Table of Contents
KanBo – The Pharma-Focused Work Coordination Maestro
Experience ultimate task alignment, communication and collaboration
Trusted globally, KanBo, bridges the gap between management and engineering in complex pharmaceutical organizations. Seamless coordination, advanced project planning, and outstanding leadership are made possible through our versatile software. Stride toward your mission-critical goals with superior collaboration and communication.
KanBo for Sterile Manufacturing Quality Auditor in Pharmaceutical Industry: Facilitating Inter-departmental Collaboration for Quality Assurance
What do readers need to know about this challenge?
A Sterile Manufacturing Quality Auditor in the Pharmaceutical Industry plays a pivotal role in maintaining the safety, efficacy, and quality of clinical products. This role requires active collaboration with various production teams, other sites, and subcontractors, focusing on quality assurance and improvement. The primary challenge here lies in coordinating these diverse groups efficiently - ensuring seamless communication, quick decision-making, and synchronizing their efforts towards a shared quality goal.
What can the reader do with KanBo to solve this challenge?
With KanBo, these collaboration-related challenges can be efficiently addressed through an array of effective features:
- Space: Facilitate seamless communication and smoother collaboration across teams by creating customized workspaces for different teams.

- Card: Use cards to represent various quality assurance tasks, ensuring clear delegation and tracking of responsibilities and tasks.

- Card Activity Stream: Monitor all activities and developments related to a particular card/task, thereby promoting transparency and smoother progress tracking.
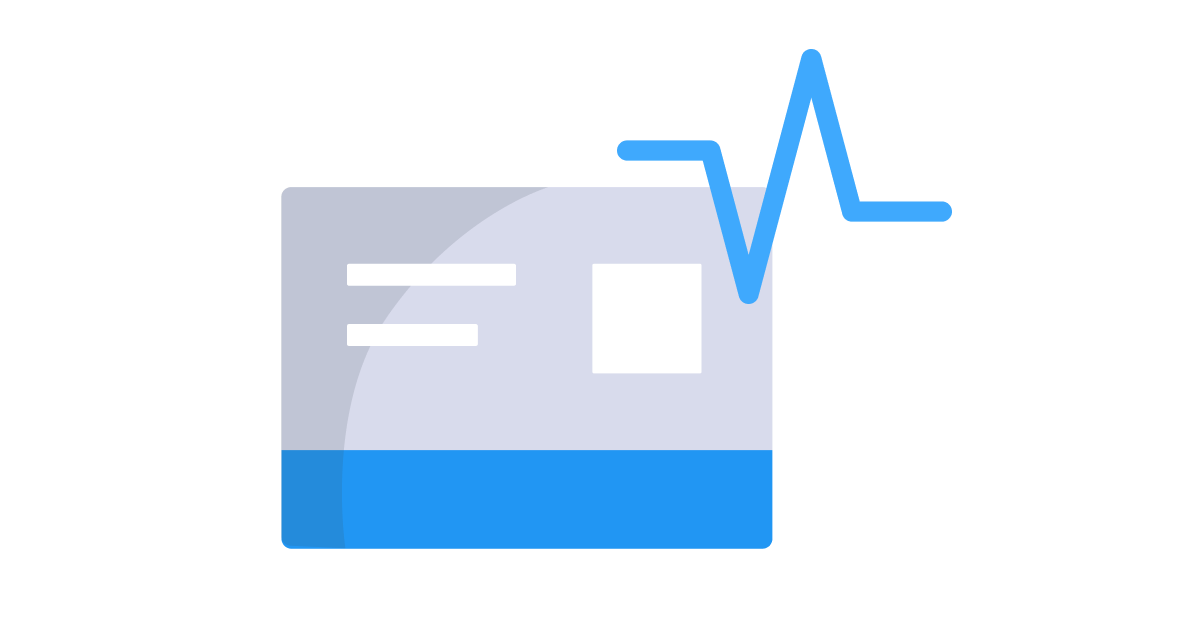
- Card Status: Track the progress of each task, giving the whole team a clear picture of the current state of work.
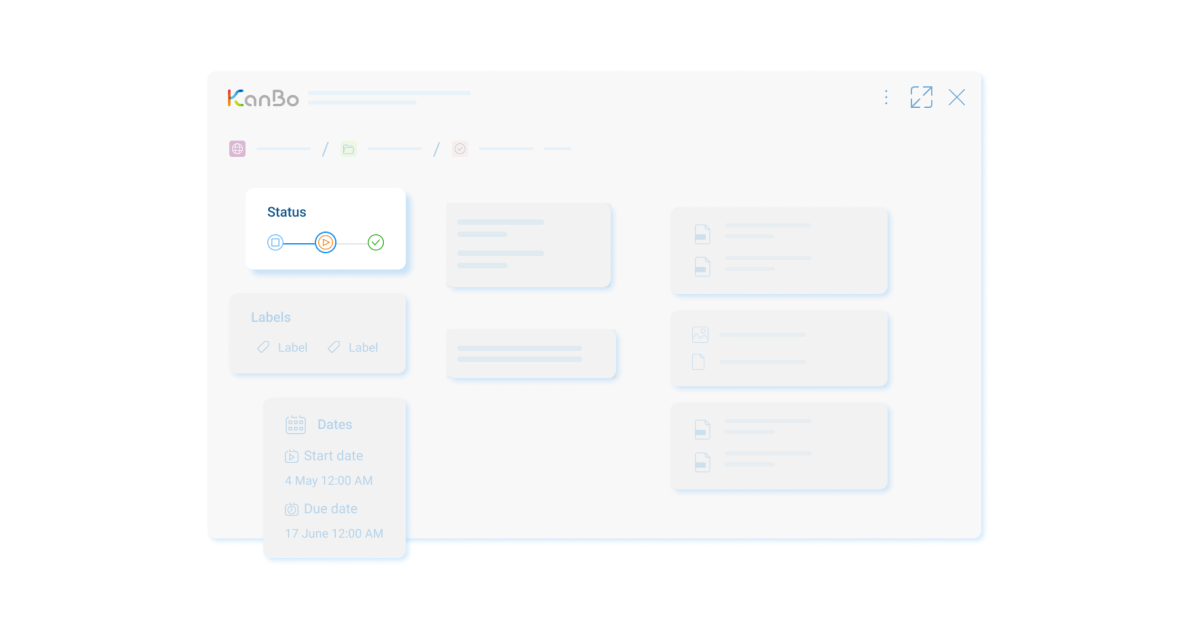
- Notification: Keep all stakeholders in the loop with updates about changes made to the cards/tasks.
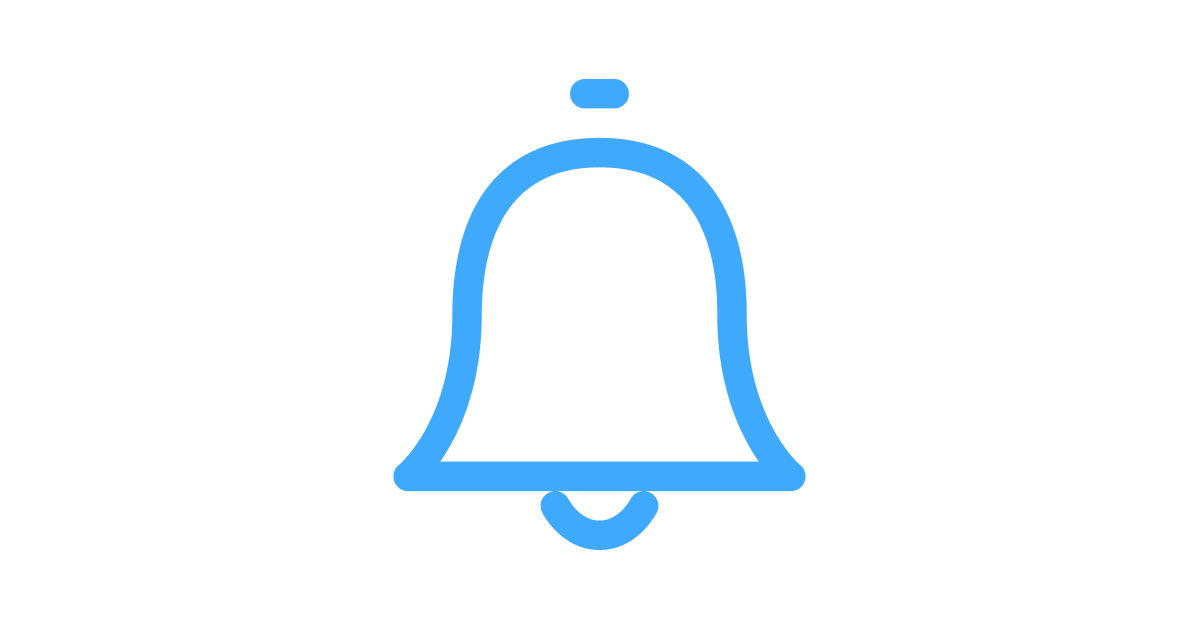
- Filtering Cards: Efficiently locate specific tasks or responsibilities, thus improving productivity and decision-making process.
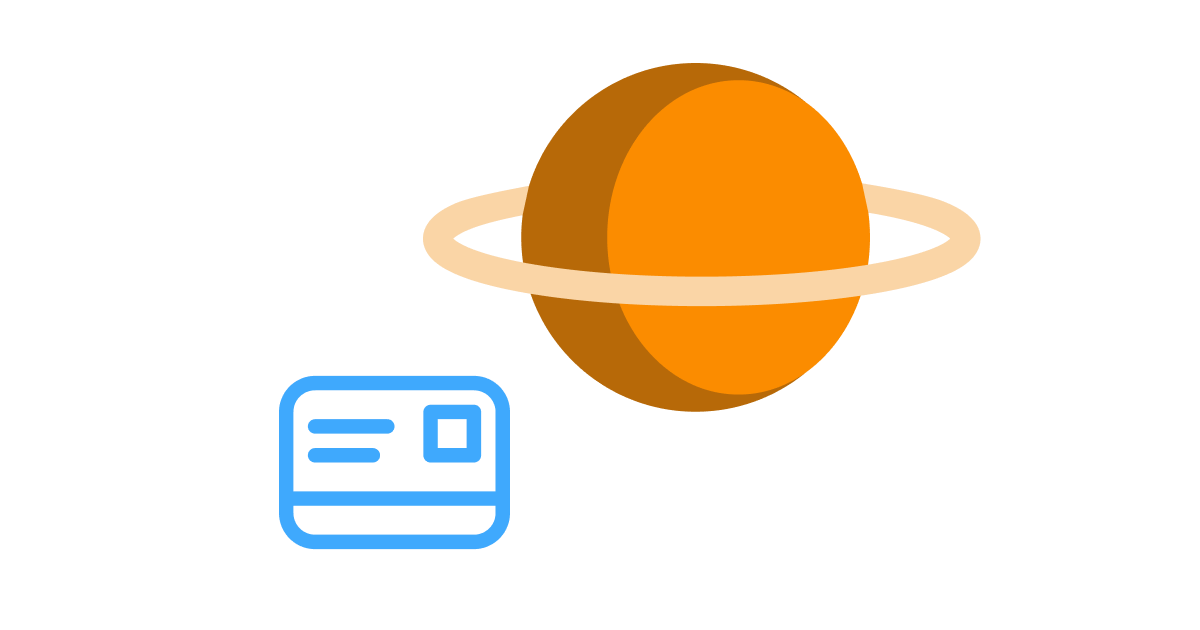
What can reader expect after solving this challenge?
Utilizing the KanBo's features will help address the challenges of managing inter-departmental collaboration effectively. The transparent and systematic tracking of tasks will not only streamline workflows but also promote accountability and responsibility among team members. Furthermore, KanBo will enhance the decision-making process, fostering efficiency, and productivity.
Over a longer period, the organization can expect improved workflow management, quick issue resolution, and overall increased productivity. The insights gained from using KanBo will also help in making informed strategic decisions, leading to better resource allocation and workflow optimization.
In conclusion, with KanBo, a Sterile Manufacturing Quality Auditor in the Pharmaceutical Industry can seamlessly collaborate with various teams and stakeholders, thereby driving quality assurance and continuous improvement.
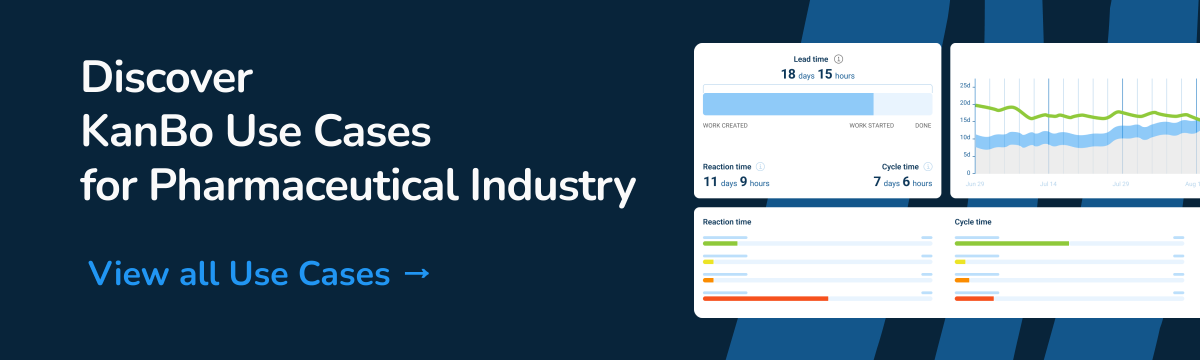
Table of Contents
KanBo – The Pharma-Focused Work Coordination Maestro
Experience ultimate task alignment, communication and collaboration
Trusted globally, KanBo, bridges the gap between management and engineering in complex pharmaceutical organizations. Seamless coordination, advanced project planning, and outstanding leadership are made possible through our versatile software. Stride toward your mission-critical goals with superior collaboration and communication.
KanBo for Sterile Manufacturing Quality Auditor in Pharmaceutical Industry: Facilitating Inter-departmental Collaboration for Quality Assurance
What do readers need to know about this challenge?
A Sterile Manufacturing Quality Auditor in the Pharmaceutical Industry plays a pivotal role in maintaining the safety, efficacy, and quality of clinical products. This role requires active collaboration with various production teams, other sites, and subcontractors, focusing on quality assurance and improvement. The primary challenge here lies in coordinating these diverse groups efficiently - ensuring seamless communication, quick decision-making, and synchronizing their efforts towards a shared quality goal.
What can the reader do with KanBo to solve this challenge?
With KanBo, these collaboration-related challenges can be efficiently addressed through an array of effective features:
- Space: Facilitate seamless communication and smoother collaboration across teams by creating customized workspaces for different teams.

- Card: Use cards to represent various quality assurance tasks, ensuring clear delegation and tracking of responsibilities and tasks.

- Card Activity Stream: Monitor all activities and developments related to a particular card/task, thereby promoting transparency and smoother progress tracking.
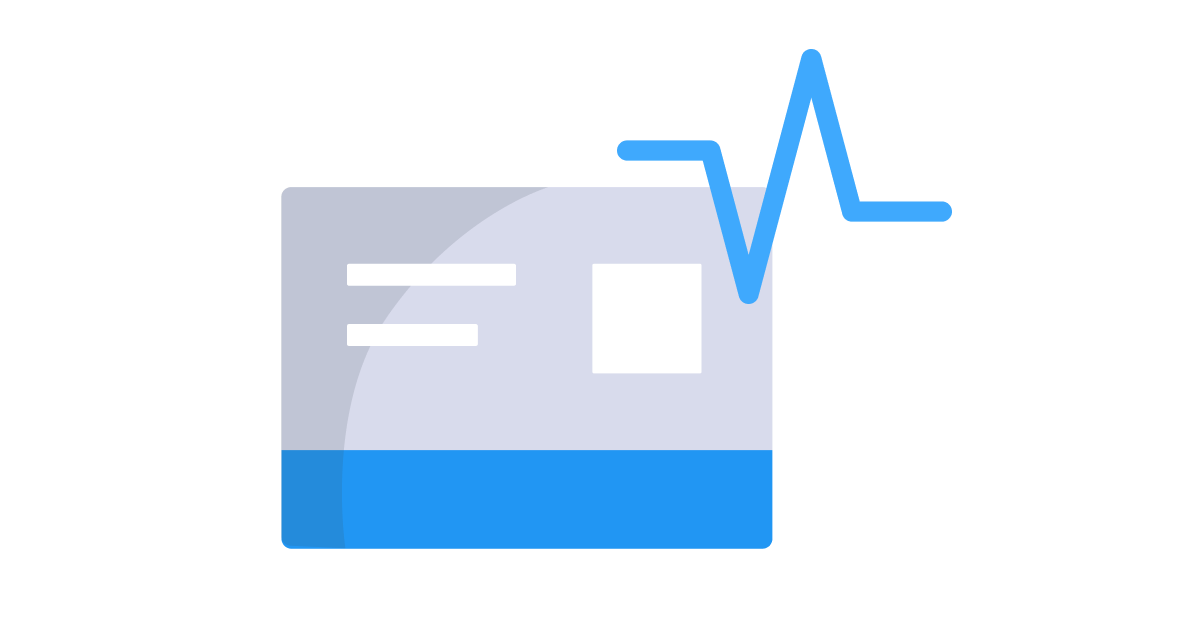
- Card Status: Track the progress of each task, giving the whole team a clear picture of the current state of work.
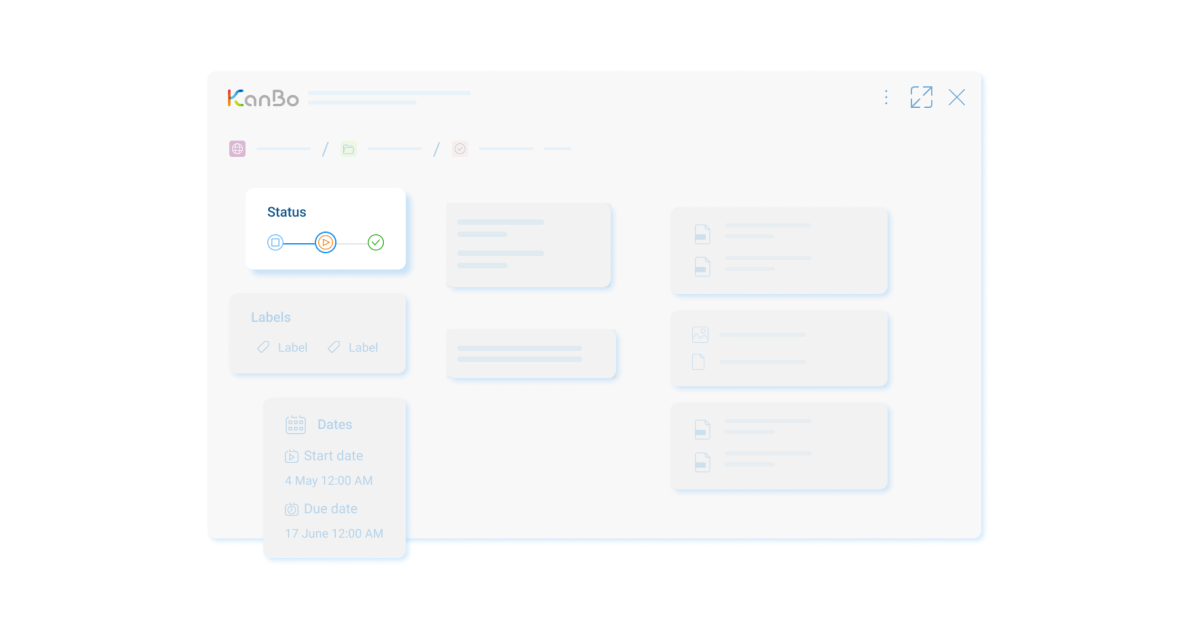
- Notification: Keep all stakeholders in the loop with updates about changes made to the cards/tasks.
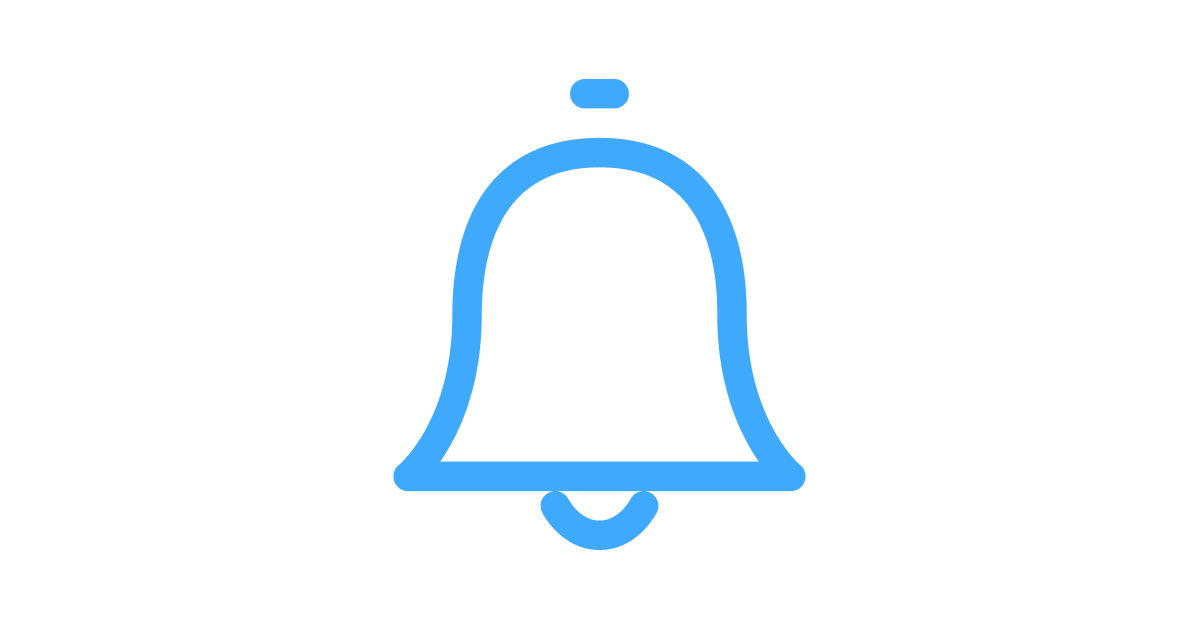
- Filtering Cards: Efficiently locate specific tasks or responsibilities, thus improving productivity and decision-making process.
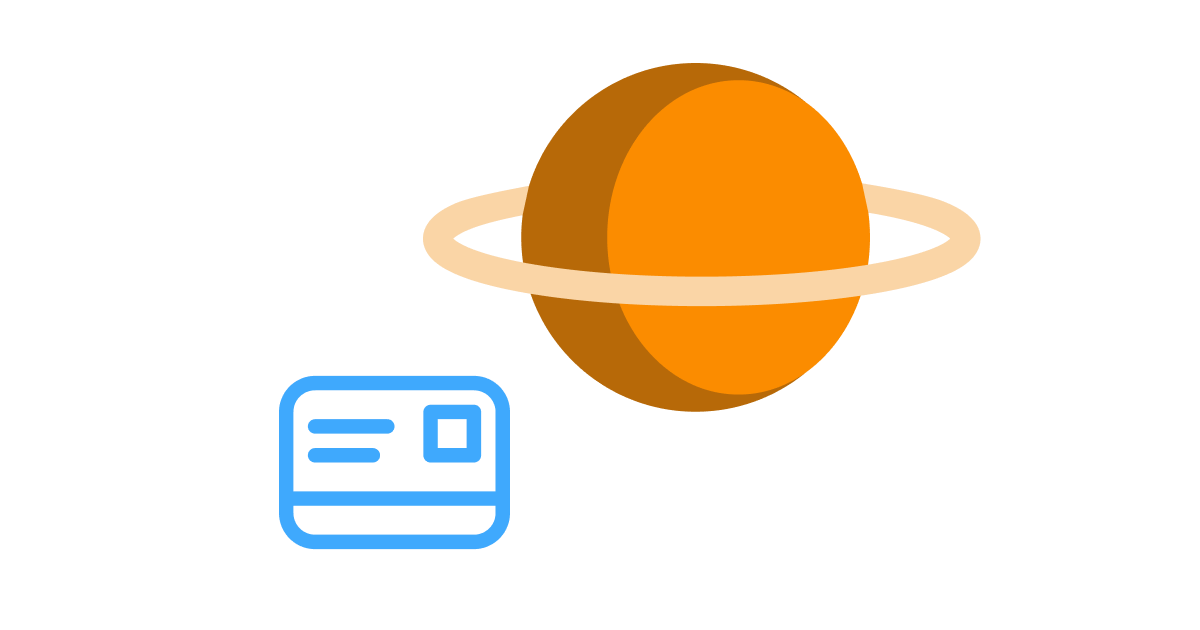
What can reader expect after solving this challenge?
Utilizing the KanBo's features will help address the challenges of managing inter-departmental collaboration effectively. The transparent and systematic tracking of tasks will not only streamline workflows but also promote accountability and responsibility among team members. Furthermore, KanBo will enhance the decision-making process, fostering efficiency, and productivity.
Over a longer period, the organization can expect improved workflow management, quick issue resolution, and overall increased productivity. The insights gained from using KanBo will also help in making informed strategic decisions, leading to better resource allocation and workflow optimization.
In conclusion, with KanBo, a Sterile Manufacturing Quality Auditor in the Pharmaceutical Industry can seamlessly collaborate with various teams and stakeholders, thereby driving quality assurance and continuous improvement.
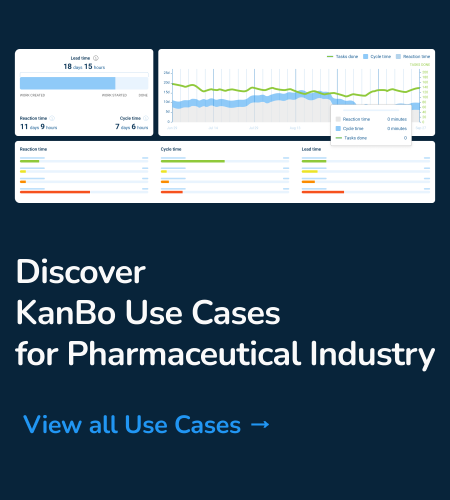