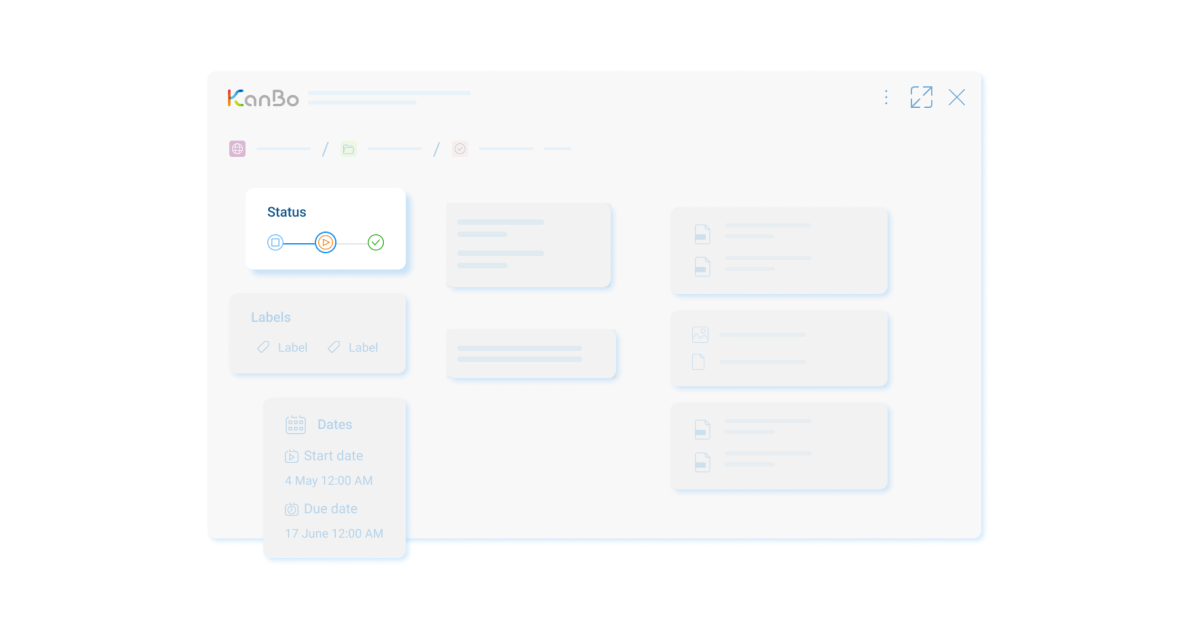
- Training and Support: Employ the Grouping feature to organize training sessions, workshops, and support groups to enhance collaboration and team cohesion.
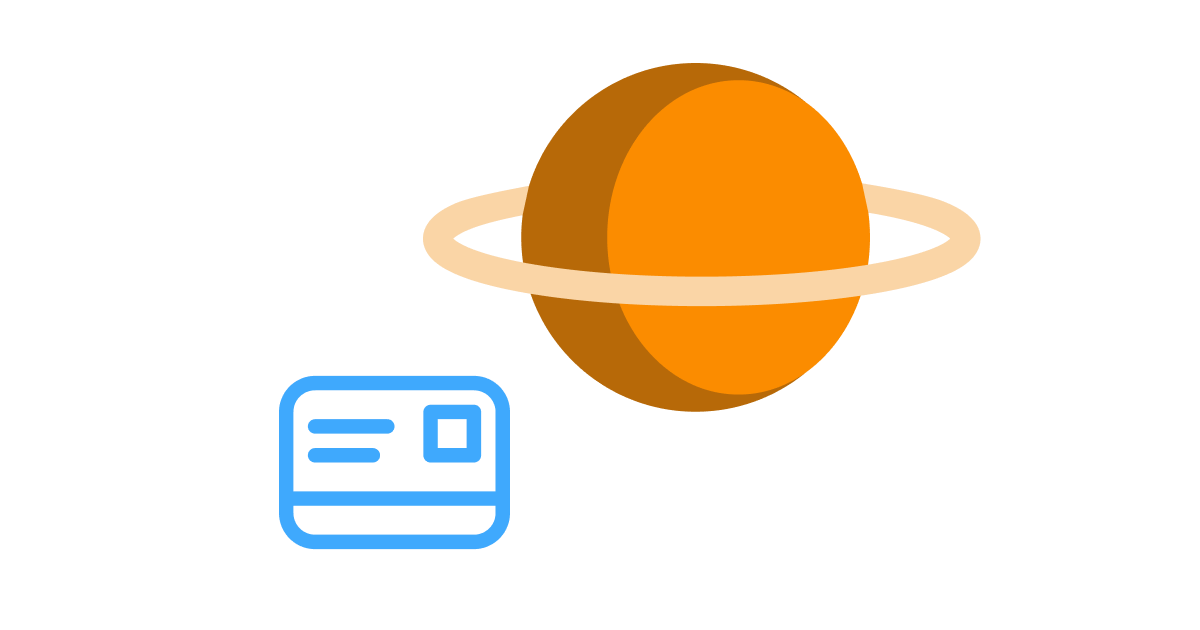
- Accessibility: Use Document sources to provide easy access to all necessary documents and training materials that support the inclusion of people with disabilities.

- Real-Time Collaboration: Leverage the User activity stream to monitor individual engagement and contributions, promoting a culture of visibility and proactive support.
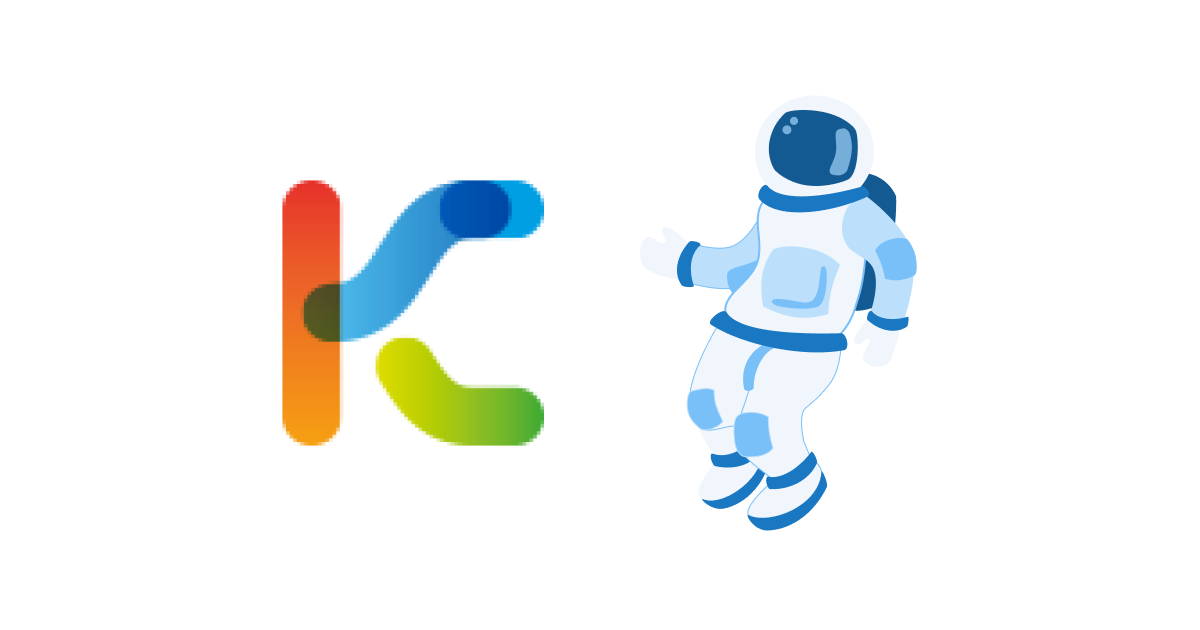
- Personalized Follow-Ups: Set Reminders for check-ins with new team members, ensuring they have the support they need and feel included in the team dynamic.
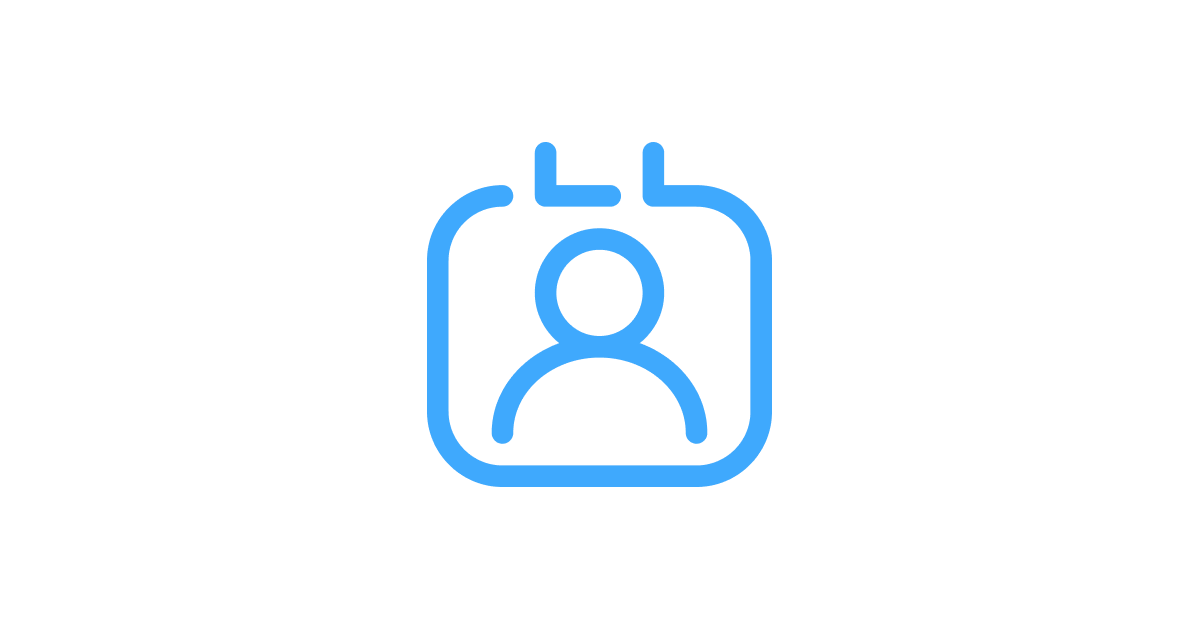
What can readers expect after solving this challenge?
After implementing KanBo to facilitate the inclusion of individuals with disabilities into the pharmaceutical packaging team, readers can expect to see a more cohesive, collaborative, and diverse work environment. Long-term benefits include higher productivity due to the efficient organization of work and the empowerment of employees through tailored support and resources. Additionally, ongoing enhancements in KanBo's interface and functionalities will support future inclusion initiatives, promoting continuous improvement and scalability for projects. Utilizing KanBo will establish a solid foundation for not just managing but excelling at inclusive operations.
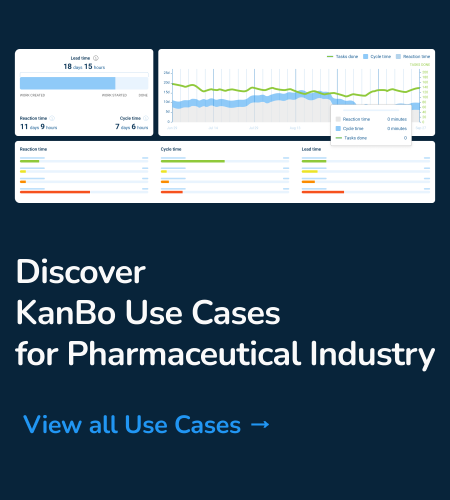