Table of Contents
KanBo – The Pharma-Focused Work Coordination Maestro
Experience ultimate task alignment, communication and collaboration
Trusted globally, KanBo, bridges the gap between management and engineering in complex pharmaceutical organizations. Seamless coordination, advanced project planning, and outstanding leadership are made possible through our versatile software. Stride toward your mission-critical goals with superior collaboration and communication.
KanBo Controlled Temperature Units & Maintenance Specialist in the Pharmaceutical Industry: Tackling Collaboration Challenges for Equipment Efficiency
What do you need to know about this challenge?
In the field of pharmaceuticals, a Controlled Temperature Units & Maintenance Specialist confronts the complex challenge of enhancing equipment capacity while ensuring that operations run smoothly. This role hinges on robust collaboration across multiple departments to adhere to strict GMP, safety, and environmental standards.
What can you do with KanBo to solve this challenge?
KanBo provides a suite of features designed to streamline collaboration and project management:
- Cross-Departmental Scheduling: The Calendar view can be utilized to align maintenance schedules, ensuring that all stakeholders are on the same page and prepared for equipment downtime or inspections.
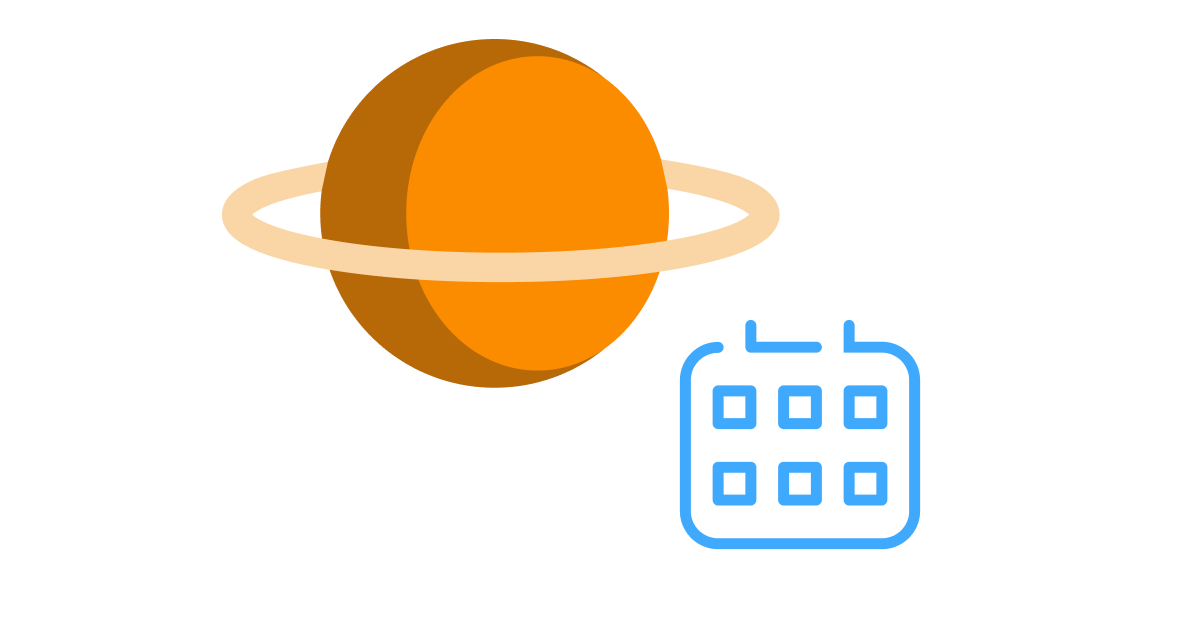
- Efficient Maintenance Management: With the Kanban view, you can visualize the workflow of maintenance requests and repairs, organizing tasks by stage for clear visibility of the equipment status.
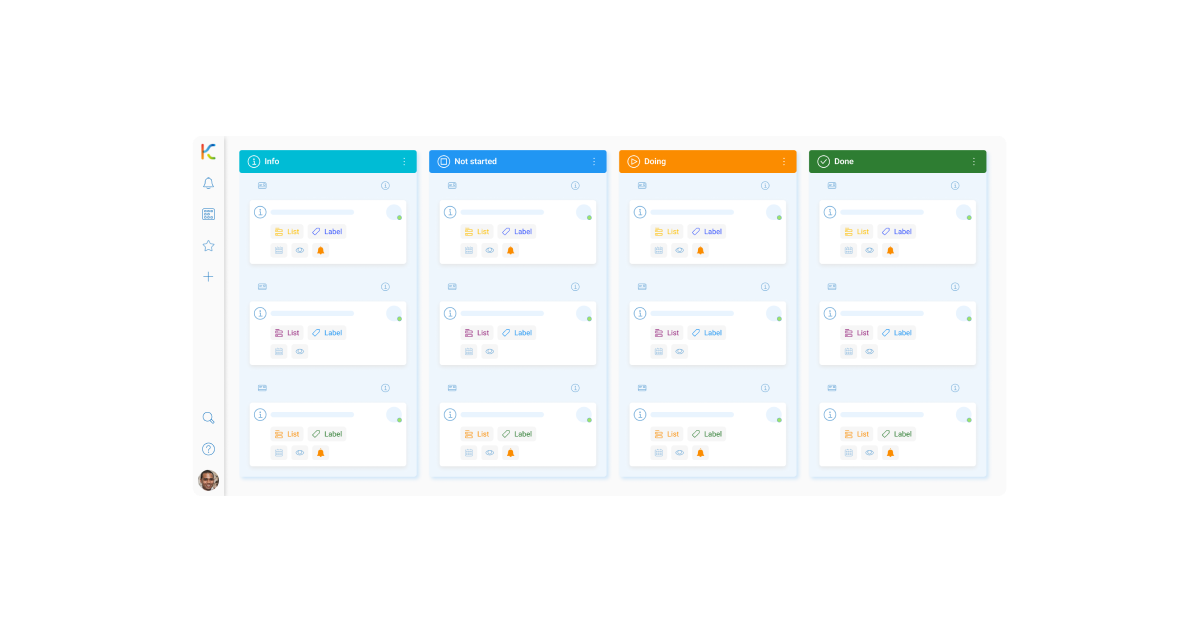
- Preventive Action Planning: Apply the Grouping feature to organize preventive and predictive maintenance activities, ensuring all tasks are grouped and prioritized according to equipment type or urgency.
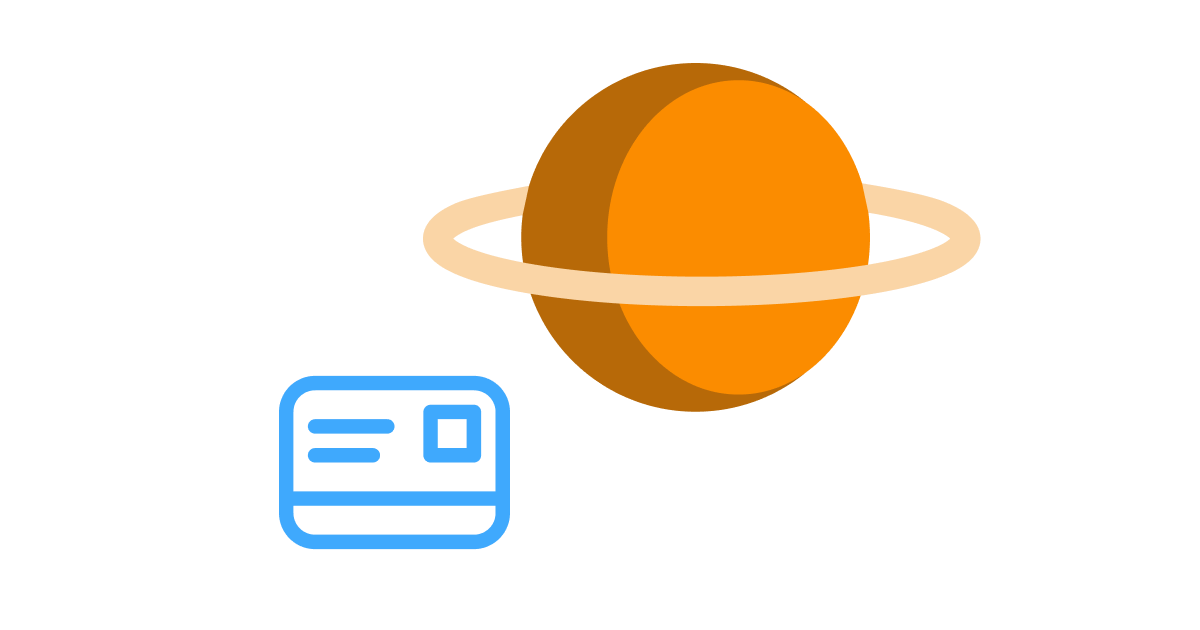
- Strategic Resource Allocation: Use the Gantt Chart view to map out long-term maintenance strategies and predict downtime, balancing the load effectively across your team and resources.
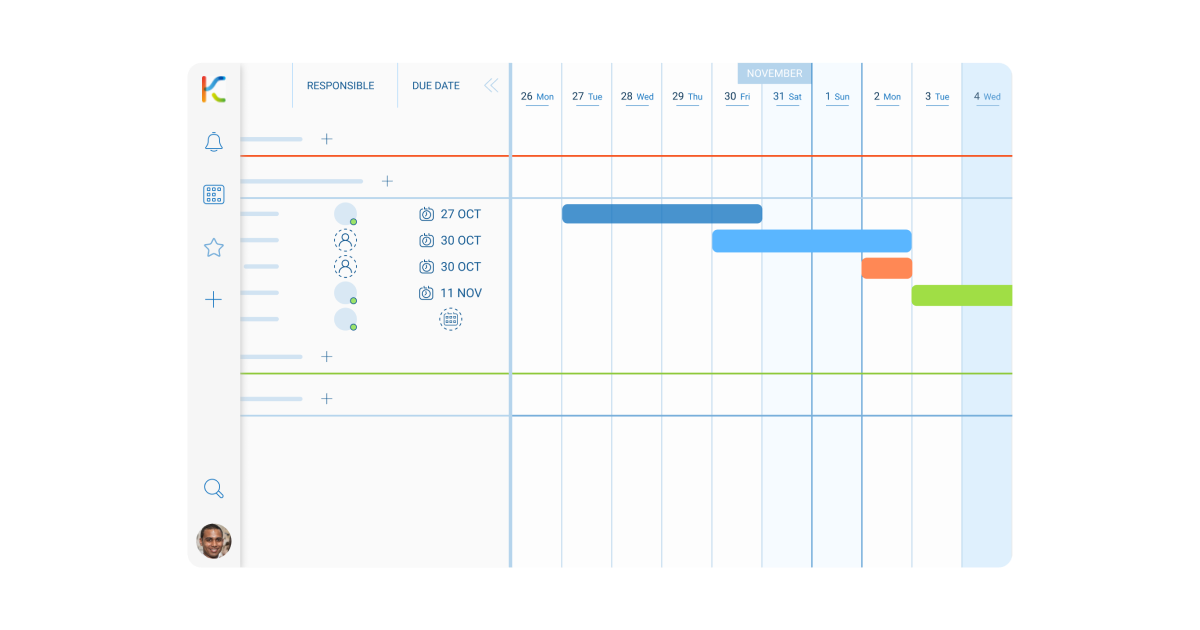
- Real-time Issue Tracking: Employ the Card blocker feature to highlight and address any immediate equipment issues that could potentially disrupt the operation, enabling quick resolution.
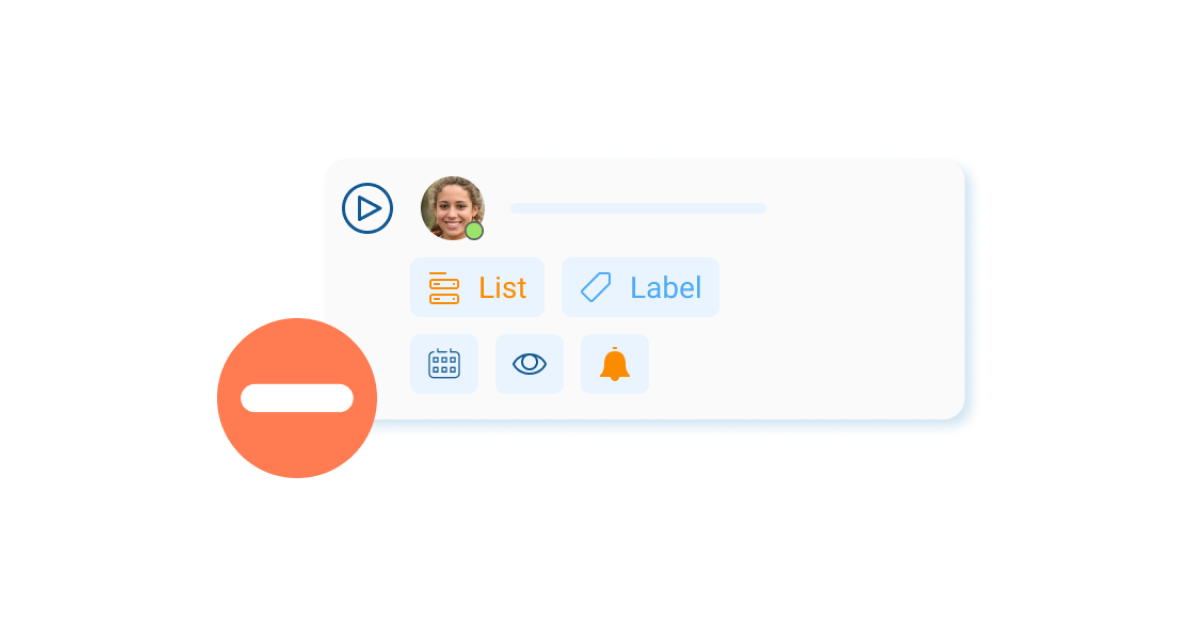
- Transparent Communication: Implement the User activity stream to track participation and follow the maintenance tasks updated by each team member, enhancing accountability and engagement.
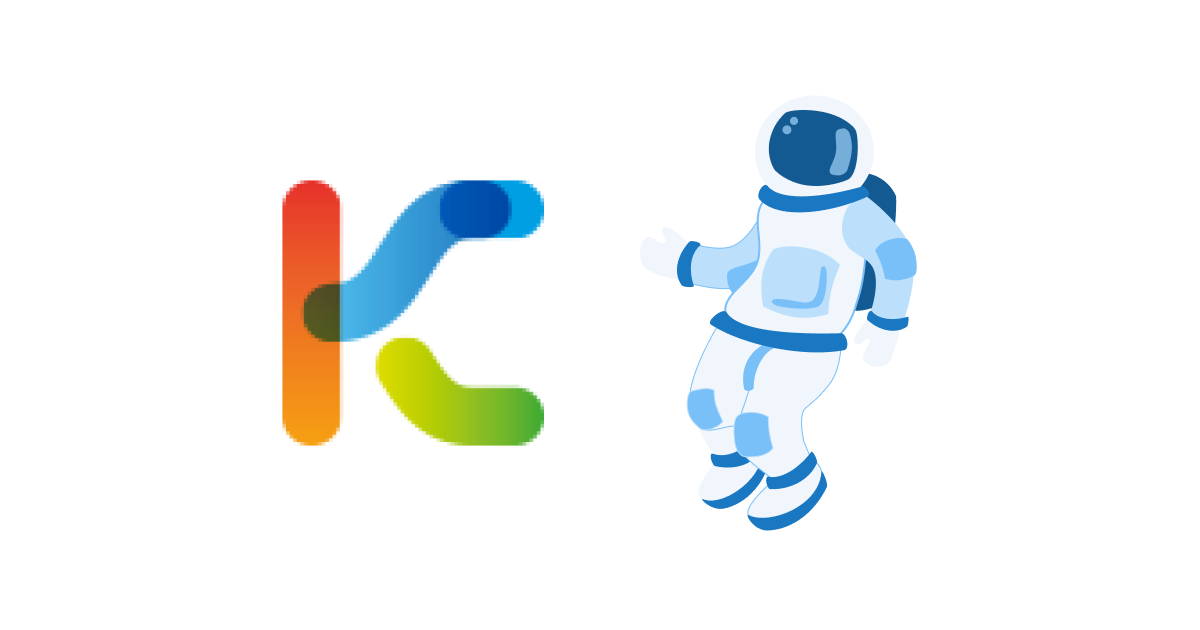
What can you expect after solving this challenge?
By leveraging KanBo to facilitate collaboration among various stakeholders, you can expect improved operational efficiency and reduced equipment downtime in the long term. Processes become more transparent and accountable, leading to a better understanding of equipment performance and more effective maintenance schedules. Looking ahead, continued enhancements to KanBo's functionality will aim to provide even greater predictive insights, allowing for proactive maintenance that can help extend the life of Controlled Temperature Units and reduce costs associated with unexpected equipment failures. The use of KanBo fosters a culture of continuous improvement and inter-departmental synergy, essential for any Controlled Temperature Units & Maintenance Specialist.
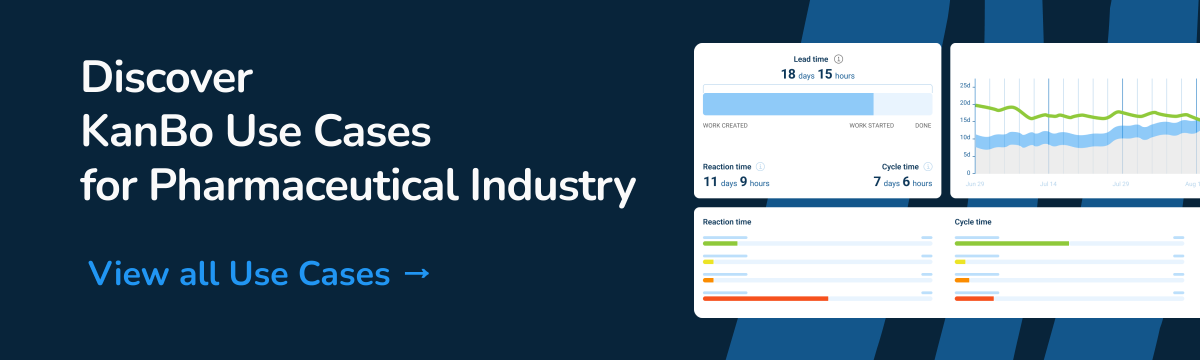
Table of Contents
KanBo – The Pharma-Focused Work Coordination Maestro
Experience ultimate task alignment, communication and collaboration
Trusted globally, KanBo, bridges the gap between management and engineering in complex pharmaceutical organizations. Seamless coordination, advanced project planning, and outstanding leadership are made possible through our versatile software. Stride toward your mission-critical goals with superior collaboration and communication.
KanBo Controlled Temperature Units & Maintenance Specialist in the Pharmaceutical Industry: Tackling Collaboration Challenges for Equipment Efficiency
What do you need to know about this challenge?
In the field of pharmaceuticals, a Controlled Temperature Units & Maintenance Specialist confronts the complex challenge of enhancing equipment capacity while ensuring that operations run smoothly. This role hinges on robust collaboration across multiple departments to adhere to strict GMP, safety, and environmental standards.
What can you do with KanBo to solve this challenge?
KanBo provides a suite of features designed to streamline collaboration and project management:
- Cross-Departmental Scheduling: The Calendar view can be utilized to align maintenance schedules, ensuring that all stakeholders are on the same page and prepared for equipment downtime or inspections.
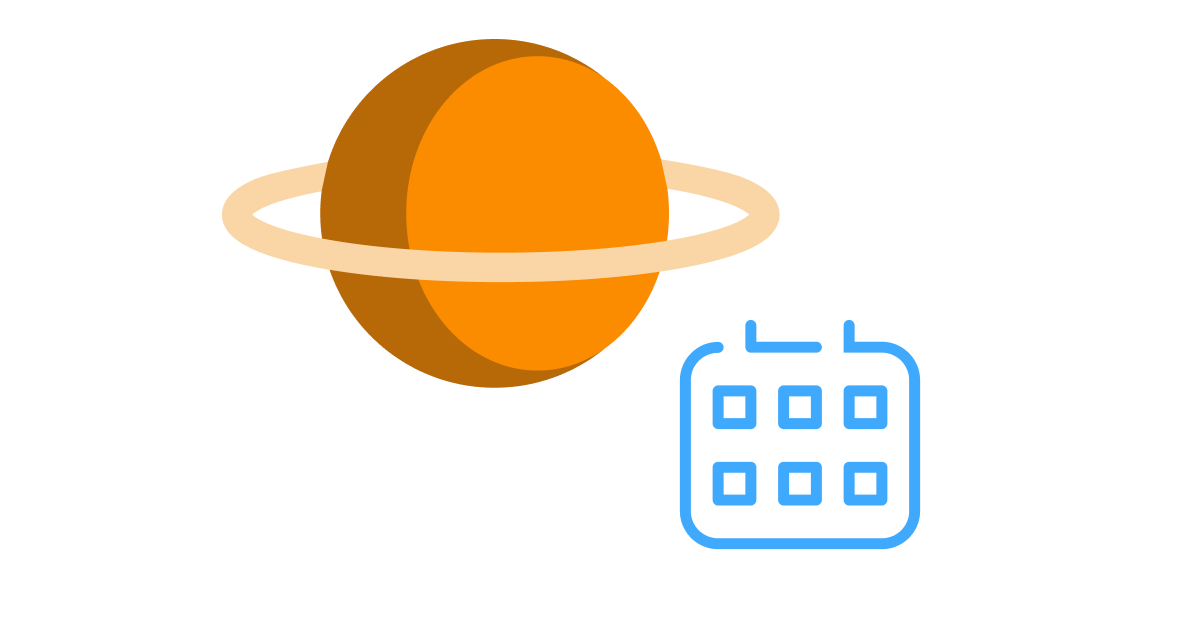
- Efficient Maintenance Management: With the Kanban view, you can visualize the workflow of maintenance requests and repairs, organizing tasks by stage for clear visibility of the equipment status.
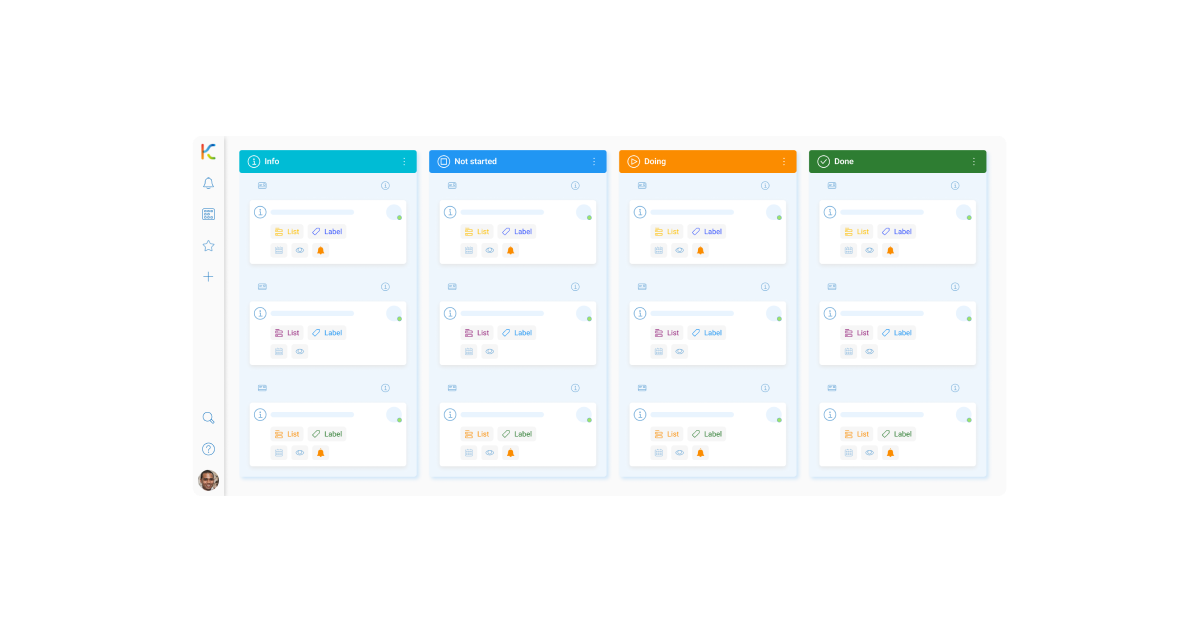
- Preventive Action Planning: Apply the Grouping feature to organize preventive and predictive maintenance activities, ensuring all tasks are grouped and prioritized according to equipment type or urgency.
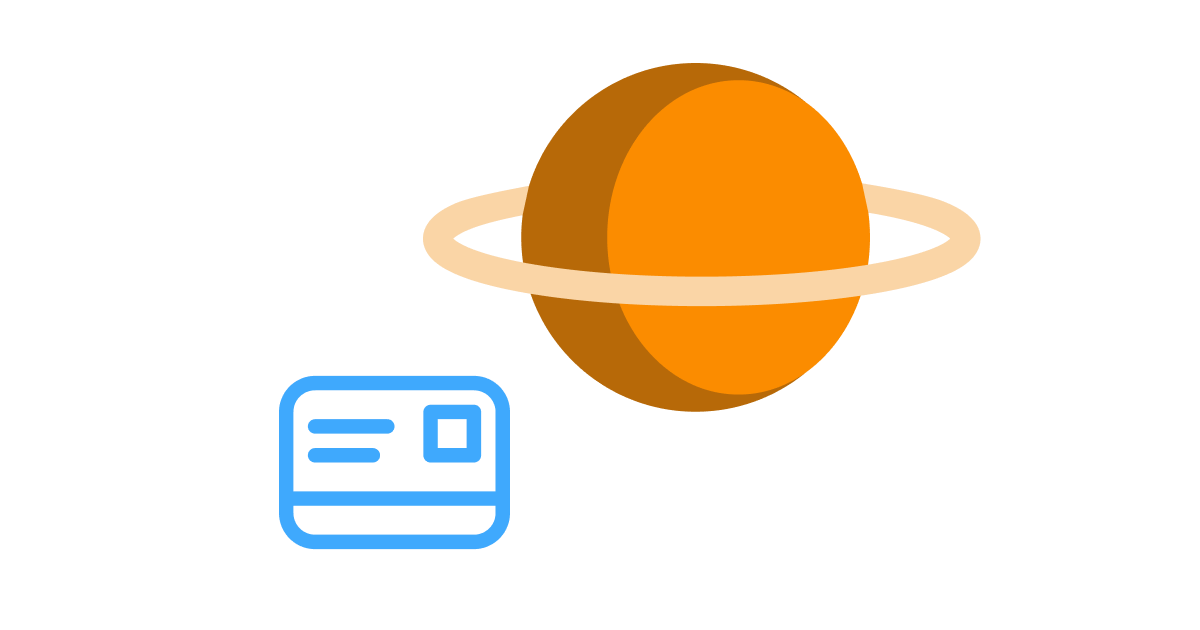
- Strategic Resource Allocation: Use the Gantt Chart view to map out long-term maintenance strategies and predict downtime, balancing the load effectively across your team and resources.
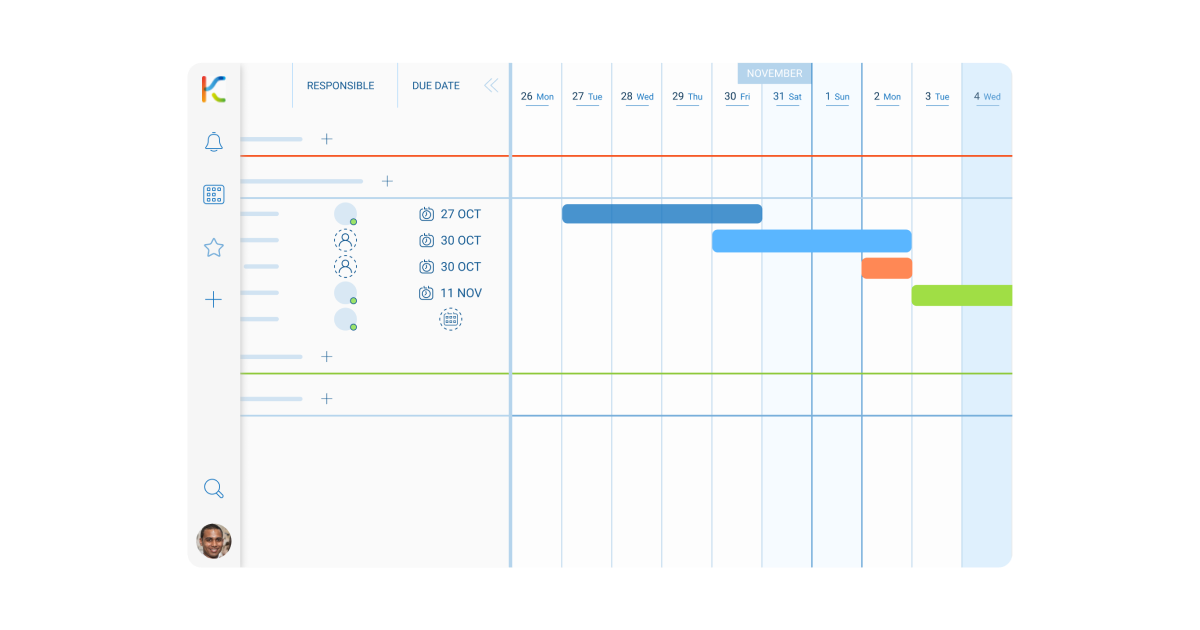
- Real-time Issue Tracking: Employ the Card blocker feature to highlight and address any immediate equipment issues that could potentially disrupt the operation, enabling quick resolution.
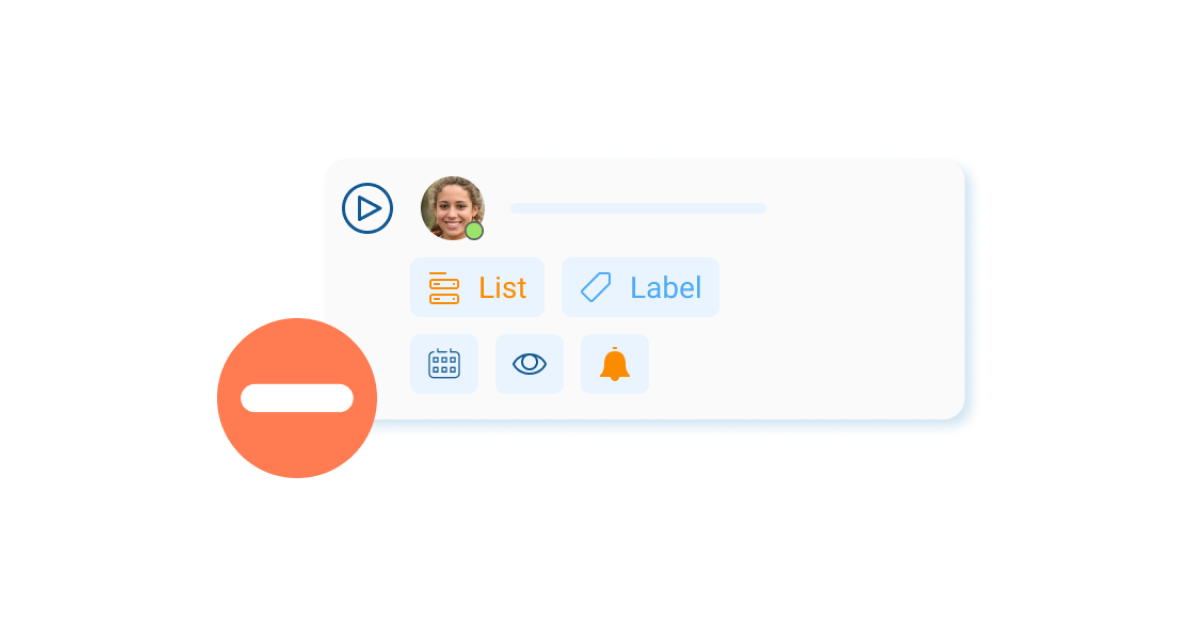
- Transparent Communication: Implement the User activity stream to track participation and follow the maintenance tasks updated by each team member, enhancing accountability and engagement.
What can you expect after solving this challenge?
By leveraging KanBo to facilitate collaboration among various stakeholders, you can expect improved operational efficiency and reduced equipment downtime in the long term. Processes become more transparent and accountable, leading to a better understanding of equipment performance and more effective maintenance schedules. Looking ahead, continued enhancements to KanBo's functionality will aim to provide even greater predictive insights, allowing for proactive maintenance that can help extend the life of Controlled Temperature Units and reduce costs associated with unexpected equipment failures. The use of KanBo fosters a culture of continuous improvement and inter-departmental synergy, essential for any Controlled Temperature Units & Maintenance Specialist.
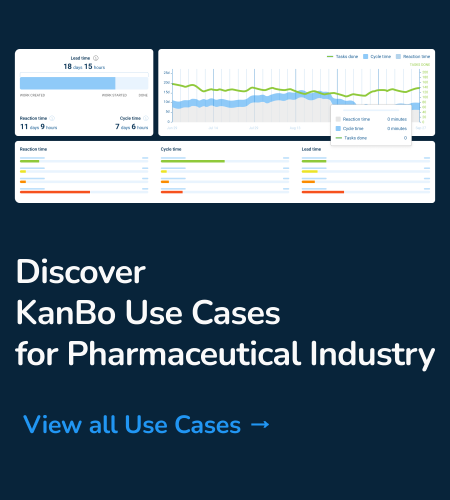