Table of Contents
KanBo – The Pharma-Focused Work Coordination Maestro
Experience ultimate task alignment, communication and collaboration
Trusted globally, KanBo, bridges the gap between management and engineering in complex pharmaceutical organizations. Seamless coordination, advanced project planning, and outstanding leadership are made possible through our versatile software. Stride toward your mission-critical goals with superior collaboration and communication.
KanBo Quality Assurance Associate - Analytical Specialist in the Pharmaceutical Industry: Tackling Collaboration and Compliance Challenges
What do you need to know about this challenge?
In the stringent reality of the pharmaceutical industry, a Quality Assurance Associate - Analytical Specialist faces a significant challenge: maintaining compliance with Good Manufacturing Practice (GMP) regulations while managing analytical deviations and corrective and preventive actions (CAPA) within a collaborative team setting. This complex task requires a meticulous approach to quality assurance and a transparent, organized system that facilitates teamwork and communication.
What can you do with KanBo to solve this challenge?
KanBo facilitates the management of GMP and CAPA procedures, streamlining collaboration among Quality Assurance teams:
- Card: Organize and track quality assurance tasks, deviations, and CAPA steps using KanBo cards that keep information centralized and accessible

- Document source: Integrate critical quality documentation into cards so all team members have easy access to GMP standards, SOPs, and CAPA records

- Card activity stream: Gain real-time insights into actions taken on quality-related tasks to keep track of investigations, reports, and resolution statuses
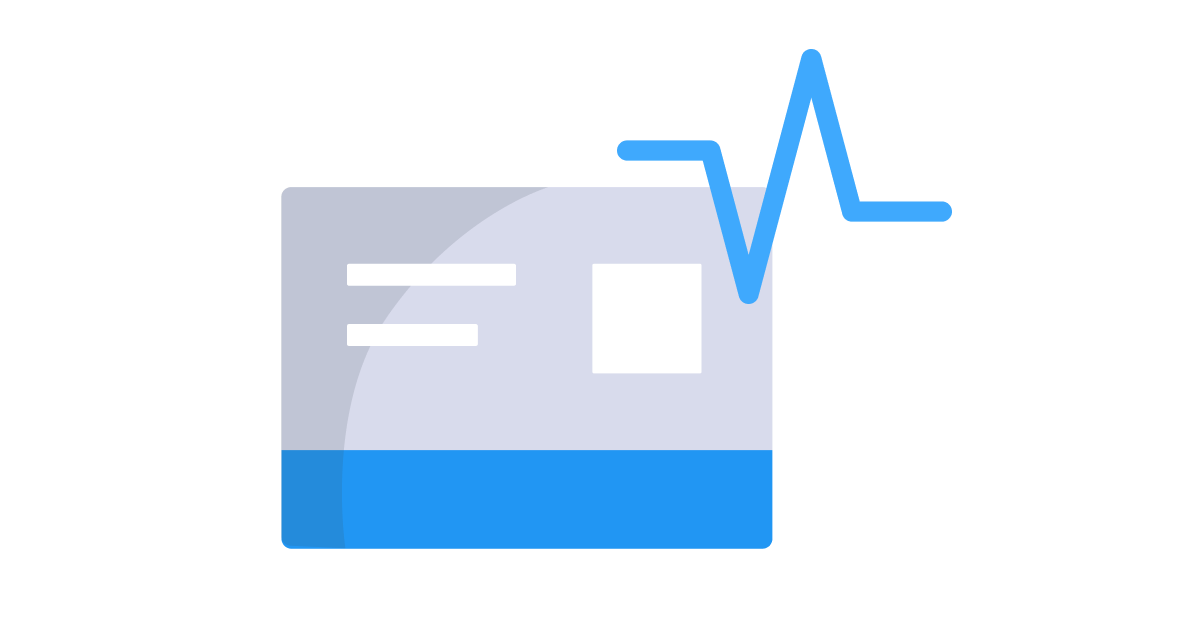
- Card status: Monitor the progress of quality assurance activities by categorizing cards based on their current phase, such as 'In Review', 'Action Needed', or 'Completed'
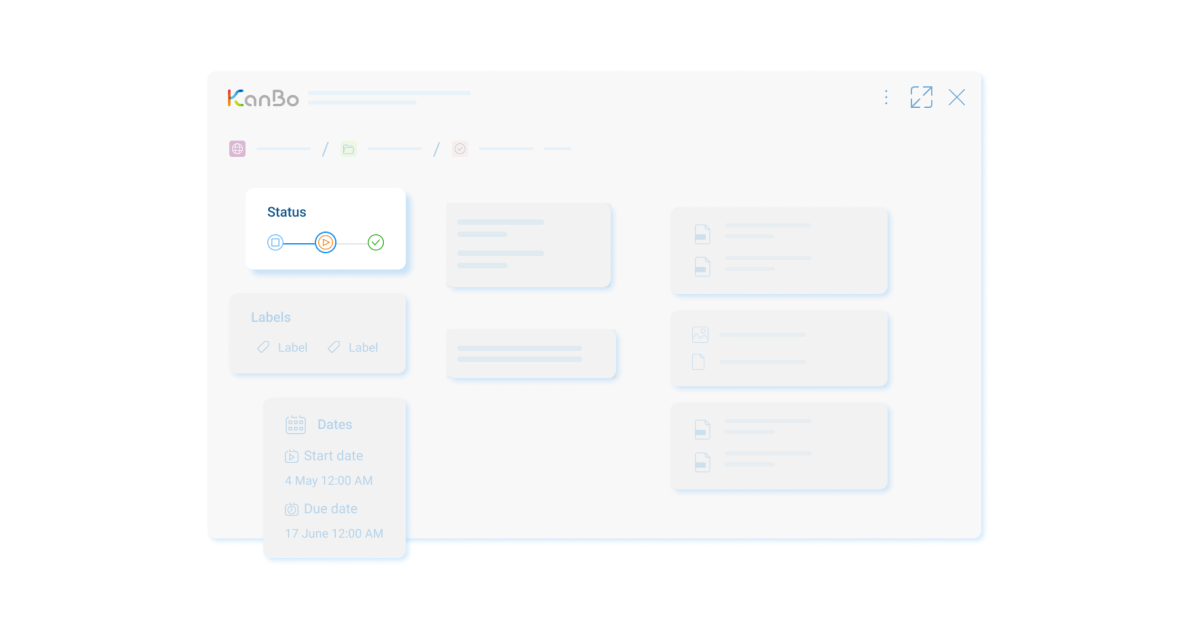
- Reminder: Ensure that no deadlines are missed by setting personal reminders for follow-ups, report submissions, and review dates
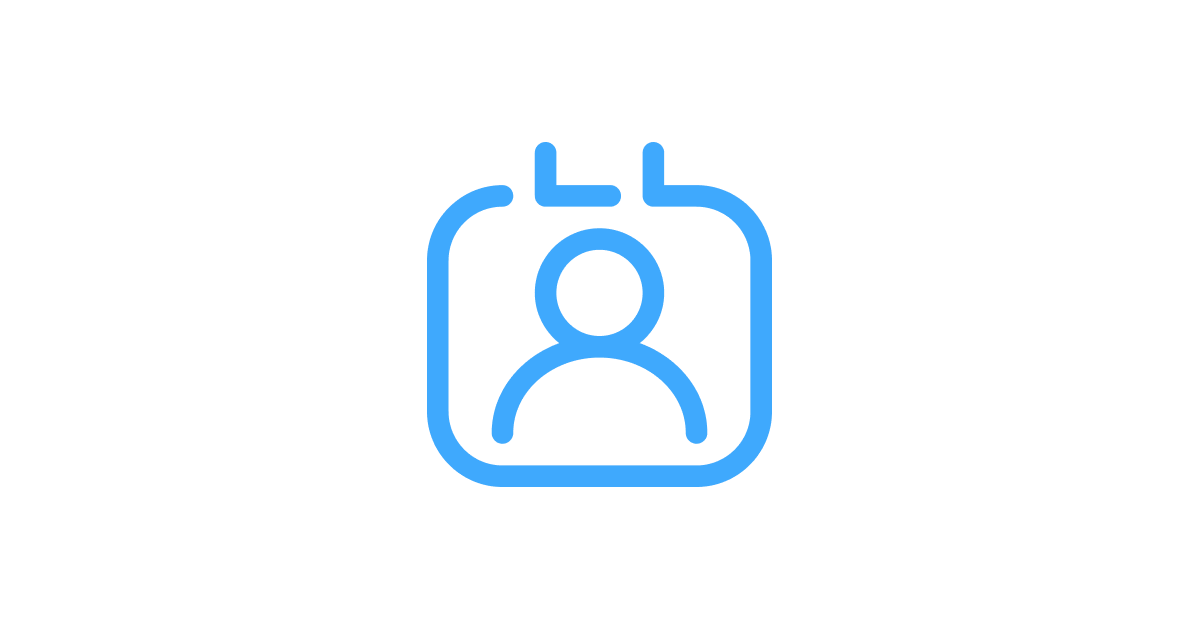
- Card relation: Create dependencies between tasks to easily manage the flow of activities from identification of deviations to the implementation of CAPA

- Filtering cards: Quickly locate specific quality assurance tasks or documentation by filtering cards based on keywords, users, or custom criteria
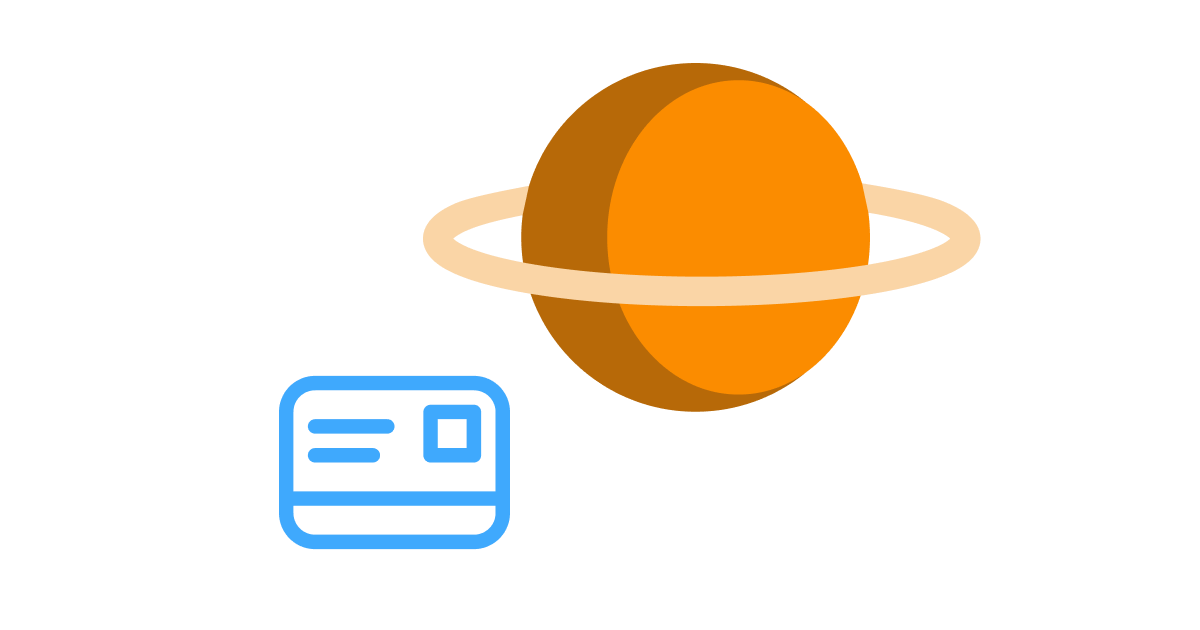
- KanBo Search: Find anything within the quality assurance space rapidly—be it documents, cards, or specific process details—using advanced search capabilities
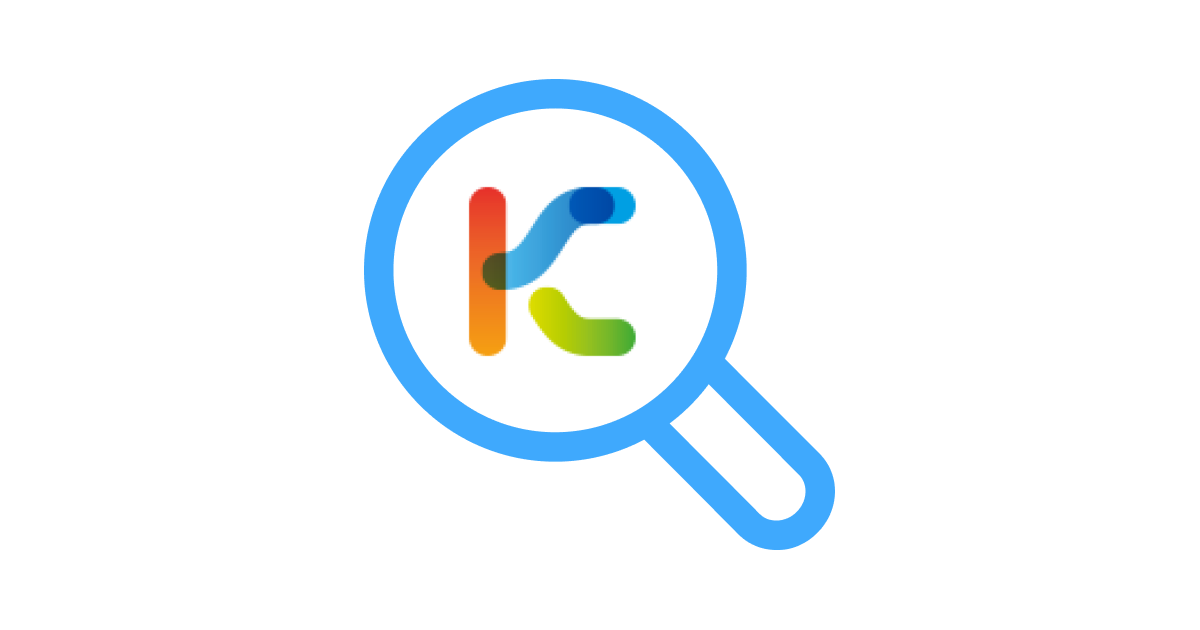
What can you expect after solving this challenge?
Embracing KanBo's robust features for managing quality assurance in the pharmaceutical industry can significantly streamline the intricate procedures of GMP compliance and deviation management. Long-term benefits include fostering a culture of proactive quality maintenance, improved audit readiness, and accelerated issue resolution. As quality processes are documented and tracked effectively, teams can anticipate a steady reduction in compliance breaches and overall risk.
Leveraging the systematic approach offered by KanBo's features, future enhancements may include more sophisticated analytics for quality performance metrics, deeper integration with laboratory information management systems, and even more granular control over quality-related workflows. As organizations evolve, KanBo stands ready to meet their growing compliance and collaboration needs with continuous innovation and adaptability.
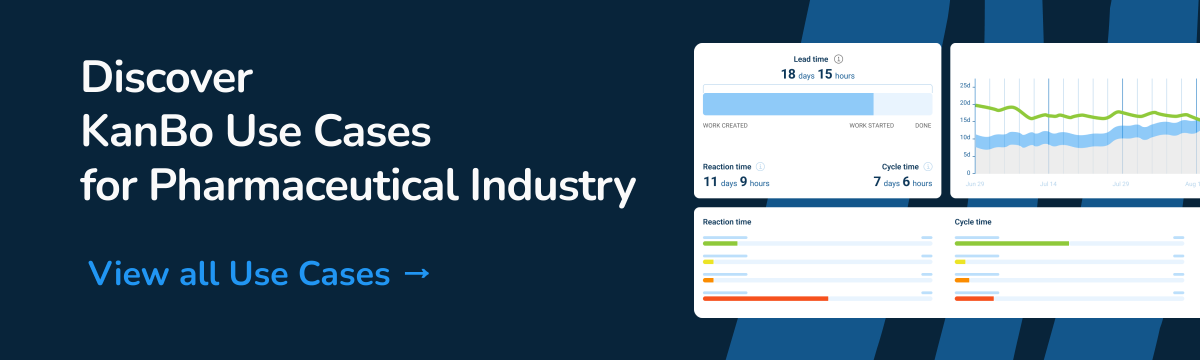
Table of Contents
KanBo – The Pharma-Focused Work Coordination Maestro
Experience ultimate task alignment, communication and collaboration
Trusted globally, KanBo, bridges the gap between management and engineering in complex pharmaceutical organizations. Seamless coordination, advanced project planning, and outstanding leadership are made possible through our versatile software. Stride toward your mission-critical goals with superior collaboration and communication.
KanBo Quality Assurance Associate - Analytical Specialist in the Pharmaceutical Industry: Tackling Collaboration and Compliance Challenges
What do you need to know about this challenge?
In the stringent reality of the pharmaceutical industry, a Quality Assurance Associate - Analytical Specialist faces a significant challenge: maintaining compliance with Good Manufacturing Practice (GMP) regulations while managing analytical deviations and corrective and preventive actions (CAPA) within a collaborative team setting. This complex task requires a meticulous approach to quality assurance and a transparent, organized system that facilitates teamwork and communication.
What can you do with KanBo to solve this challenge?
KanBo facilitates the management of GMP and CAPA procedures, streamlining collaboration among Quality Assurance teams:
- Card: Organize and track quality assurance tasks, deviations, and CAPA steps using KanBo cards that keep information centralized and accessible

- Document source: Integrate critical quality documentation into cards so all team members have easy access to GMP standards, SOPs, and CAPA records

- Card activity stream: Gain real-time insights into actions taken on quality-related tasks to keep track of investigations, reports, and resolution statuses
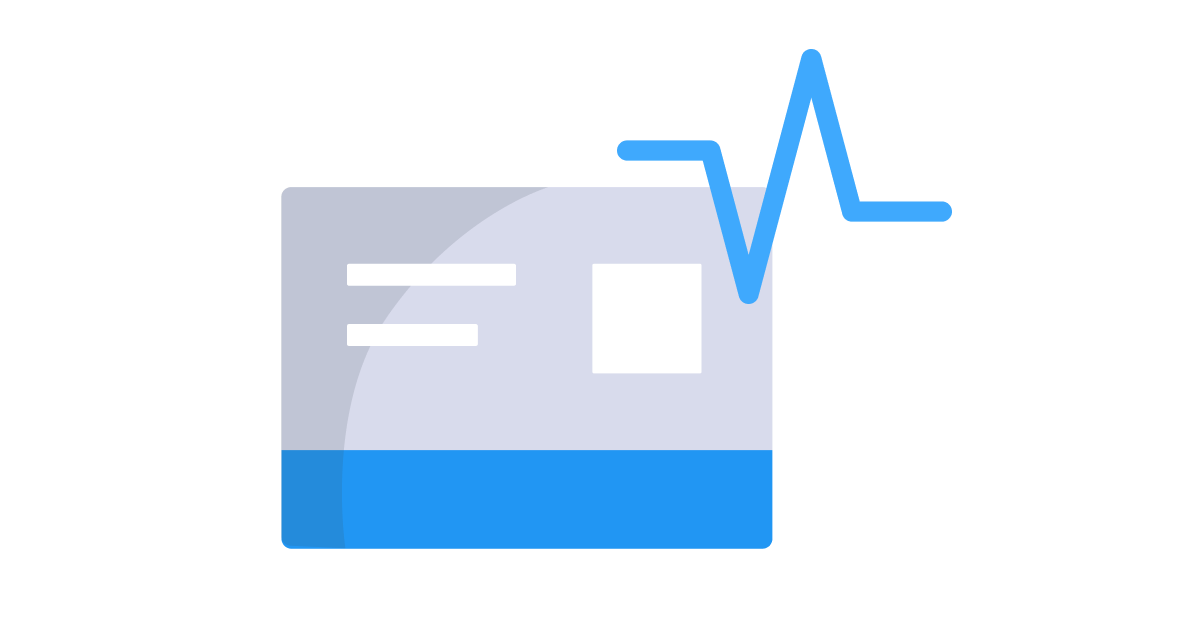
- Card status: Monitor the progress of quality assurance activities by categorizing cards based on their current phase, such as 'In Review', 'Action Needed', or 'Completed'
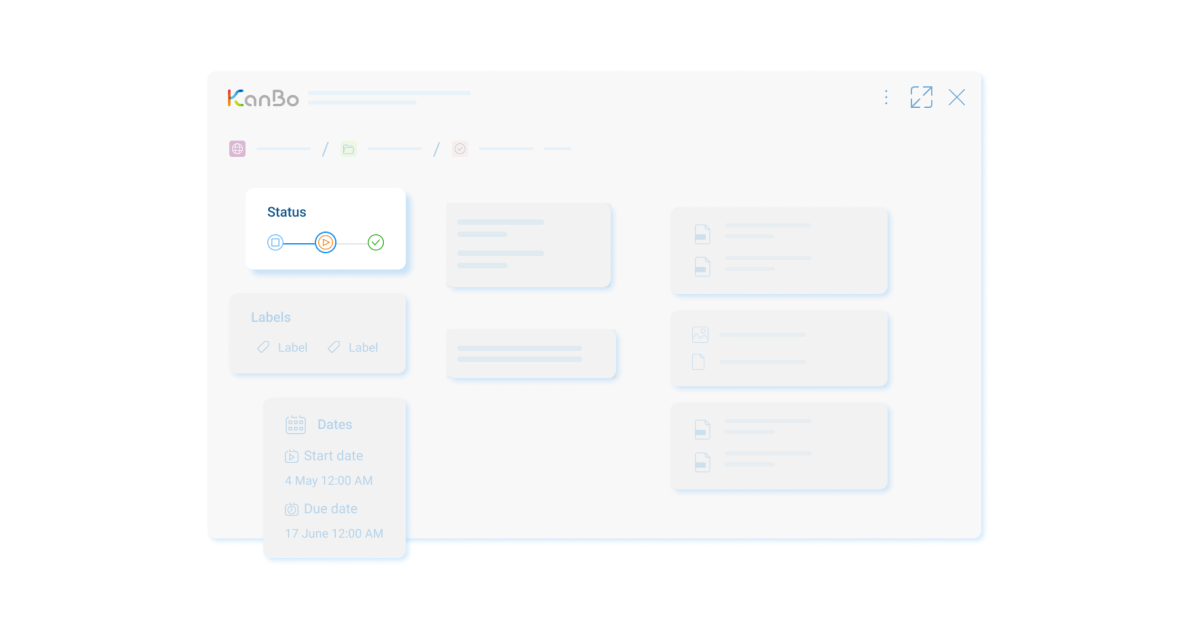
- Reminder: Ensure that no deadlines are missed by setting personal reminders for follow-ups, report submissions, and review dates
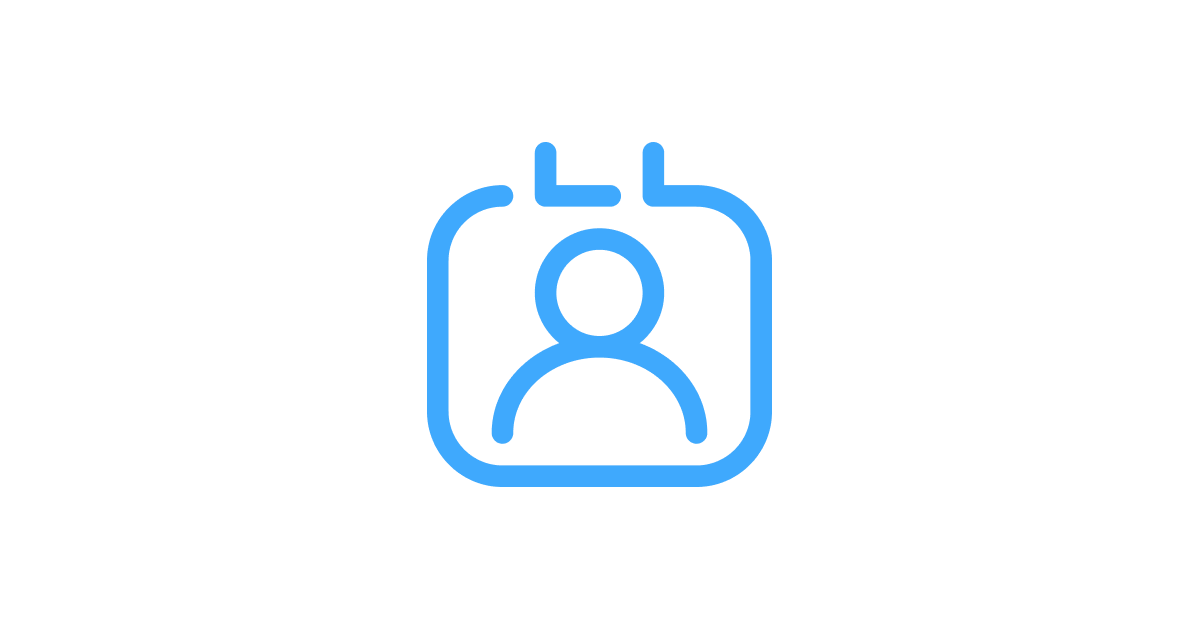
- Card relation: Create dependencies between tasks to easily manage the flow of activities from identification of deviations to the implementation of CAPA

- Filtering cards: Quickly locate specific quality assurance tasks or documentation by filtering cards based on keywords, users, or custom criteria
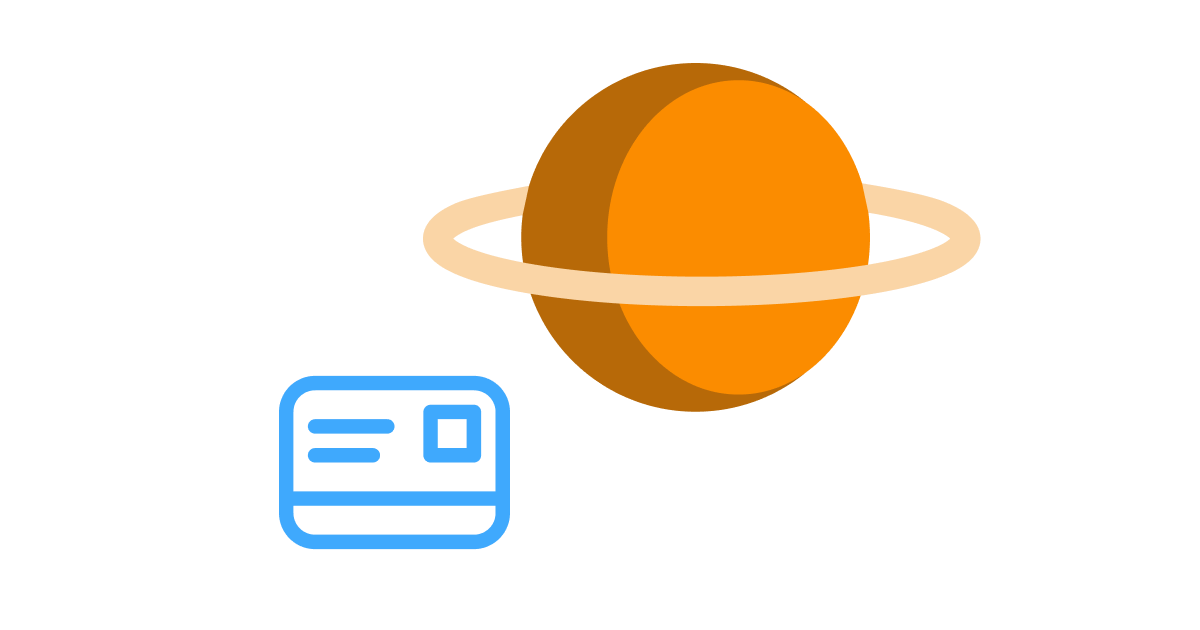
- KanBo Search: Find anything within the quality assurance space rapidly—be it documents, cards, or specific process details—using advanced search capabilities
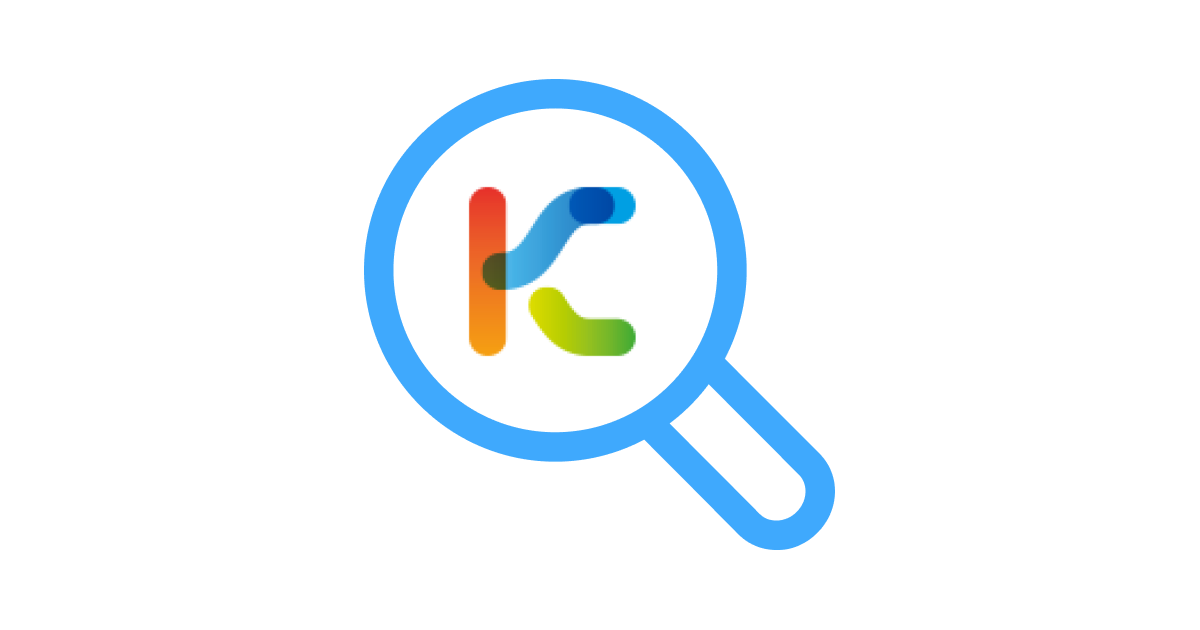
What can you expect after solving this challenge?
Embracing KanBo's robust features for managing quality assurance in the pharmaceutical industry can significantly streamline the intricate procedures of GMP compliance and deviation management. Long-term benefits include fostering a culture of proactive quality maintenance, improved audit readiness, and accelerated issue resolution. As quality processes are documented and tracked effectively, teams can anticipate a steady reduction in compliance breaches and overall risk.
Leveraging the systematic approach offered by KanBo's features, future enhancements may include more sophisticated analytics for quality performance metrics, deeper integration with laboratory information management systems, and even more granular control over quality-related workflows. As organizations evolve, KanBo stands ready to meet their growing compliance and collaboration needs with continuous innovation and adaptability.
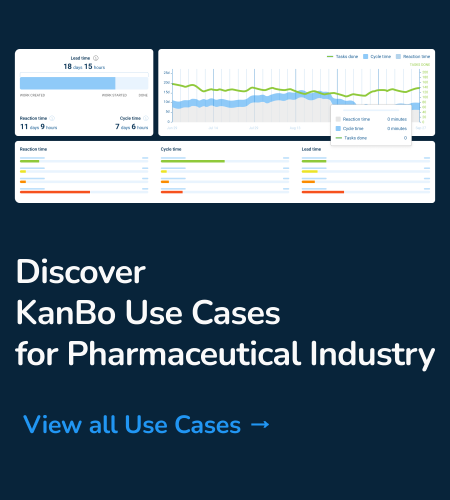